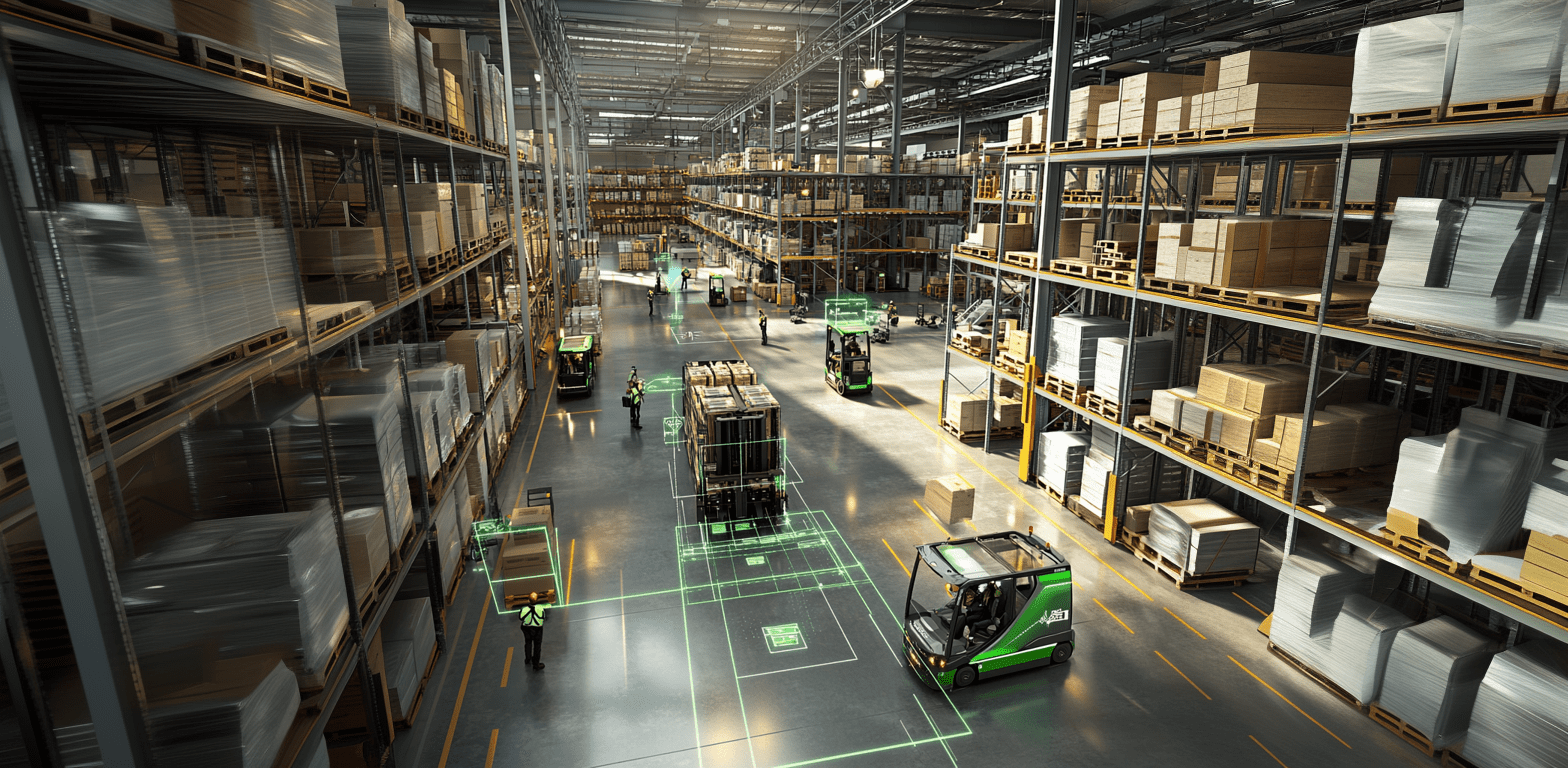
How does RTLS eliminate bottlenecks in manufacturing?
In this article, you will learn:
-
what are bottlenecks in manufacturing, and what are their consequences?
-
what are the types of bottlenecks?
-
how can process bottlenecks be eliminated?
-
what is a Real-Time Location/Locating System (RTLS) and how does it work?
-
how does a real-time location/locating system help identify bottlenecks in manufacturing?
-
what are the benefits of RTLS?
-
with which technologies can the RTLS system be integrated?
