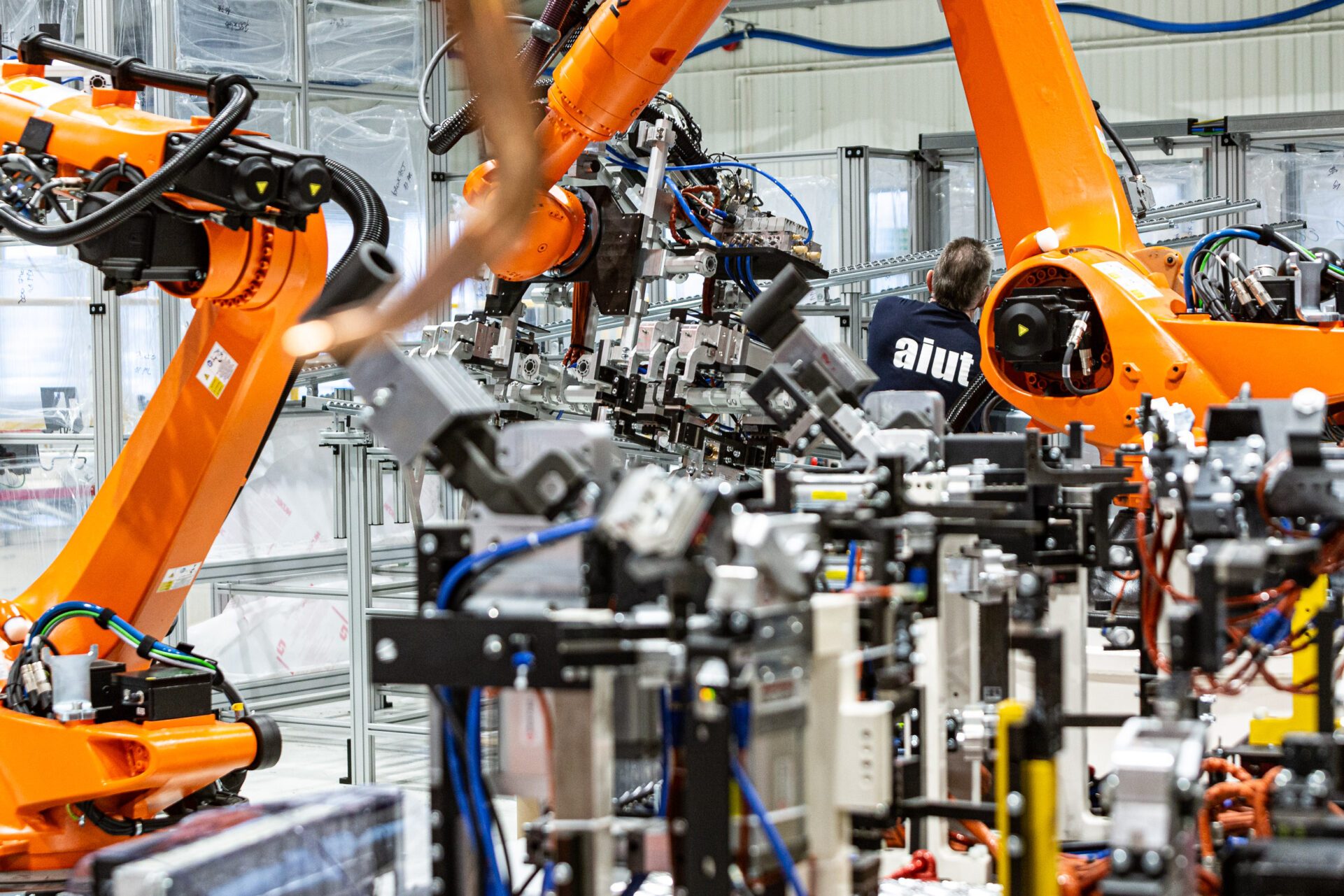
Who is an industrial automation integrator?
In this article, you will learn:
-
who is an industrial automation integrator, and what is their role?
-
what tasks does a systems integrator perform?
-
why do you need a systems integrator for automation and robotics solutions?
-
what are the benefits of working with an experienced industrial automation integrator?
-
how to choose the right industrial automation systems integrator?
-
learn about the largest Polish systems integrator company.
Definition of an industrial automation integrator and their role in Manufacturing 4.0
An industrial process integrator designs and implements advanced turnkey control systems for manufacturing plants, warehouses, and other facilities across various industries. These solutions help businesses enhance process efficiency, achieve higher production levels, and seamlessly progress through industrial revolutions, from Manufacturing 4.0 to Manufacturing X.0.
Integrators manage both the development of new installations and the modernization of existing systems, ensuring all components are seamlessly combined into a cohesive and functional solution. Their role encompasses supporting clients at every stage — from identifying the problem and implementing custom automation solutions to providing ongoing maintenance. This comprehensive process includes design, construction, testing, deployment, and servicing, all aimed at streamlining and automating the client’s processes.
Leading interdisciplinary teams, integrators deliver complex projects that go far beyond standard engineering tasks. Their teams typically include automation engineers, electricians, PLC (Programmable Logic Controllers) and SCADA (Supervisory Control and Data Acquisition) programmers, mechanics, as well as experts in IoT (Internet of Things), cybersecurity, machine vision, intralogistics, process analysis and optimization, IT, system integration (e.g., with MES or WMS systems), interface design, project management, and service.
