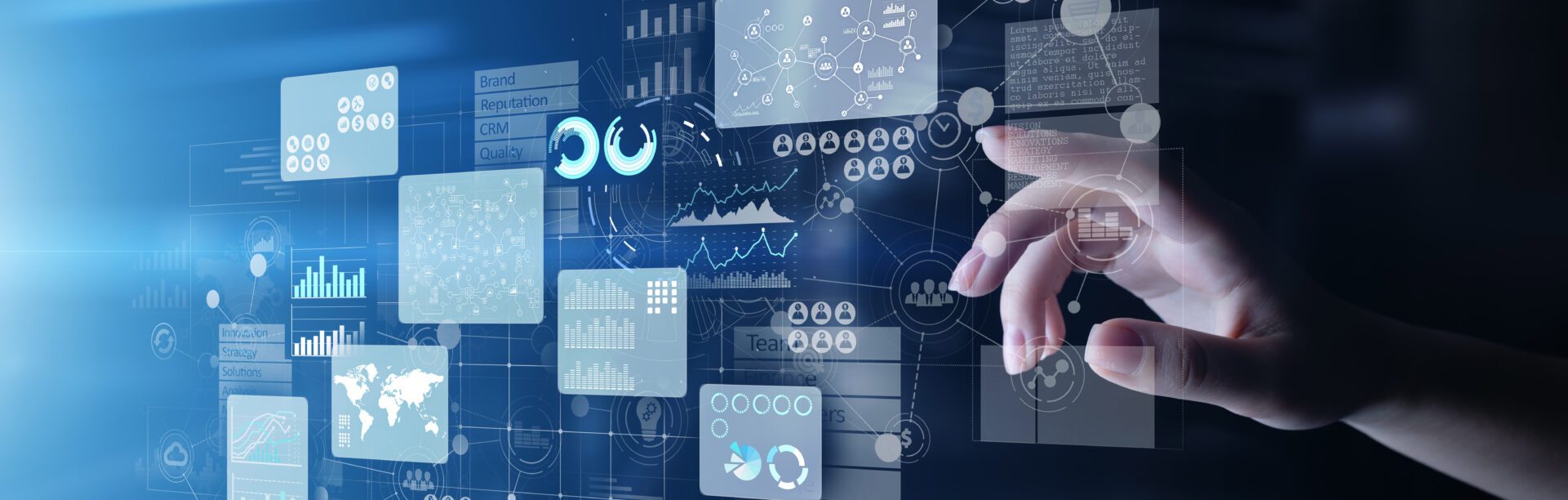
Cyfrowy bliźniak: Optymalizacja i datafikacja produkcji
Z tego artykułu dowiesz się:
-
jak wygląda rynek cyfrowych bliźniaków?
-
czym jest cyfrowy bliźniak oraz jak powstaje?
-
na czym polega proces datafikacji?
-
jakie są różnice między cyfrowym bliźniakiem a cyfrowym modelem?
-
jakie korzyści przynosi wdrożenie cyfrowego bliźniaka w firmie produkcyjnej?
-
dlaczego wysokiej jakości dane są niezbędne do budowy cyfrowego bliźniaka?
Każda firma produkcyjna powinna dążyć do cyfryzacji procesów, aby móc skutecznie realizować przyjętą strategię i zyskać przewagę konkurencyjną. W tym celu niezbędne jest gromadzenie wysokiej jakości danych o produktach, procesach czy systemach. To właśnie dzięki nim możliwe jest tworzenie cyfrowych modeli i przeprowadzanie symulacji w wirtualnym środowisku. Jedną z technologii, która umożliwia takie działania, jest cyfrowy bliźniak.
Technologia cyfrowego bliźniaka zyskuje szerokie zastosowanie w takich obszarach, jak optymalizacja produkcji, poprawa kontroli jakości, analiza predykcyjna, zarządzanie łańcuchem dostaw, intralogistyka, opieka zdrowotna, zarządzanie inteligentnymi miastami i budynkami, a także wytwarzanie i rozwój nowych produktów. Wykorzystanie cyfrowych bliźniaków pozwala przedsiębiorstwom podejmować lepsze decyzje oparte na danych, jednocześnie eliminując błędne lub nieskuteczne scenariusze.
