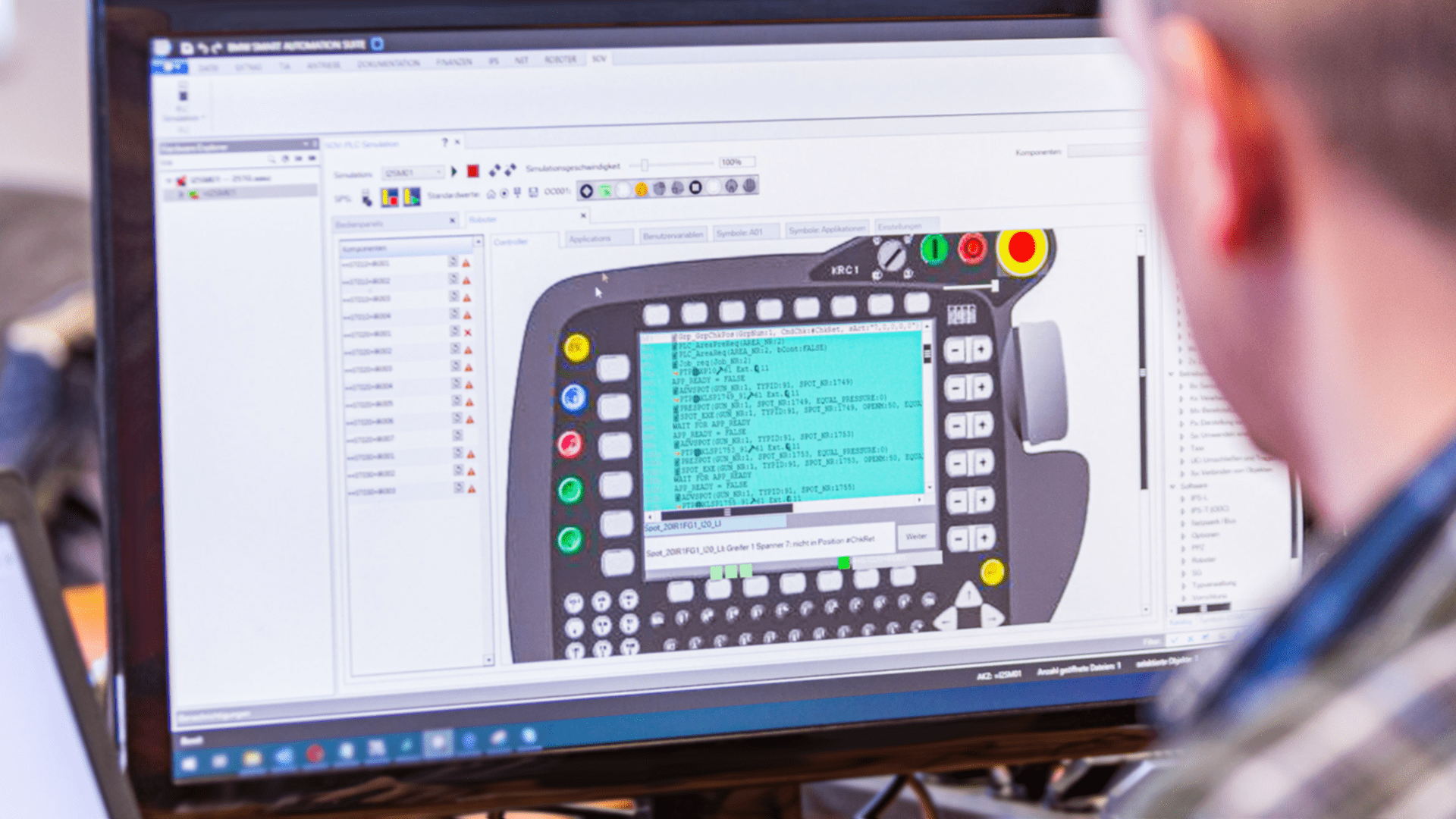
We use the technology of Virtual Commissioning to reduce the actual time needed for the implementation of robotized production lines and stations.
Factory 4.0: a flawless commissioning
Growing market expectations towards reducing the time to launch production processes require advanced solutions to be used.
At AIUT, we use virtual commissioning (VC) technology to fully optimize the designed (or existing) production lines and stations. The range of simulation includes both hardware and software. Our solution allows to test the operation of control systems, simulate the mechanics and automation of defined processes (including the work of robots), and many others. As a result, structural errors are detected and eliminated during the design phase, before they to occur in reality.
Virtual commissioning allows for quick and precise optimization. This is applicable especially (but not limited) to large production lines and robotized stations, even before their actual start-up.
Virtual system validation
- process simulation
- three-dimensional models of all elements included in the robotized production line
- optimal layout of all components
- selection of robots and system tools
- robot reach-range testing
- collision-free paths planning
- service points defining
- robot trajectory optimization
- adapting the application to the customer’s standards
Advantages of virtual commissioning:
- Accelerated time to production
- risk minimization
- elimination of errors at the level of advanced simulations - before the production starts
- technology of optimization
- minimizing the risk of downtime in case of a new model implementation or an introduction of changes to existing production processes.
- planning and implementing new models in parallel with existing productions
- higher return on investment
- improved competitiveness of the plant
Digital factory
Virtual commissioning is a modern tool that significantly speeds-up the commissioning of machines and production lines process. The digital simulation model enables to test any assembly line (either the ones in the design phase or the ones already in operation), including machines and individual stations even before their actual commissioning.

The main, yet separate tasks for virtual commissioning are:
Defining input/output signals, logical definitions, HMI programming, safety programming.
Required simulations and tests for creating the mechanical project of a production system, including the design, kinematics, programs (path-planning), intervals and cycle time.
Digital twin introduces new possibilities
VC technology enables the replication of robotic stations, production process, and even the entire production hall, using combined data from the entire production ecosystem. As a result, a so-called digital twin is created. Such advanced simulations allow you to map real product behaviour, improve machine and robot behaviour, enable monitoring of various process parameters, reveal production gaps and low-efficiency processes.