With such a broad range of expertise, technical skills, and extensive experience, systems integrators execute complex industrial automation and robotics projects tailored precisely to the client’s needs and requirements. They also offer integration with existing IT systems in the factory and ensure ongoing support for implemented solutions. In essence, an automation integrator company serves as an indispensable technological partner in industrial transformation, driving the automation and robotics of factories and warehouses.
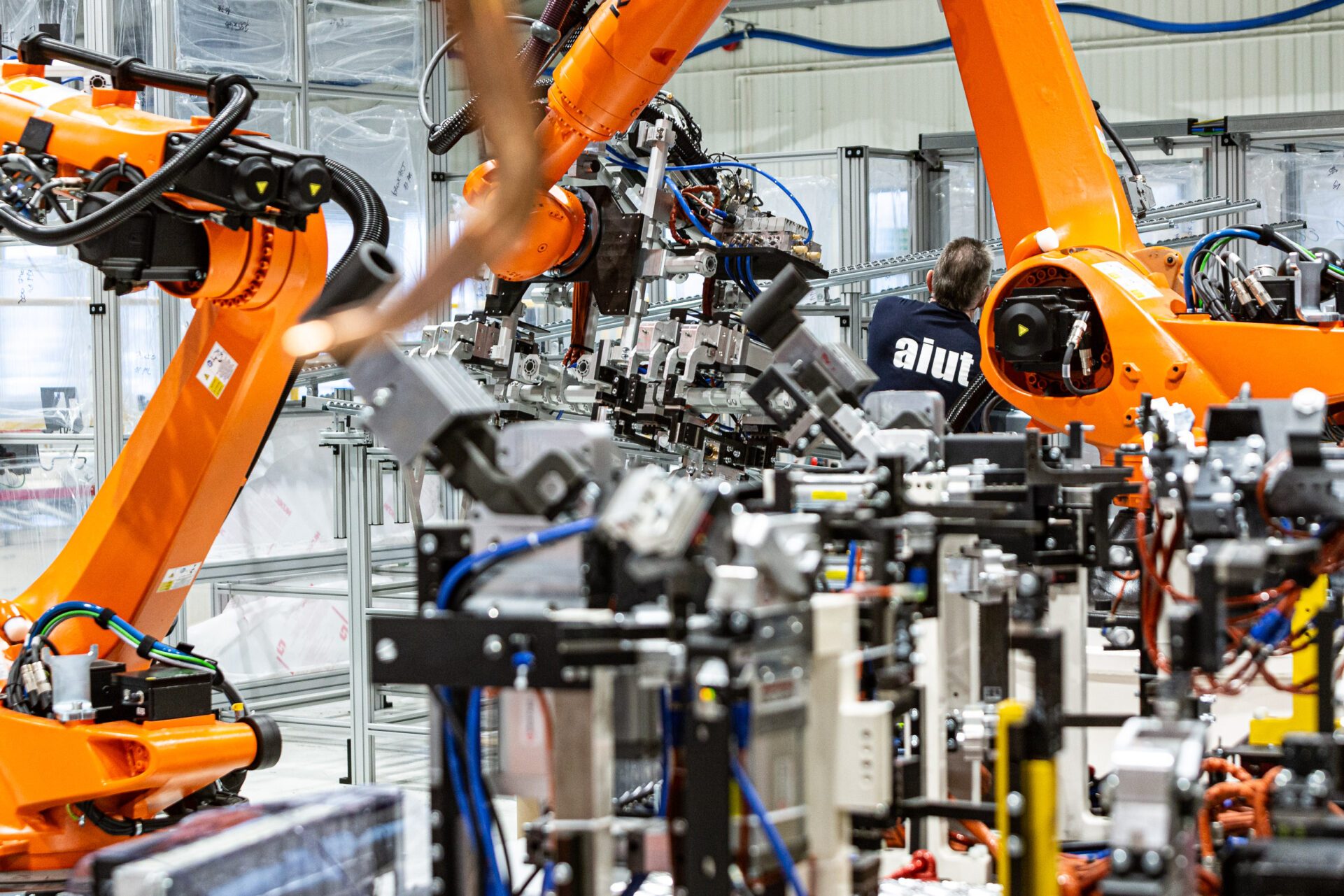
Tasks performed by industrial automation integrators
Each of the tasks listed below is a critical component of implementing and maintaining industrial automation systems. Whether designing a new solution or modernizing an existing system, an industrial automation integrator effectively manages and tailors activities to the specific requirements of the project.
Analyzing client needs and defining the project
In the initial phase, an industrial automation integrator conducts a thorough analysis to identify the client’s challenges, define their needs, and understand expectations. A key part of this process involves gathering as much information as possible about relevant factory processes, often through on-site visits and detailed questioning. Based on these insights, the integrator recommends suitable solutions and collaboratively sets goals and desired outcomes, guided by Key Performance Indicators (KPIs) to measure the success of the implementation.
Designing automation systems
This phase includes developing detailed technical documentation and creating designs tailored to the client’s specific needs. Industrial automation integrators prepare electrical, mechanical, and software schematics, ensuring they meet both technological and operational requirements. Key elements of this stage involve identifying potential project risks and planning the integration with existing factory systems. Each solution must comply with safety standards while being cost-effective and optimized for performance.