-
in which industrial sectors is the RTLS Romotus system applicable? — use cases for RTLS
Knowing what happens in our factory is crucial for implementing corrective actions and optimizing processes. Managing bottlenecks requires examining manufacturing processes and comparing them with our assumptions and expectations. One tool that facilitates this is a Real-Time Locating/Location System, such as the AIUT RTLS Romotus. With its help, we can monitor resources and collect reliable location data for identifying, analyzing, and eliminating bottlenecks. Additionally, the RTLS system supports the philosophy of KAIZEN, which emphasizes continuous process improvement, allowing us to prevent disruptions and production downtimes in the future. In this article, we will discuss what bottlenecks are, the consequences they bring, and how to eliminate them. We will also introduce the RTLS system, outline its benefits to businesses, and highlight key considerations when implementing corrective actions.
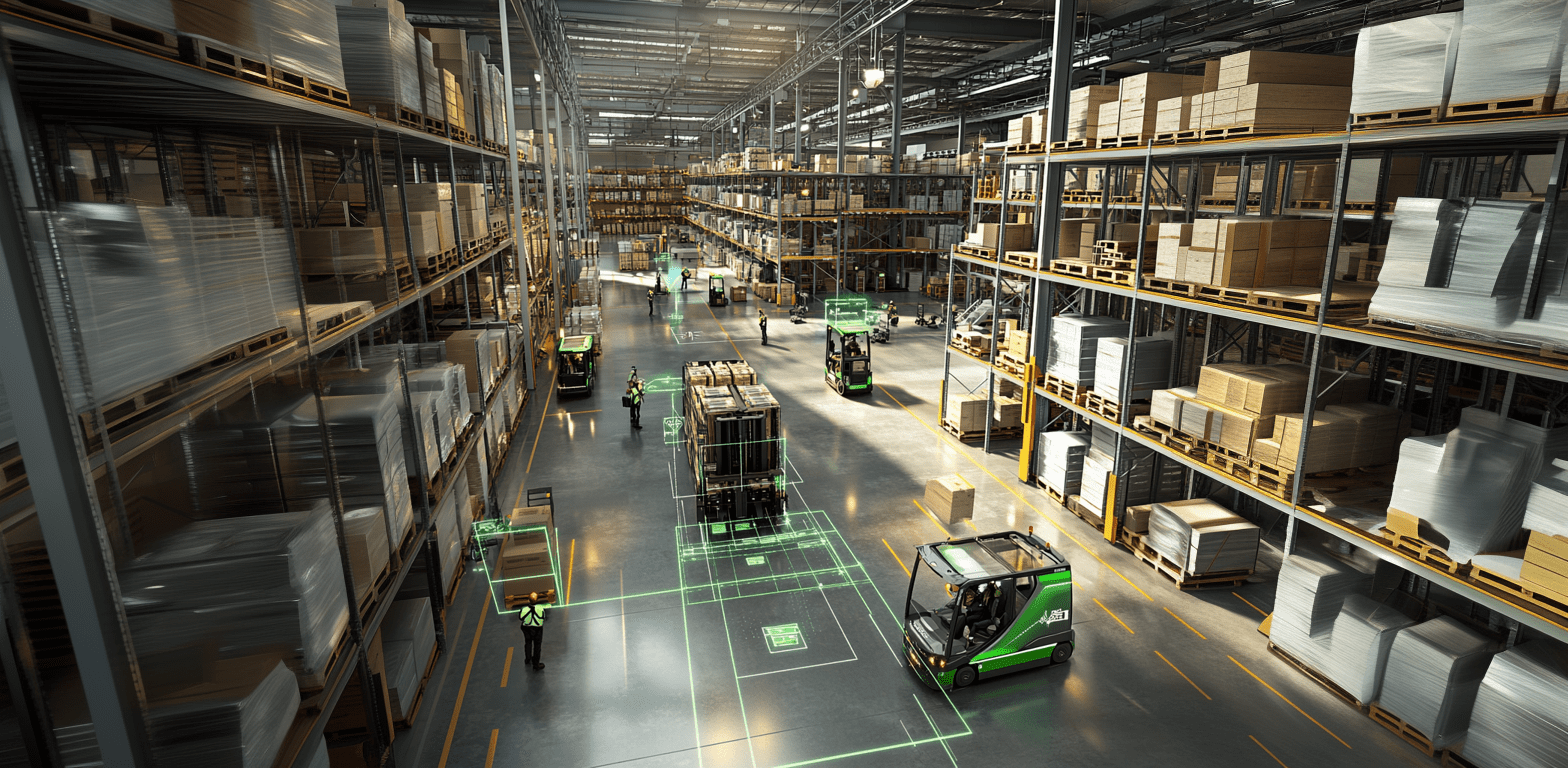
Bottlenecks – what are they, and what are their consequences?
