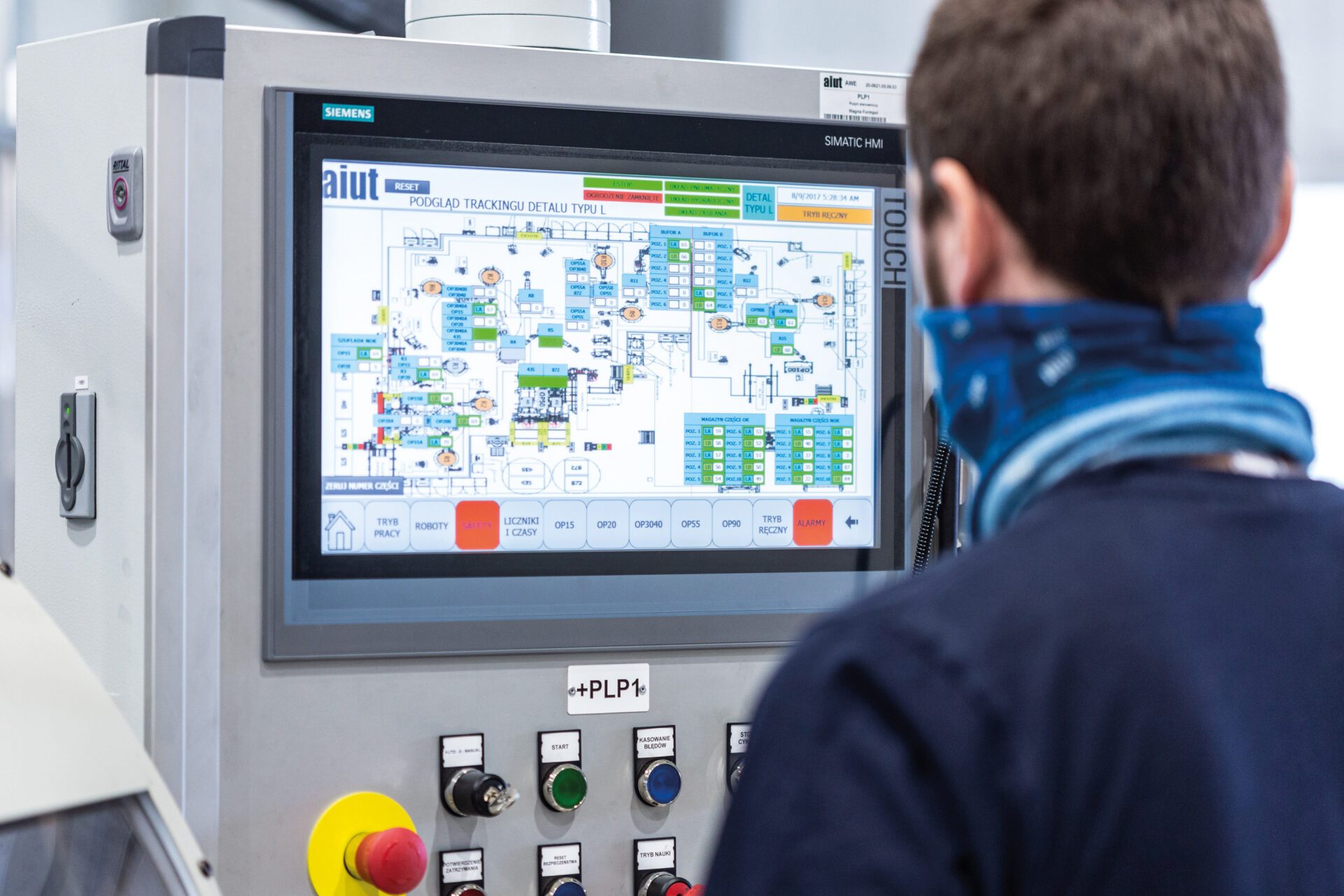
Tworzymy świat maszyn, pozwólmy im się komunikować
Współczesne zakłady produkcyjne i magazyny operują w dynamicznym, coraz bardziej zautomatyzowanym środowisku, gdzie integracja procesów przemysłowych staje się kluczowym czynnikiem sukcesu. Aby sprostać wyzwaniom, niezbędne jest wdrożenie inteligentnych systemów, które nie tylko optymalizują produkcję, ale również zapewniają płynny przepływ informacji między poszczególnymi rozwiązaniami i działami. Na te potrzeby odpowiada Dział Digital Industrial Transformation w AIUT.