Selecting components and automation technologies
This task involves choosing the appropriate devices, controllers, sensors, and technologies that best align with the requirements outlined in the project. Industrial automation integrators prioritize reliability, compatibility, and scalability when selecting components. The key objective of this stage is to ensure reliable system operation and eliminate potential errors.
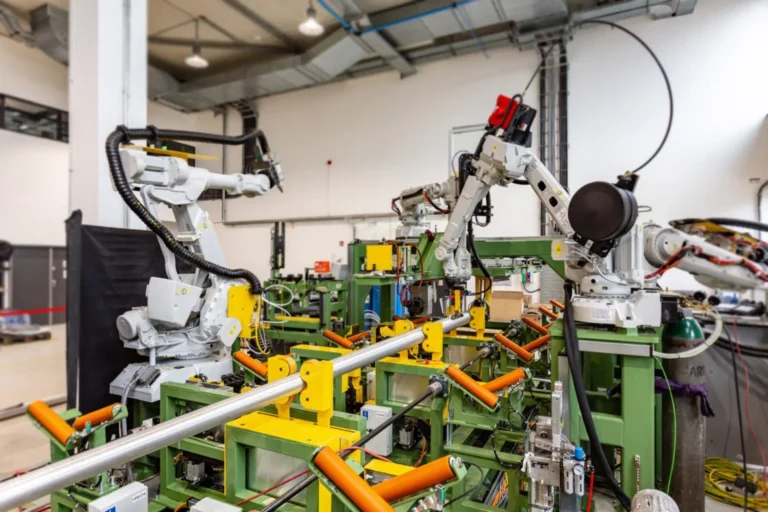
Programming and configuration of automation solutions
Specialists responsible for this stage develop control software tailored to the client’s specific requirements. Programming includes PLC systems, HMI/SCADA platforms, and process visualization tools. Simultaneously, device configuration is performed to ensure their optimal operation within the entire system.
Building automation systems and testing prototypes
Integrators leverage Digital Twin technology, Virtual Commissioning tools, and dedicated testing workshops to ensure the reliability of implemented solutions. Building and testing prototypes allow for early verification of the system's compliance with client requirements and the identification of potential issues. Through system simulations, project optimization can occur at an early stage, reducing implementation time at the client’s site.
Installation and commissioning of automation systems
After completing the design and testing phases, the system is installed in the industrial environment and commissioned. This process includes hardware assembly, device connections, and detailed testing under real operating conditions. The key objective of this stage is to ensure reliable system performance and eliminate any potential errors.
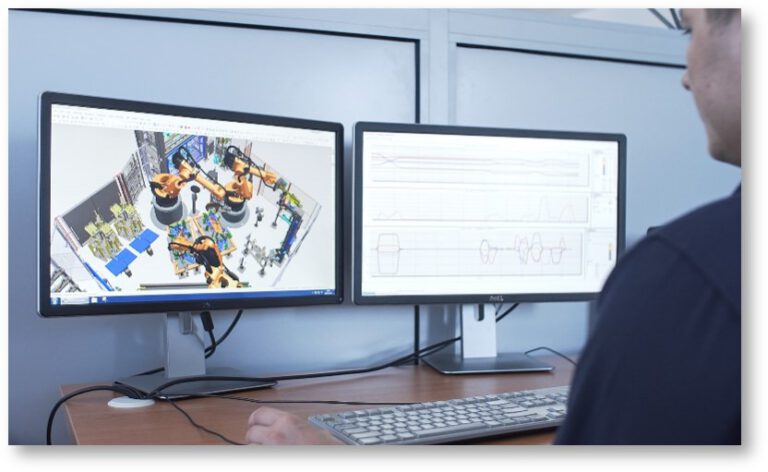
Integration of automation systems with IT infrastructure
At this stage, new technologies and devices are seamlessly combined into a cohesive system. The process involves adapting new components to the existing infrastructure and ensuring full compatibility with systems such as WMS, ERP, and MES. The key challenge lies in synchronizing all elements to work harmoniously, eliminating potential technological conflicts. The result of this integration is a digital ecosystem that enhances production management.
Training for operators on implemented automation solutions
Once the implementation is complete, integrators organize training sessions for end users. These sessions aim to ensure that operators can efficiently use the implemented system, respond to potential issues, and fully leverage its capabilities. The training programs are tailored to the participant's level of expertise and the specific features of the deployed solution.
Post-implementation service and support
An industrial automation integrator offers long-term technical and service support, including diagnostics, maintenance, software updates, and the adaptation and development of automation systems to meet new business needs. With local engineering centers in customer markets, integrators can respond quickly to emergencies and ensure regular maintenance. This approach ensures optimal system performance and minimizes the risk of production downtime.