A bottleneck refers to elements or resources that limit the efficiency of a process or an entire system. In other words, these are the weakest links, causing production downtimes, reduced system throughput, and lower employee motivation and efficiency. Additionally, bottlenecks can lead to overproduction, longer order fulfillment times, and increasing pressure from customers.
Bottlenecks can occur both in production and logistics. Depending on their duration, they can be classified as short-term or long-term. Short-term bottlenecks are less problematic for businesses since their consequences are temporary, such as when a skilled employee takes a few days off due to illness. However, long-term bottlenecks hidden within processes continuously decrease production efficiency. These require particular attention, as their negligence or misidentification can result in frequent downtimes, inefficient goods flow, deteriorating machinery conditions, and eventually, the gradual loss of customers. A long-term bottleneck may occur, for instance, when a machine breaks down due to excessive overloading, causing a production line stoppage and generating financial losses for the company over an extended period.
The term "bottleneck" is derived from "bottle" and "neck." The concept of a bottleneck can be visualized using a bottle, whose neck restricts flow and illustrates how a single inefficient element in a process can impact the entire company, reducing its efficiency and slowing down other activities.
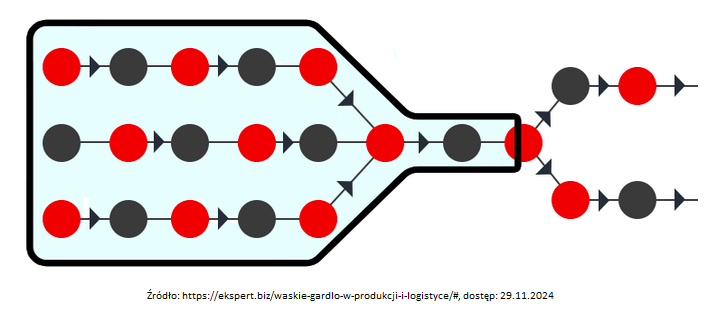
How to deal with bottlenecks? — identifying, analyzing, and reducing bottlenecks
Managing bottlenecks is a crucial step toward achieving greater efficiency in a manufacturing enterprise. Identifying bottlenecks involves analyzing actual processes to pinpoint areas where inefficiencies occur. Once the precise location of bottlenecks is identified, a corrective action plan should be developed to eliminate them. After implementing corrective solutions, ongoing process monitoring becomes essential to remain vigilant against deviations. This approach aligns with the well-known Deming Cycle, which emphasizes the principle of continuous improvement: Plan, Do, Check, Act.
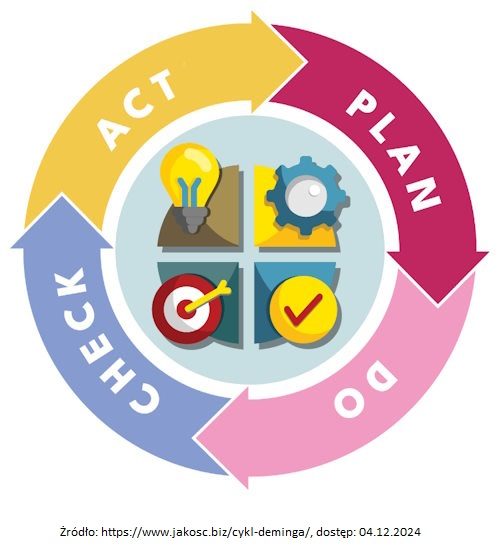
It sounds simple, but how can processes in a factory be analyzed and monitored?
One of the tools that enables process monitoring, as well as identifying and subsequently eliminating bottlenecks, is AIUT's real-time location system called RTLS Romotus.
