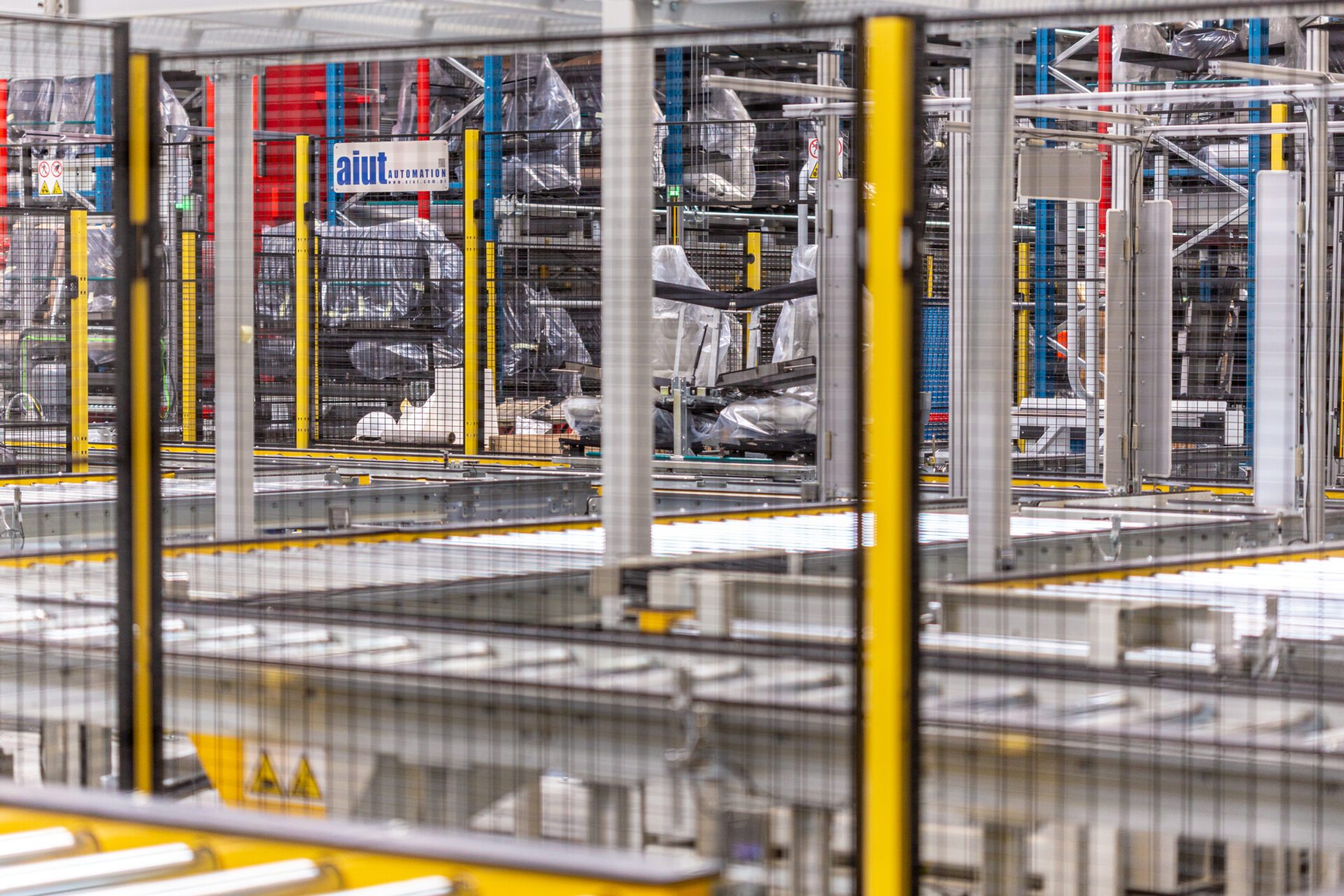
How warehouse sortation systems are changing logistics?
From this article, you will learn:
-
what are the tasks of a warehouse sorting system?
-
what benefits automated sortation systems provide to businesses?
-
what parameters should be considered to select the right sortation system?
-
about examples of automatic sorters used in the market.