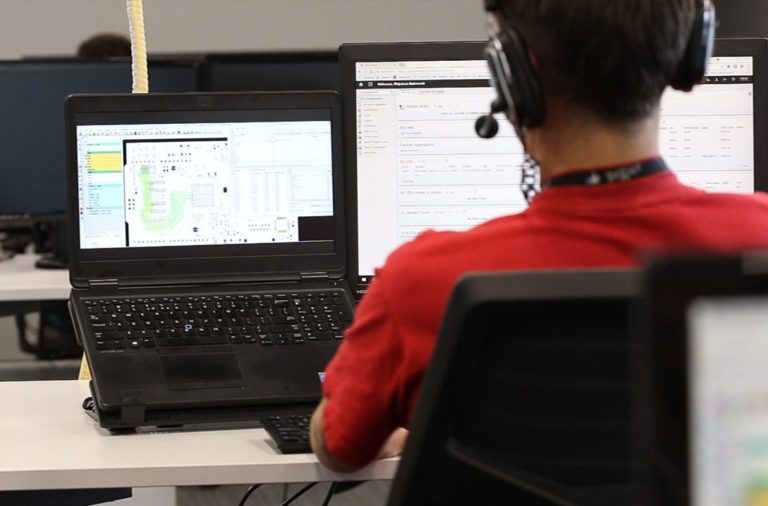
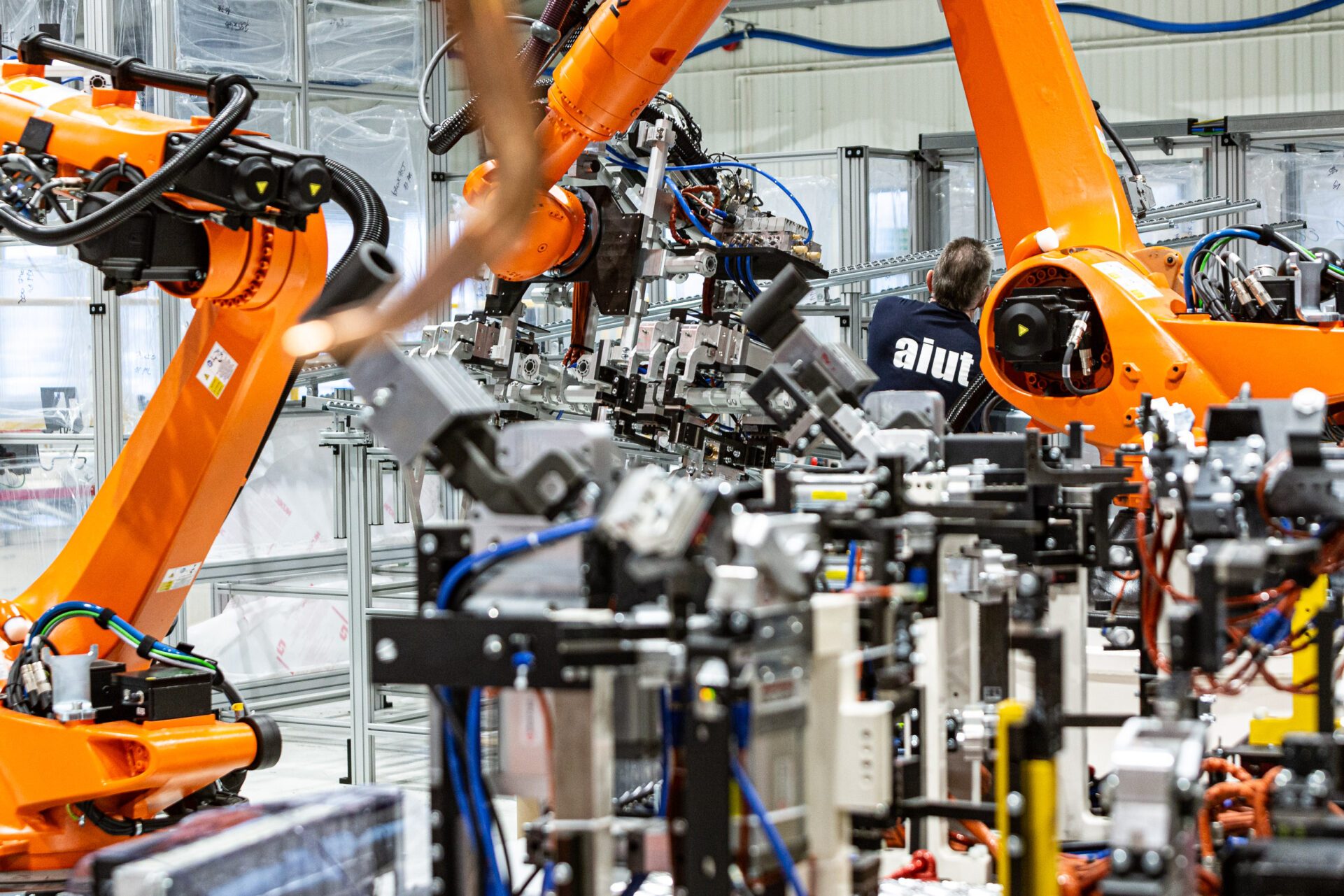
Automation: The cornerstone of Manufacturing 4.0 – Why every business needs an industrial automation integrator?
Manufacturing 4.0, also known as the Fourth Industrial Revolution, relies on advanced automation and robotics technologies as well as IoT (Internet of Things) solutions. Industrial automation integrators play a pivotal role in implementing this concept, shaping the factories of the future with high efficiency, flexibility, and minimal production downtime.
Businesses across various industries rely on the expertise of automation integrators, where automation and robotics are critical to building competitiveness and operational efficiency. This includes sectors such as automotive, pharmaceutical, food, and heavy industries.