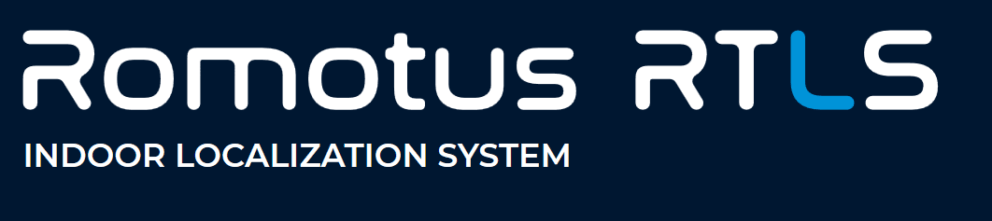
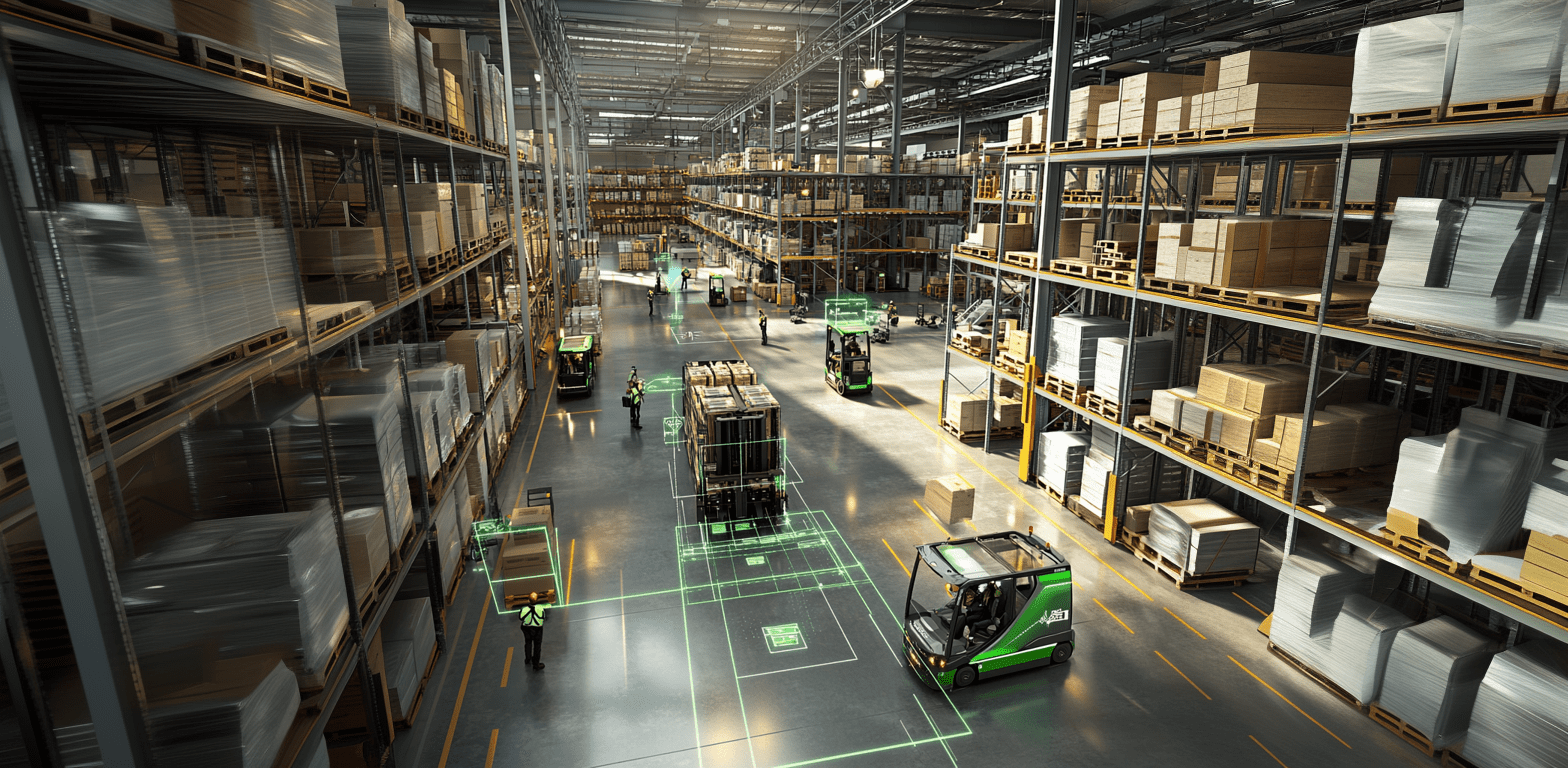
What is RTLS?