-
about the challenges associated with implementing sorting systems in warehouses and distribution centers.
-
about the implementation of an automated shipping sorter by AIUT.
In an era of increasing competition and rising customer expectations, warehouse operations efficiency has become a key success factor for many companies. The intense development of e-commerce orders and the increase in the volume of packages handled contribute to the search for more efficient solutions for warehouse automation. One such solution is a warehouse sortation system, which speed up the picking and issuing of goods process, thereby reducing delivery times and order fulfillment for customers.
In this article, we will look at how a warehouse sortation system works, analyze its key parameters, discuss the benefits that automated sortation systems provide to companies, and address important issues related to their implementation process.
What are warehouse sorting systems used for?
Automated sorters enable efficient warehouse operations and virtually error-free item picking & packing segregation. They operate according to pre-set parameters, allowing sorting operations to be completed in less time than manual sorting processes. Sorters help companies at many points in the manufacturing, logistics, and supply chain, including picking, final sortation as packages leave the warehouse, and the returns processes. They use advanced technologies such as RFID readers, autonomous mobile robots, vision systems, and robotic solutions to speed up logistics processes while reducing the risk of errors and improving the overall efficiency of warehouse operations.
When is it worth investing in automated warehouse sortation systems? Read expert opinions on www.logistyczny.com.
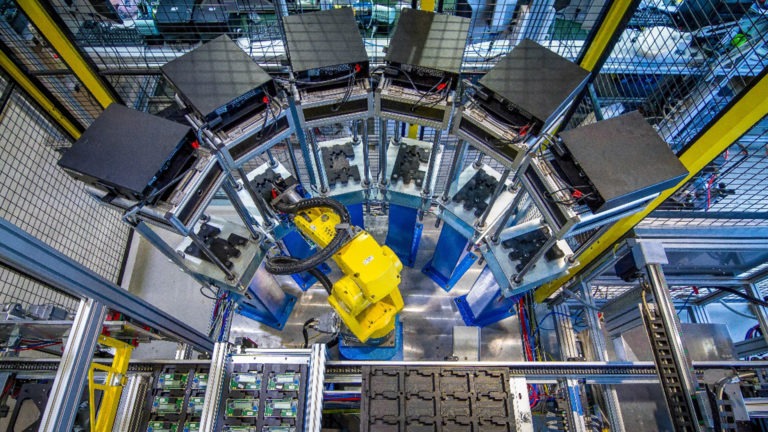
Benefits of automated sorting systems
Automated sorting brings several benefits, including:
- increased efficiency of the order fulfillment and sorting process,
- shortened handling and distribution time of goods,
- accelerated speed sortation,
- error reduction,
- optimization of warehouse space,
- improved work ergonomics.
Warehouse sortation parameters — how to choose the right sortation system?
When selecting an automated warehouse sortation system, several key parameters must be considered to ensure the best fit for the specific operational needs of the warehouse. The priority is the sortation system's capacity, i.e., the ability of the sorter to handle a certain number of product units in a given amount of time. When picking goods from a large area, from different zones, it is worthwhile to group orders and then transfer individual goods to further processes in the next stage. It is also important to match the type of sorter to the dimensions of the goods, such as weight, size, type of packaging, and material being sorted. Another significant key parameter of warehouse sortation systems is the ability to integrate with the existing IT environment, i.e., the appropriate system for managing the sortation process from the WMS or ERP system level. Last but not least, an essential factor to consider is the available warehouse space, to optimally plan the physical flow of goods and the available space for the installation of the sortation system.