Clients frequently engage integrators to implement production lines, robotic workstations, and logistics solutions involving AMR/AGV robots and transportation systems. Specialized integrators also focus on modernizing existing equipment and integrating automation, robotics, IT, and IIoT systems. They excel at delivering custom solutions, ensuring high quality and timely execution.
While automation and robotics are often associated with large enterprises, the growing availability of technology and support from EU funding make these solutions increasingly accessible to small and medium-sized businesses (SMEs). Automation integrators precisely tailor solutions to the specific needs of their clients, designing systems that optimally support their production processes.
Regardless of the scale of operations, implementing process automation increases efficiency, reduces operational costs, and strengthens a company’s market position. Collaboration with an automation integrator ensures a professional approach, customized solutions, and support at every stage of the project.

Benefits of collaborating with an industrial automation integrator
In an era of rapid technological advancements, integrating automation systems has become a crucial component of effective production management across various industries. This process enables businesses to optimize workflows, enhance efficiency, and reduce unnecessary costs. Automation integrators provide end-to-end support, from needs analysis to implementation and maintenance, leveraging cutting-edge automation technologies and tailoring solutions to meet specific client requirements. They help businesses achieve technological growth while maintaining a competitive edge.
By utilizing advanced engineering and design tools, automation integrators deliver safe, efficient, and cost-effective solutions aligned with Manufacturing 4.0 principles. Their expertise ensures seamless automation and robotization of workstations and production lines, as well as system integration within factories.
In summary, partnering with an industrial automation integrator offers numerous advantages, including:
- a personalized approach tailored to client needs.
- comprehensive support throughout the project lifecycle.
- access to cutting-edge automation technologies.
- reduced operational costs.
- increased efficiency and quality.
- integration with existing systems.
- expert knowledge and experience.
- compliance with the latest regulations and standards.
- high-quality execution and on-time delivery.
- professional service and technical support.
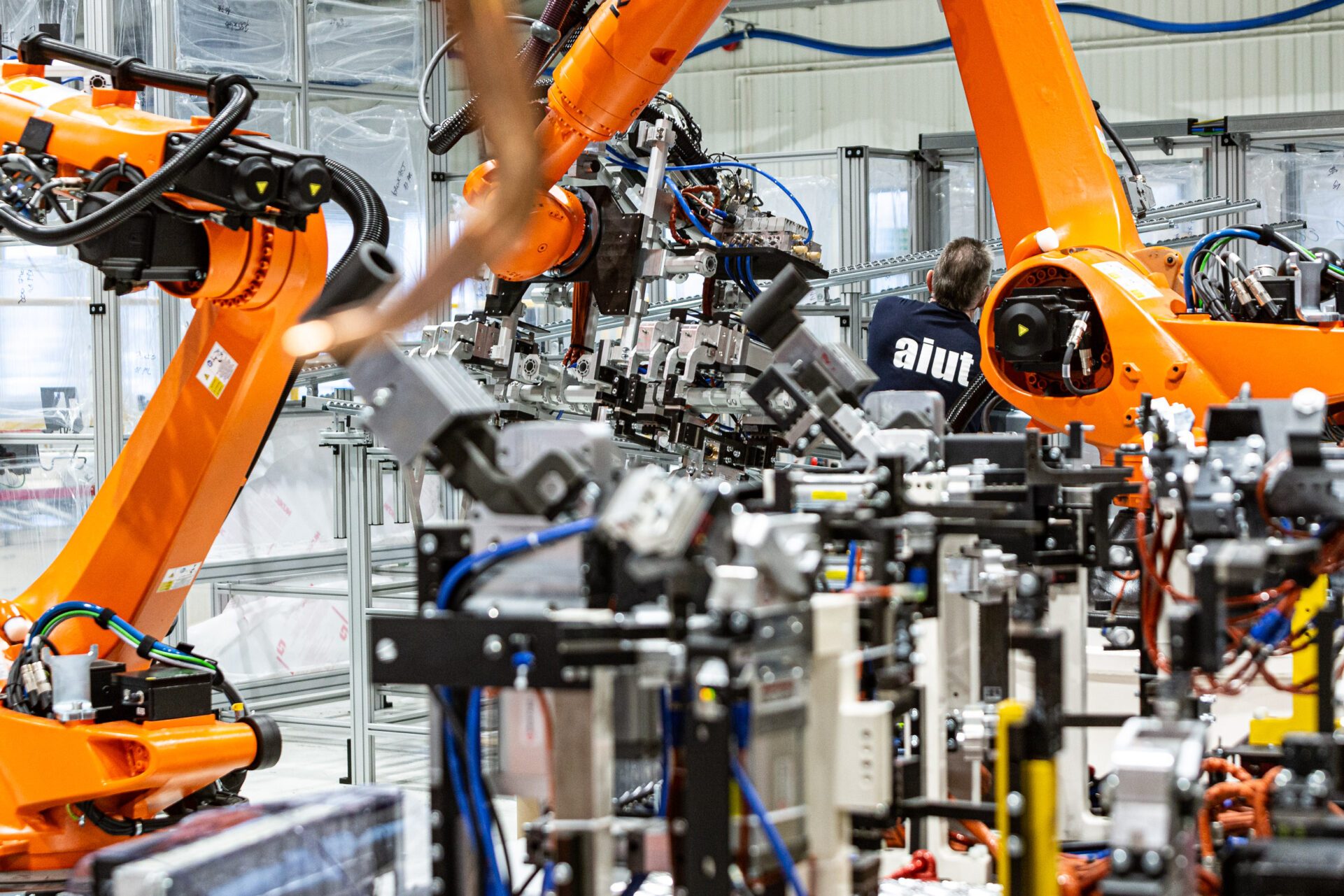
What to consider when choosing an industrial automation integrator
Selecting the right technology partner for implementing and integrating industrial systems is a critical factor in the success of an automation project. It is essential to choose an integrator with proven experience in working with the technologies and systems relevant to your project, as well as expertise in the specific industry in which your business operates. Reviewing the integrator’s portfolio of completed projects can help verify whether they have the necessary knowledge, skills, and experience to successfully deliver automation and digitalization solutions. Additionally, it allows you to assess the quality of their work, which directly impacts operational efficiency and timely product delivery to the market.