A Real-Time Locating/Location System (RTLS) is used to determine the location of enterprise assets within a facility and to track changes in their position in real time. The operation of RTLS systems can be based on various technologies, including Bluetooth Low Energy (BLE), Ultra-WideBand (UWB), 5G, radio-frequency identification (RFID), and others. The first RTLS systems, dating back to the late 1990s, used RFID technology. Today, the most popular option, due to its high location accuracy — below one meter — is UWB technology.
To monitor resources in real time, transmitters known as tags, labels, markers, or locators are used, along with receivers often referred to as concentrators, hubs, gateways, or anchors. The concentrators collect data from identifiers worn by employees or mounted on equipment. Naturally, this setup requires a system where the gathered data can be visualized on a facility map or used to generate charts essential for process analysis. Discover how the Romotus RTLS system works.

The use of real-time location system in bottleneck analysis – heatmaps and spaghetti diagrams
Real-Time Location Systems (RTLS) are closely aligned with the concept of Lean Management, which focuses on identifying and eliminating waste in processes, including bottlenecks. Using the location data collected by RTLS system, we can visualize our processes through tools such as heatmaps, spaghetti diagrams, or other types of charts (e.g., bar, pie, or box plots). These tools enable process analysis and support the planning of optimization strategies.
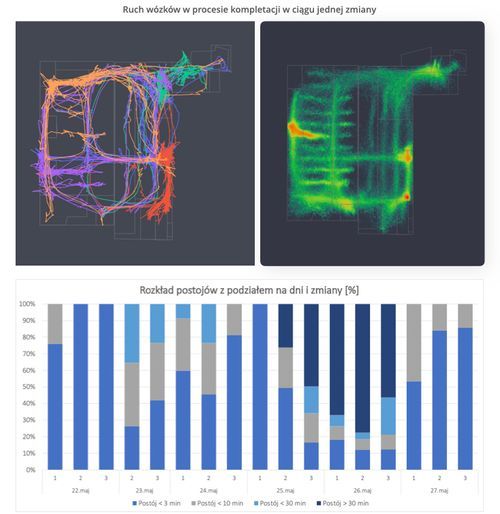
Benefits of RTLS. Why implement a real-time locating system (RTLS) in a manufacturing facility?
- identification of manufacturing bottlenecks
- elimination of production downtimes
-
increased production efficiency
-
tracking assets' locations and optimizing routes
- enhanced throughput and operational efficiency
- identification and diagnosis of process inefficiencies (muda)
-
environmental monitoring of resource locations such as tools, scanners, materials, finished products, autonomous robots (AMR/AGV), and employees
-
monitoring employee safety, e.g., in hazardous zones
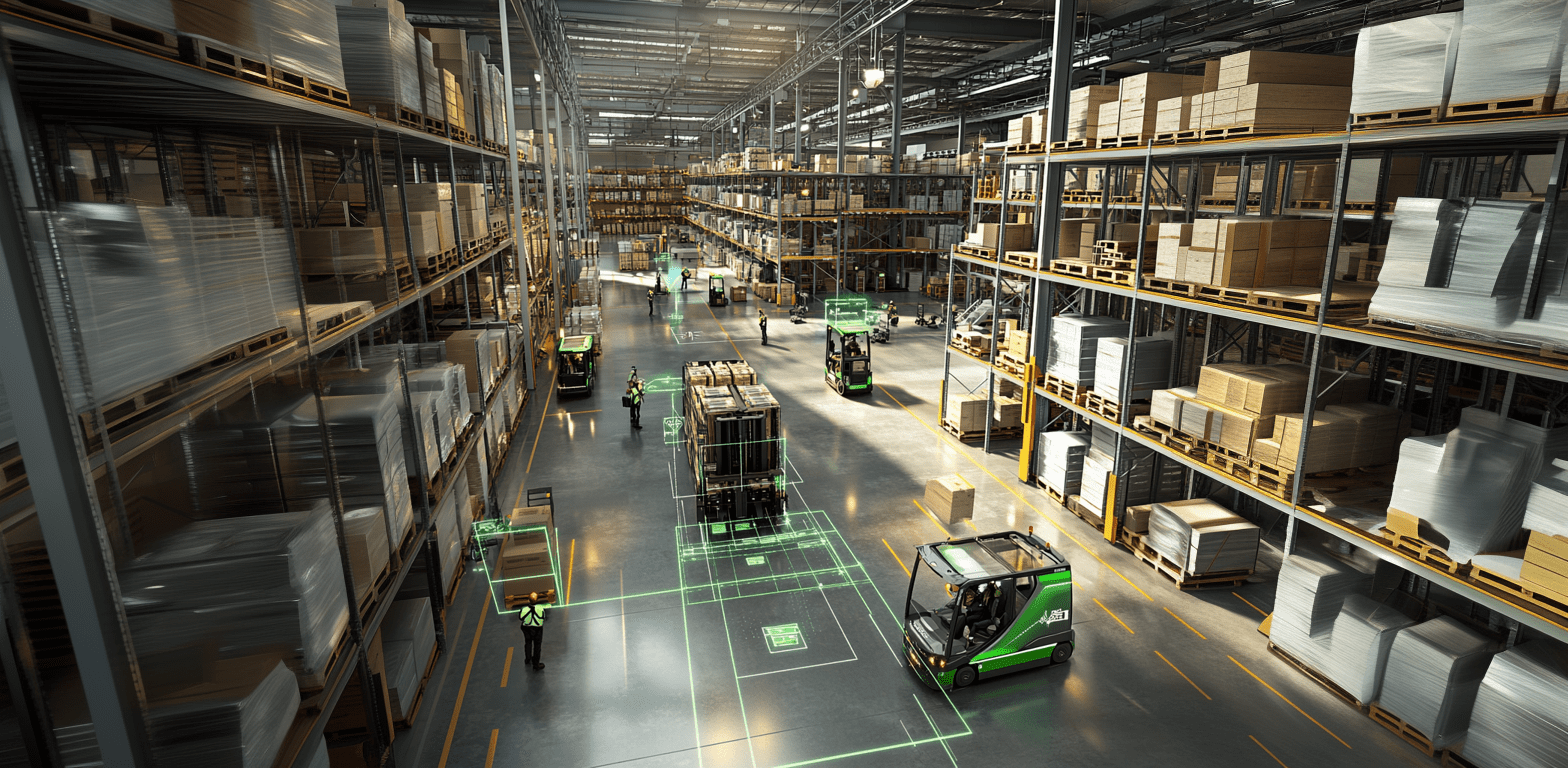
RTLS technology — key aspects of implementing corrective actions