Integracja rozwiązań cyfrowych przełomowa dla produkcji
Z budową cyfrowej fabryki przedsiębiorcy nie powinni zwlekać. Eskalacja danych produkcyjnych, wynikająca z postępującej automatyzacji i robotyzacji procesów, umożliwi dokładniejszą analizę operacji, szybsze podejmowanie decyzji oraz bardziej efektywne zarządzanie zasobami. Warunkiem jest właściwa integracja środowisk cyfrowych.
– Sektor przemysłowy doświadcza eksplozji danych. To efekt wzmożonej robotyzacji i automatyzacji, dynamicznego rozwoju technologii komunikacji bezprzewodowej i coraz szerszego wykorzystania w przemyśle rozwiązań Internetu Rzeczy, czyli opomiarowania i sensoryki. Kluczem do uwolnienia ich potencjału jest budowa ekosystemu IT do zarządzania fabryką, który umożliwi międzysystemową integrację danych, ich analizę i dwukierunkową komunikację, zapewniając sterowanie rzeczywistymi procesami – mówi Andrzej Gaik, dyrektor Działu Digital Industrial Transformation w AIUT.
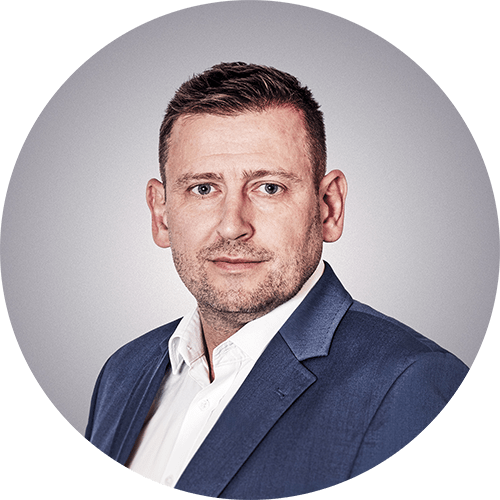
Datafikacja produkcji warunkiem dalszego wzrostu
Datafikacja, czyli przekształcenie fizycznych działań i procesów w dane cyfrowe, rewolucjonizuje zarządzanie produkcją. Dane zbierane z maszyn, sensorów i systemów zarządzania (ERP, MES, MOM) stają się kluczowym zasobem, umożliwiając:
- Szybsze podejmowanie decyzji na podstawie aktualnych informacji,
- Predykcję zdarzeń, zapobieganie awariom i redukcję przestojów,
- Lepsze planowanie i optymalizację produkcji dzięki analizie w czasie rzeczywistym.
Dzięki skutecznej integracji różnych systemów i aplikacji, przedsiębiorstwa mogą tworzyć spójne ekosystemy zarządzania fabryką, co prowadzi do efektywniejszego wykorzystania zasobów i skrócenia czasu realizacji zleceń.
Czym jest integracja procesów przemysłowych i komu powierzyć ten proces?
Integracja procesów przemysłowych polega na połączeniu różnych systemów, urządzeń i technologii w jeden spójny ekosystem zarządzania produkcją. Obejmuje to zarówno automatyzację procesów, jak i synchronizację danych pomiędzy systemami IT (np. ERP, MES, SCADA) oraz technologiami operacyjnymi (OT), takimi jak maszyny, linie produkcyjne, roboty i systemy intralogistyczne. Realizację tego typu inwestycji najlepiej powierzyć doświadczonemu integratorowi systemów automatyki przemysłowej, który tak jak AIUT, specjalizuje się w transformacji cyfrowej.
Kim jest integrator systemów automatyki? Jakie korzyści wynikają ze współpracy z integratorem procesów produkcyjnych? Już teraz przeczytaj na naszym blogu. AIUT ma blisko 35 lat doświadczenia w automatyzacji przemysłu i chętnie odpowiemy na Twoje pytania. KLIKNIJ, aby przejść do artykułu.
Połączony ekosystem IT – pełna kontrola
Tradycyjne systemy, takie jak ERP, MES czy SCADA, odgrywają kluczową rolę w zarządzaniu produkcją. Jednak w obliczu zmieniających się realiów – od masowej produkcji po seryjną produkcję unikatów – rośnie znaczenie ich integracji z warstwą OT (Operational Technology), obejmującą systemy i urządzenia, które wchodzą w interakcję ze środowiskiem fizycznym.