A distinguishing feature of a good integrator is the use of advanced technologies such as Digital Twin or Virtual Commissioning. These tools enable simulation and testing of designed solutions in a virtual environment. It's also important for the integrator to have in-house workshops and production facilities where prototypes of production lines, robotic workstations, automation systems, and intralogistics solutions can be built and tested. This approach minimizes the risk of errors during real-world implementation and significantly reduces the time required to commission systems at the client’s site.
When choosing an automation systems integrator, consider the size of their engineering team. A larger team offers diverse expertise, faster project delivery, greater flexibility, and the ability to ensure continuity even if a key expert is unavailable due to extended leave. It is also critical to evaluate whether the integrator has local engineering centers near your facility. Local presence ensures rapid response to unexpected failures, minimizing downtime risks and ensuring continuous production. It also facilitates regular servicing of implemented systems and devices.
Finally, ensure the integrator maintains strong relationships with technology manufacturers and suppliers. This can provide better access to state-of-the-art solutions and lead to more efficient project implementation.
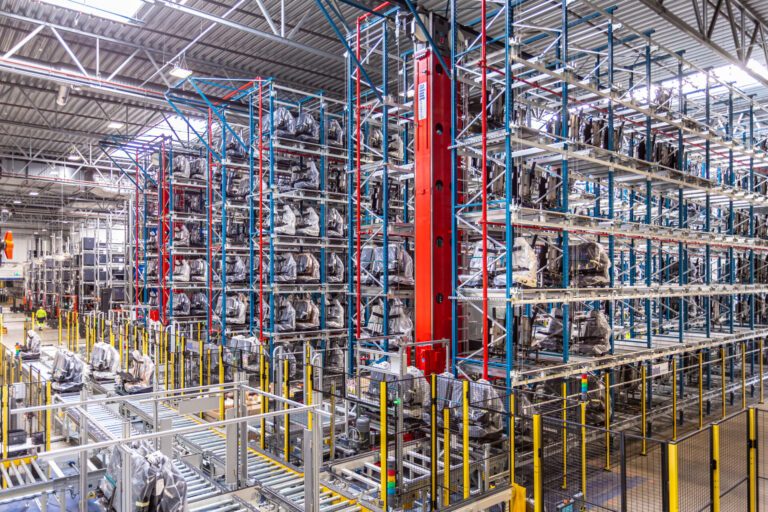
Where to find information about industrial automation integrators?
To find the right industrial automation integrator, it’s worth leveraging organizations that bring together companies in this field. In Poland, the search for a suitable technology partner is made easier by FAIRP – an organization representing the largest and most experienced industrial automation integrators. FAIRP unites systems integrators who deliver comprehensive solutions in factory automation, robotics, automated storage and retrieval systems (ASRS), and OT/IT system integration, tailored to meet diverse industrial needs.