We now understand what bottlenecks are, what their consequences are, and which tools can help identify and eliminate them. Now is the time to consider how to effectively implement corrective actions to improve processes. These actions may include various measures such as repositioning machines, mapping employee skills, altering resource flow routes, improving production schedules, adjusting inventory levels, or enhancing team qualifications. The approach depends on the specific issue to be addressed. Addressing bottlenecks should follow a systematic, step-by-step process, rather than attempting to analyze all areas of the factory simultaneously. A critical element is engaging employees in the process of overcoming production bottlenecks. They are closest to daily challenges and can provide valuable insights into real-world problems. A leader who actively communicates with the team can learn about difficulties in the warehouse or production area. Moreover, with RTLS technology leaders can closely examine highlighted areas while building employee awareness by explaining the purpose and benefits of the implemented corrective actions.
RTLS Romotus — the best RTLS solution for your factory
The Romotus RTLS indoor tracking platform enables the real-time location of vehicles, employees, and other assets. It is used to optimize transportation, increase resource utilization efficiency, coordinate work processes, and manage workplace safety. Its flexibility and scalability allow the system to be tailored to the specific needs of any organization, regardless of its industry or size. As a result, RTLS Romotus becomes not just an indoor location system but a critical element of strategic management, supporting long-term operational improvements and enhancing workplace safety.
Using RTLS Romotus with other manufacturing technology
The data collected and processed by the RTLS Romotus — AIUT's indoor location system — can also be used to launch a digital twin, allowing the replication of physical objects and processes in a virtual environment. Additionally, it aids in defining routes for autonomous AMR vehicles and monitoring their working environment.

Implementing RTLS Romotus in manufacturing sectors — use cases for RTLS system
- Automotive: Monitoring the location of vehicles and components
- Consumer Goods (FMCG): Managing inventory and reducing order-picking times
- Distribution Centers: Intelligent management of pallet and vehicle movement
- Appliance Manufacturers: Tracking components and finished devices
Read our RTLS use cases for improving productivity in production nests, improving warehouse efficiency, and AGV productivity improvement.