W tym artykule omówimy, czym jest technologia cyfrowego bliźniaka, jak obecnie wygląda rynek cyfrowych bliźniaków, jakie korzyści przynosi wdrożenie tego rozwiązania, dlaczego istotne jest gromadzenie wysokiej jakości danych oraz jak odpowiednio podejść do budowy cyfrowego bliźniaka w firmie produkcyjnej.
Globalny rynek cyfrowych bliźniaków
Według raportu MarketsandMarkets globalny rynek cyfrowych bliźniaków wyniósł 10,1 miliarda dolarów w 2023 roku. Szacuje się, że będzie on rósł w latach 2023-2028 z CAGR wynoszącym 61,3%, osiągając wartość 110,1 miliarda dolarów w 2028 roku. Raport wskazuje, że dynamiczny rozwój rynku cyfrowych bliźniaków jest napędzany rosnącym zapotrzebowaniem na redukcję kosztów oraz usprawnienie procesów operacyjnych w łańcuchach dostaw. Ważnym aspektem jego postępu będzie także coraz częstsze wykorzystanie cyfrowych bliźniaków w sektorze opieki zdrowotnej, a także szerokie zastosowanie tej technologii w konserwacji predykcyjnej maszyn i urządzeń.
Czym jest cyfrowy bliźniak?
Cyfrowy bliźniak to znacznie więcej niż wirtualna replika fizycznych obiektów, procesów czy systemów. W przeciwieństwie do cyfrowych modeli uwzględnia on otoczenie poszczególnych elementów. Innymi słowami cyfrowy bliźniak jest to zintegrowane i interaktywne środowisko, które pozwala użytkownikom testować i analizować różne scenariusze w bezpiecznej, wirtualnej przestrzeni. Koncepcja odwzorowania rzeczywistości w cyfrowym świecie odgrywa kluczową rolę w przeprowadzaniu symulacji procesów produkcyjnych. Z pomocą cyfrowego bliźniaka firmy mogą udoskonalać istniejące rozwiązania lub weryfikować nowe pomysły jeszcze przed ich wdrożeniem w fabryce. Takie podejście umożliwia monitorowanie, analizowanie i optymalizacje procesów w wirtualnej przestrzeni, bez ingerowania w funkcjonowanie zakładu. Stąd, cyfrowa weryfikacja założeń redukuje koszty i czas wdrożenia nieefektywnych rozwiązań w świecie rzeczywistym. Obecnie, cyfrowy bliźniak jest nieodłącznym elementem dostaw nowych produktów i usług dla klienta oraz stanowi podstawę dalszych działań utrzymaniowych.
W skrócie, cyfrowy bliźniak stosowany do nowych rozwiązań wdrażanych w fabryce służy do:
- planowania,
- projektowania,
- analizowania,
- testowania,
- oraz przeprowadzania działań utrzymaniowych.
Natomiast w istniejących już rozwiązaniach, cyfrowy bliźniak umożliwia:
- monitorowanie i ciągłe doskonalenie procesów produkcyjnych.
Jak powstaje cyfrowy bliźniak?
Założenia projektowe
Przed przystąpieniem do budowania cyfrowego bliźniaka, kluczowym krokiem jest zdefiniowanie, jakie problemy będzie on rozwiązywać oraz na tej podstawie określenie, której części produkcji będzie dotyczył. Istotną kwestią jest także wyznaczenie celów, które chcemy z jego pomocą osiągnąć. Następnie rozpoczyna się proces datafikacji, czyli odwzorowania rzeczywistości w świecie cyfrowym za pomocą danych.
Model cyfrowy
W tym kroku zbierana jest specyfikacja techniczna oraz szczegółowa dokumentacja dotycząca urządzeń, linii produkcyjnych czy całych zakładów. Model cyfrowy obejmuje m. in. harmonogramy, struktury produktów, zwane BOM (ang. Bill of Materials), jak i dane historyczne o przestojach czy inspekcjach maszyn. W tym celu często wykorzystuje się systemy EAM/CMMS do kompleksowego zarządzania zasobami przedsiębiorstwa, tj. np. IBM Maximo. Integracja systemu zarządzania zasobami z Cyfrowym Bliźniakiem, pozwala firmie zyskać pełną kontrolę nad operacjami oraz przyspieszyć proces pozyskiwania danych.
Gromadzenie danych
Po zaprojektowaniu modelii w technologii 3D, wprowadzane są rzeczywiste dane, które staną się kluczowym zasobem podczas analizy i symulacji procesów. Mogą to być np. dane z maszyn, urządzeń, sensorów IoT, systemów sterowania i monitorowania procesów np. SCADA, zarządzania produkcją i magazynem (WMS, MES) czy systemów RTLS.