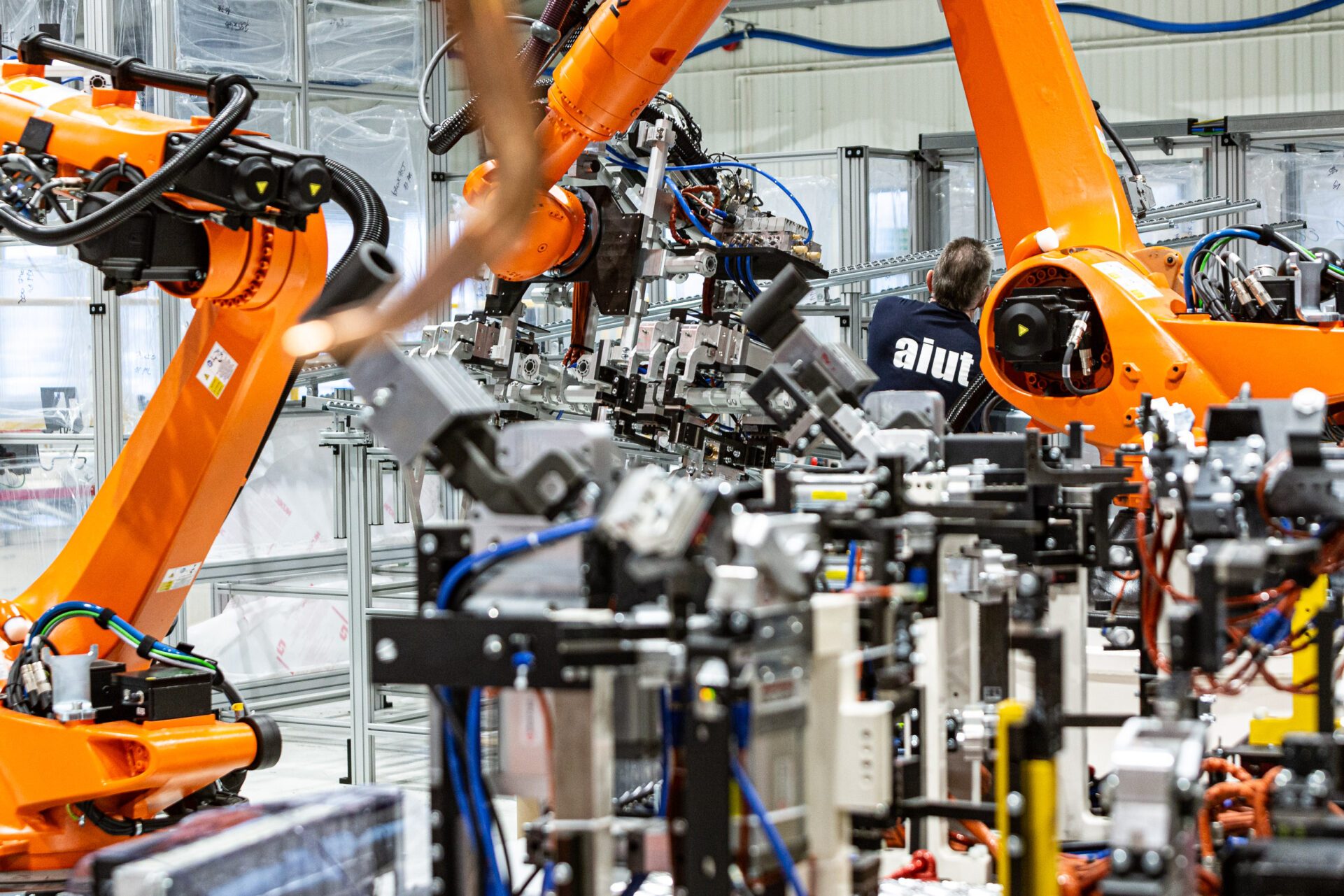
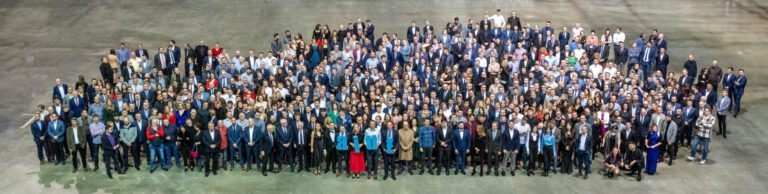
We are experts in designing and delivering turnkey solutions for automation and robotics in production processes. AIUT offers a wide range of solutions, including robotic production lines and workstations, comprehensive industrial automation systems, IT and IIoT solutions, warehouse management systems (WMS), and CMMS/EAM-class systems that support enterprise asset management and maintenance. Our services cover every stage of factory modernization — from process design and seamless integration of advanced control systems to full implementation. We also provide automated warehouse systems, internal transportation solutions, and smart metering systems for remote monitoring of utilities and fuels.
Experience shows that a competent automation systems integrator becomes a long-term technological partner for their clients. At AIUT, we deliver end-to-end support — from tailor-made design and project execution to technical assistance at every stage of implementation and operation. Our work not only optimizes current operations but also prepares companies for future challenges. With our approach, every element of the production and logistics process is integrated and streamlined, resulting in higher efficiency and improved system collaboration.
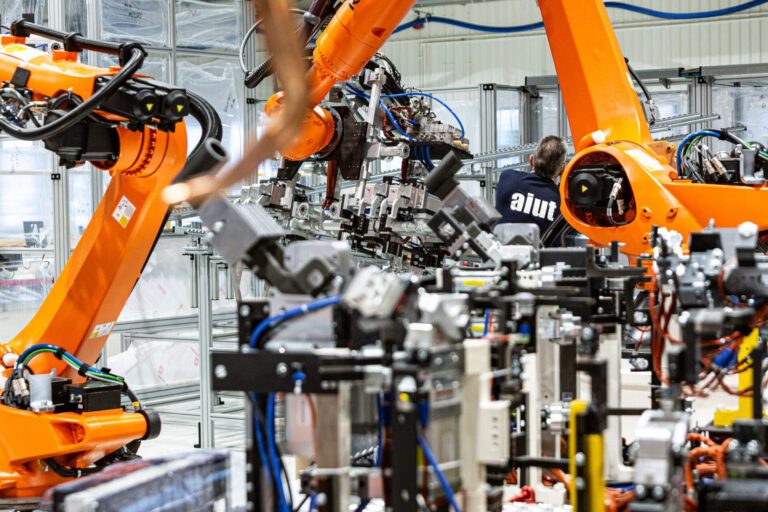
By establishing local engineering centers in customer markets, AIUT ensures fast and direct support, including immediate response to production facility failures. We understand the specific needs of our clients, possess extensive engineering expertise, and tailor our solutions to unique production processes, supporting their technological and business objectives.