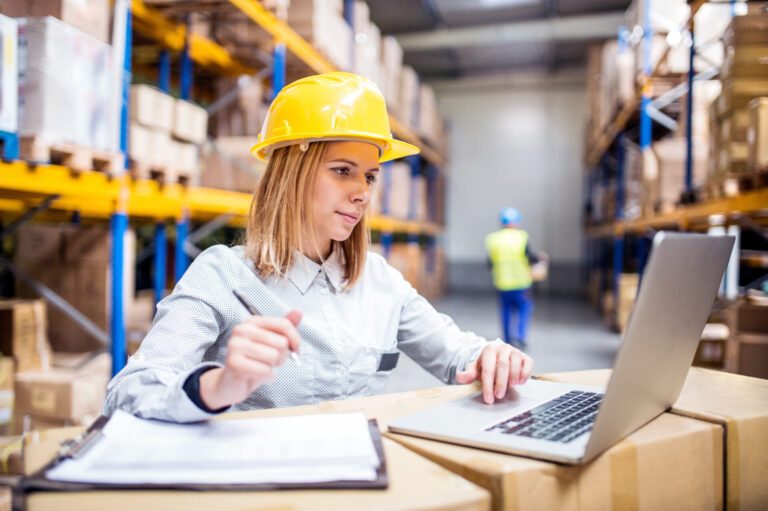
Examples of sorter types available on the market
Depending on operational needs and the characteristics of the sorted goods, we can distinguish several basic types of sorters, such as:
Cross-belt sorter
A cross belt sorter allows goods to be conveyed around curves, horizontally, or on an inclined plane, both up and down, creating a flexible sortation system in various dimensions. These sorters are most commonly found in linear, oval, or U-shaped forms.
Narrow-belt sorter
It consists of a series of narrow belt conveyors arranged in parallel. High-friction rollers are attached to them, allowing bidirectional sorting of parcels at a 90-degree angle to the right or left.
Wheel sorter (also called as Switch sorter)
This is a sorter that consists of conveyor modules, allowing it to be easily expanded and configured to meet changing needs. Sorters of this type use a series of rotating pins, rollers, or wheels to physically divert items to different outputs.
Bombay sorters (otherwise known as Split-Tray or just Tray sorters)
Bombay sorters are suitable for sorting flat goods such as textiles or paper products. They have movable trays with multiple segments that open at the bottom. When the tray passes over the appropriate destination, it opens and drops the product into a container or onto a conveyor belt below, hence the name, which refers to aircraft releasing bombs. The tray sorter is capable of handling goods for inbound and outbound sorting processes. They are not suitable for segregating fragile and delicate items but are often used in the fashion industry.
Shoe sorter
It allows the sorting of products of different dimensions. The shoe sorter is used in processes where higher efficiency is required.
Designing sorting lines and choosing automated sortation technologies tailored to the needs of the client
Choosing an appropriate automated sortation system requires a holistic approach that considers not only the current but also the future needs of the warehouse, ensuring the ability to scale and adapt the system to changing operational requirements. The types mentioned above are just examples of solutions for standard loads. With the help of an integrator, such solutions can be configured and expanded, taking into account necessary parameters such as operational efficiency, type, weight, and dimensions of the goods to be sorted, and available warehouse space.
In cases where a company wants to automatically sort goods of non-standard size, length, or lack of packaging, integrators will design and implement a solution tailored to the individual needs of the customer's facility. At AIUT, that's how we work. We understand the customer's problem, review the market for warehouse automation equipment, and propose a system that will achieve the expected efficiency and handle the specified flow of goods. We approach each customer individually and create an automated warehouse solution tailored to their needs.
In our solutions, thanks to traceability systems, we enable tracking and full control of the sorting process. Data from each stage of sorting is archived for future analysis and control, and photos taken of parcels leaving the sorter allow full identification of shipments and their condition at the time of issue. Read more about our offer of automated sorters here.