Analiza danych
Dane pozyskane z procesów same w sobie jeszcze nic nie znaczą. Kluczowym zadaniem jest wyselekcjonowanie najistotniejszych z nich i przekształcenie ich w wartościowe informacje. Dzięki przeprowadzeniu odpowiedniej analizy możliwe jest nie tylko przewidywanie awarii, ale także optymalizacja procesów produkcyjnych i zwiększenie wydajności operacyjnej. Algorytmy uczenia maszynowego odgrywają tu kluczową rolę, monitorując dane w czasie rzeczywistym oraz wspierając predykcję i automatyzację.
Aktualizacja cyfrowego bliźniaka
Aby uwolnić pełny potencjał technologii cyfrowego bliźniaka i uzyskać maksymalne korzyści z przeprowadzonych symulacji, ważną kwestią jest zapewnienie ciągłej, dwukierunkowej wymiany danych między cyfrowym obiektem a jego fizycznym odpowiednikiem w czasie rzeczywistym. Dzięki bieżącej wymianie informacji cyfrowy bliźniak wspiera firmy produkcyjne w podejmowaniu lepszych decyzji biznesowych, pozwala w bardziej efektywny sposób zarządzać procesami, jak i umożliwia monitorowanie stanu maszyn, w tym wczesne wykrywanie awarii.
Korzyści z wdrożenia cyfrowego bliźniaka
- Dostęp do symulacji: Posiadając cyfrowego bliźniaka, firmy mogą przeprowadzać symulacje online i testować różne scenariusze bez ingerencji w rzeczywiste procesy. Dzięki temu można zweryfikować zgodność pracy maszyn z wytycznymi projektowymi, co obniża ryzyko przestojów oraz skraca czas potrzebny na rzeczywiste uruchomienie inwestycji w zakładzie.
- Zwiększenie wydajności: Analiza danych w czasie rzeczywistym pozwala na bieżącą optymalizację procesów i ich ciągłe doskonalenie. Cyfrowe bliźniaki usprawniają procesy produkcyjne poprzez monitorowanie i dostosowywanie parametrów w czasie rzeczywistym.
- Lepsza jakość produktów: Dzięki symulacjom i testom firmy mogą wprowadzać zmiany w procesach produkcyjnych przed ich rzeczywistym wdrożeniem, co przekłada się na lepszą jakość produktu końcowego.
- Redukcja przestojów i konserwacja predykcyjna: Cyfrowe bliźniaki umożliwiają przewidywanie awarii i planowanie konserwacji, co wpływa na zachowanie ciągłości produkcji.
- Optymalizacja kosztów: Dzięki dokładniejszej analizie procesów możliwe jest lepsze zarządzanie zasobami, co prowadzi do eliminacji nieefektywnych działań.
Dlaczego wysokiej jakości dane są kluczowe w budowie cyfrowego bliźniaka?
W procesie tworzenia cyfrowego bliźniaka dane o wysokiej jakości odgrywają kluczową rolę, ponieważ to właśnie na ich podstawie powstaje precyzyjny model rzeczywistego obiektu lub procesu. Dzięki nim możliwe jest budowanie cyfrowych modeli, które wiernie odwzorowują zachowanie maszyn, linii produkcyjnych oraz systemów. Nieaktualne dane mogą prowadzić do błędnych symulacji, które negatywnie wpływają na działanie przedsiębiorstwa, zwiększając ryzyko kosztownych przestojów i nieefektywnych działań naprawczych. Stąd, dane o wysokiej jakości stanowią fundament efektywnego i niezawodnego działania cyfrowego bliźniaka, a także są najważniejszym czynnikiem sukcesu wdrażanych strategii w świecie rzeczywistym.
Podsumowanie
Wprowadzenie cyfrowego bliźniaka do przemysłu otwiera nowe możliwości w zakresie optymalizacji procesów produkcyjnych. Cyfrowy bliźniak, zaawansowane technologie IoT i analityka danych stają się fundamentem nowoczesnych fabryk. Te technologie umożliwiają przewidywanie awarii, poprawę jakości oraz szybsze podejmowanie decyzji. Przemysł 4.0 oraz rozwój cyfrowych bliźniaków to nieodłączny element przyszłości produkcji, zapewniający firmom konkurencyjność i efektywność operacyjną.