Dowiedz się, jak transformacja cyfrowa może pomóc Twojej firmie zwiększyć wydajność i minimalizować straty i przestoje.
Poniżej publikujemy fragment rozmowy z Andrzejem Gaikiem, ekspertem AIUT ds. transformacji cyfrowej, na łamach wydania specjalnego Control Engineering Polska.
Czy stosowanie systemów klasy MES (ang. Manufacturing Execution System) lub ERP (ang. Enterprise Resource Planning) do sterowania procesem produkcji przestanie być wystarczającym źródłem przewagi rynkowej?
– Systemy klasy ERP, czyli systemy planowania zasobów przedsiębiorstwa, stanowią jedno z kluczowych rozwiązań wspierających zarządzanie procesem produkcji i ważne źródło budowania przewag konkurencyjnych. Należy jednak zwrócić uwagę, że ostatnie lata znacząco zmieniły środowisko produkcyjne. Model masowej produkcji seryjnej zastępowany jest seryjną produkcją unikatów. To silnie wpływa na dynamikę działania przedsiębiorstw, powodując jednocześnie wzrost wymogów dotyczących oprogramowania. Dlatego tym bardziej należy zwrócić uwagę na integrację systemową. Aby możliwe było pełne wykorzystanie potencjału systemu ERP, musimy zapewnić łączność z użytkowanym parkiem maszynowym. Brak integracji może prowadzić do niepełnych lub błędnych informacji. Kompletne i wiarygodne dane stanu technicznego maszyn na temat ich dostępności czy awaryjności, to klucz do planowania i optymalizacji produkcji. Najlepiej, jeśli te informacje bazują na danych zbieranych bezpośrednio z urządzeń. Dynamicznie rozwijające się technologie komunikacji bezprzewodowej (WiFi gen 6, 5G) oraz szeroki dostęp do opomiarowania i sensoryki w przemyśle (IIoT), pozwalają na czerpanie takiej wiedzy z danych procesowych w czasie rzeczywistym.
[…]
W kierunku Industry X.0
– Kiedy będziemy najefektywniej zarządzać procesem produkcji? Wtedy, kiedy zbudujemy jeden, spójny komunikacyjnie, zintegrowany ekosystem zarządzania całą fabryką, opierający się na sensorach i czujnikach monitorujących urządzenia, maszyny, procesy produkcyjne, logistyczne, magazynowe oraz przekazujący dane w czasie rzeczywistym między różnymi poziomami systemów zarządczych, od MES, przez MOM (ang. Manufacturing Operations Management) i EAM/APM, na systemach ERP skończywszy. Prowadzi to do wyższego poziomu automatyzacji i autonomii w procesie produkcyjnym. W takie rozwiązanie AIUT potrafi i chce dziś wyposażać fabryki […].
– Z naszej perspektywy, integratora systemów przemysłowych, najważniejsze dopiero przed nami. Obecnie skupiamy się na integracji danych i informacji oraz uelastycznianiu i optymalizacji procesów produkcyjnych, aby umożliwić „seryjną produkcję unikatów”. Wśród liderów, szczególnie w wiodącej w Industry 4.0 branży motoryzacyjnej, obserwujemy jednak pewne nasycenie, w ramach którego dalsza optymalizacja w tym modelu staje się nieopłacalna. Odpowiedzią na stale rosnącą potrzebę skracania czasu wprowadzania na rynek nowych produktów jest idea Industry X. Przemysł X.0 jest z jednej strony kontynuacją Przemysłu 4.0 pod kątem dalszej integracji i automatyzacji, jednak to koncept wprowadzający zupełnie nowe podejście do optymalizacji procesu wejścia na rynek nowych produktów. Zamiast skupiać się na dalszym skracaniu i optymalizacji liniowego procesu – od projektowania, przez prototypowanie po wprowadzanie produktu do produkcji – umożliwia prowadzenie wielu takich procesów równolegle, wymiernie skracając Time-to-market – wyjaśnia Andrzej Gaik, dyrektor Działu Digital Industrial Transformation w AIUT.
Cały artykuł przeczytasz na łamach dodatku Control Engineering Polska „Integratorzy systemów automatyki 2024/2025”, s. 8-9. Publikacja jest dostępna online TUTAJ.