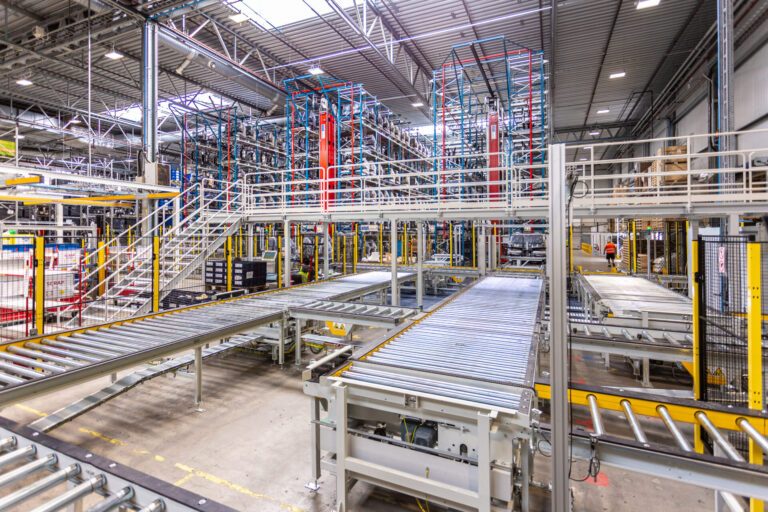
Challenges in implementing warehouse sorting systems
Despite the many benefits, implementing efficient sortation systems presents some challenges. One of the main ones is the high investment cost. Purchasing and installing advanced sortation equipment requires a significant financial investment, which can be a barrier for many companies. Integrating new equipment with existing warehouse and IT systems can also be complicated. The need to adapt new technologies to current processes and infrastructure requires careful planning and often specialized knowledge. Staff training is another challenge. To realize the full potential of sortation equipment, employees must be properly trained in its operation and maintenance. This includes both machine operators and those responsible for supervising the sortation process. Finally, there is the need for continuous adaptation and evolution. The market and technologies are constantly changing, so automated sortation solutions must be flexible and able to adapt to future business and technological needs.
However, despite these challenges, the benefits of implementing automated sortation systems are significant, and investing in an optimized sortation process can pay long-term dividends in the form of increased efficiency, reduced errors, and improved overall operational performance.
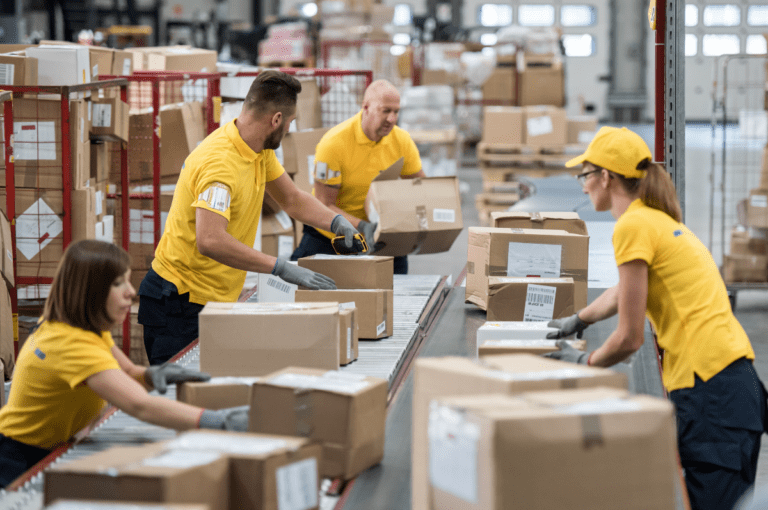
Example of implementing a warehouse sortation system
For an international logistics operator based in central Poland, AIUT designed and built an automated shipping sorter covering an area of over 3,000 sqm. The system automatically transports goods from storage stations to operator completion stations where final order completion takes place. The solution includes system information to exclude or load specific operator stations. Then, using integrated vision systems and RFID readers, each package ready for shipment is identified, sorted, and automatically routed to the appropriate warehouse release points, from where it is transported to the final recipient. The solution has been integrated with material flow control (MFC) and warehouse management systems (WMS) to execute orders according to shipping priorities and continuously track inventory levels.
Summary
Modern warehouse sorters are key elements of automated warehouse and distribution center systems, helping to efficiently sort and direct goods to the appropriate shipping or storage zones. For a company, the most important condition for implementing an automated sortation system is to increase the efficiency of processes, measured by the number of orders processed in a given time unit. Thanks to automated sorters, the speed of order processing per hour can be increased many times over, which is one of the main factors in the decision to invest in these devices. In addition, automated sortation systems lead to lower operating costs and greater efficiency of other logistics processes, which translates into a faster return on investment.

Do you want to implement automated warehouse sorters? Let us know!
As an integrator of automation and robotics solutions, we are responsible for the comprehensive implementation of projects for automated warehouses and intralogistics systems. By combining unique engineering skills, we build advanced solutions for industry and logistics, tailoring the project to the individual requirements of the client.