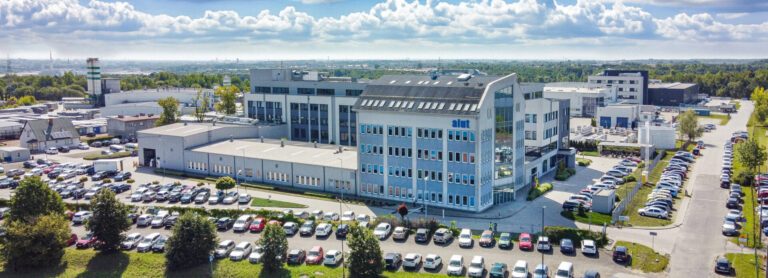
With our in-house production facilities and advanced systems, we can create simulations, digital twins, and conduct virtual commissioning of entire production lines. Watch the video to see how it works in practice. These activities minimize the risk of errors during actual implementation, significantly reduce commissioning time, and enhance the reliability of programmed industrial robots and systems. Learn more about us.
Summary
An industrial automation integrator is a key partner supporting businesses in designing, implementing, and servicing custom industrial solutions. Their primary role is to help companies enhance efficiency, reduce costs, and automate production processes. Collaboration with an experienced integrator provides access to advanced technologies and precisely tailored industrial automation solutions. When selecting an integrator, it is essential to consider their experience, project portfolio, and the availability of local engineering centers.
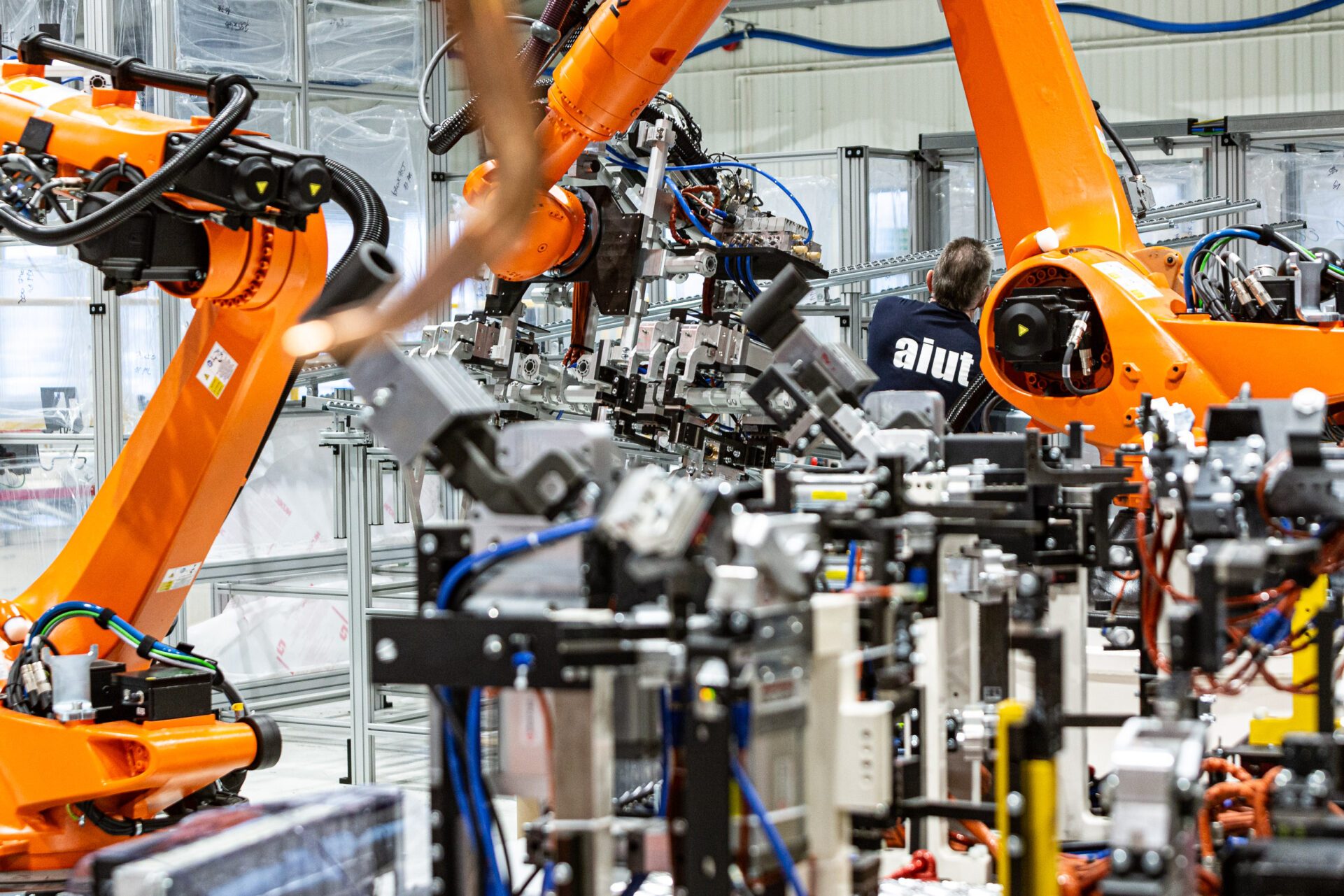