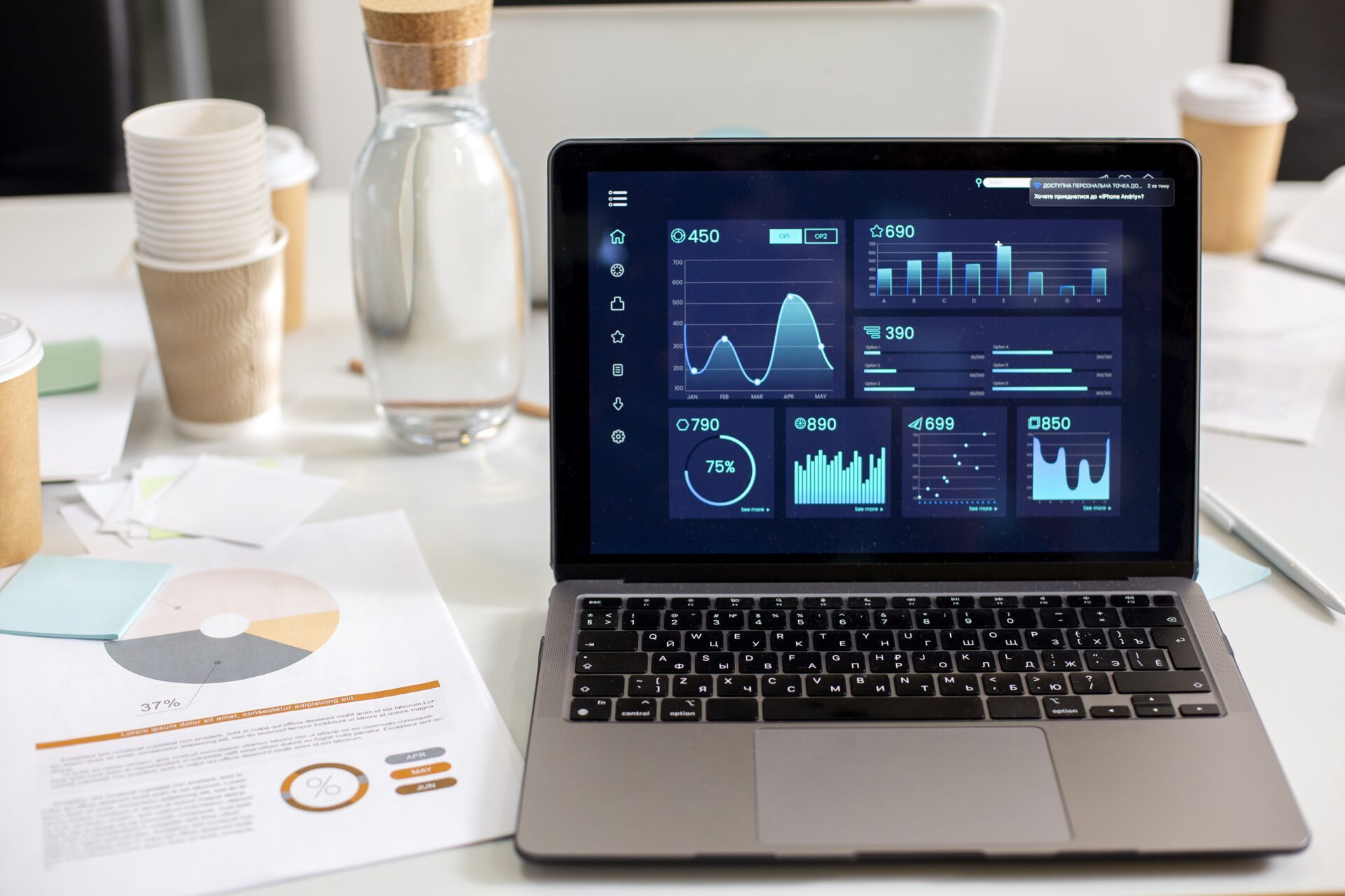
Czy Twoja firma wdrożyła już cyfrowego bliźniaka?
Jeśli nie, skontaktuj się z nami, aby dowiedzieć się, jak AIUT może wesprzeć Twoje przedsiębiorstwo w procesie digitalizacji produkcji i we wdrożeniu technologii cyfrowego bliźniaka.