The AIUT Indoor Localization Platform - RTLS Romotus was awarded the top prize in the prestigious competition "Innovative Product for Logistics, Transport, and Production 2024" during the XXIII Logistics, Transport, and Production Gala 2024 in Warsaw, organized by the Eurologistics Media Group.
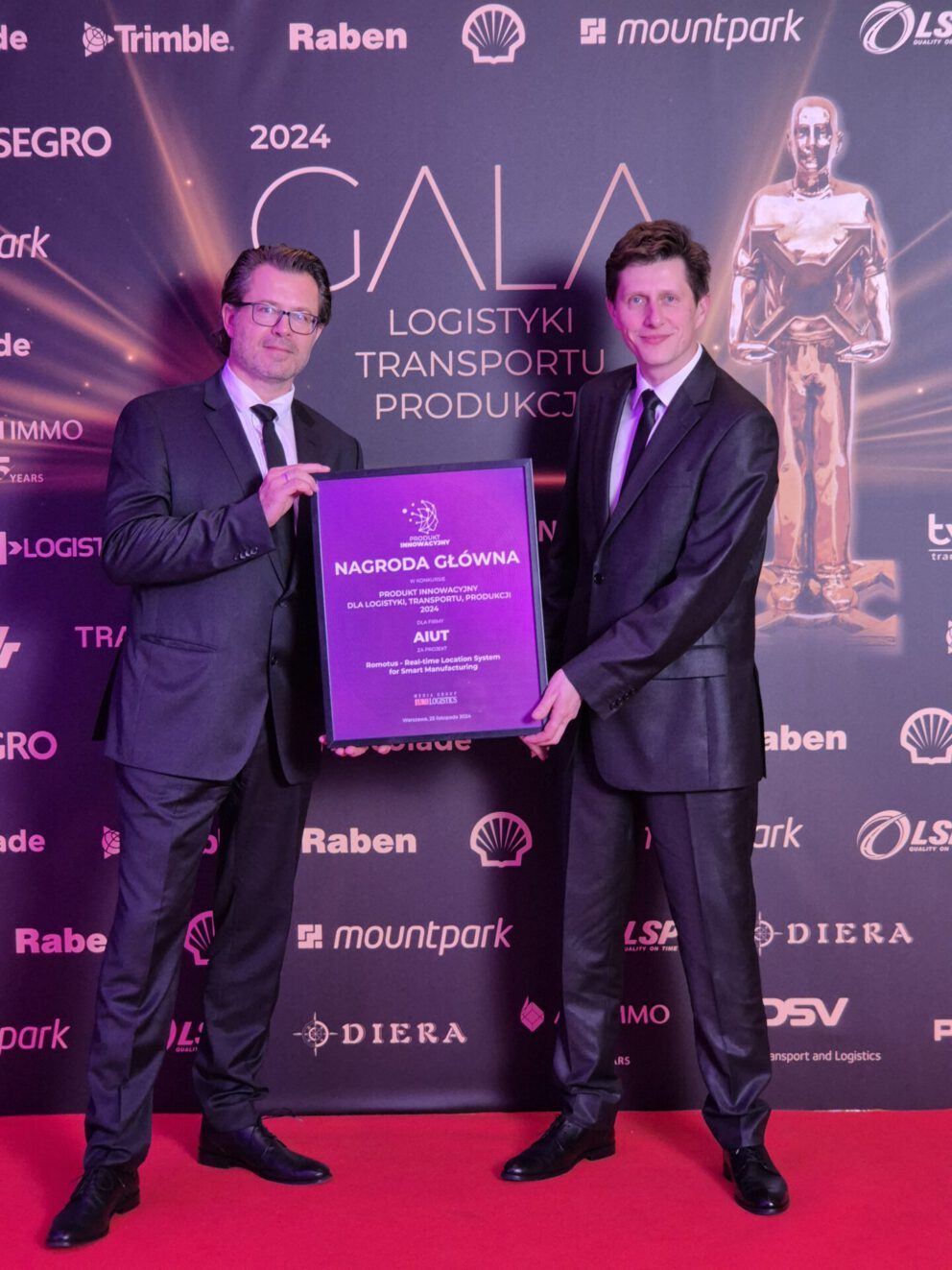
Summary
Bottlenecks in production and logistics processes are elements that limit system throughput, leading to downtime, waste, and reduced efficiency. Identifying and eliminating these bottlenecks is essential for improving a company's performance. A system for location tracking technology, such as AIUT's RTLS Romotus, is one of the modern tools supporting the elimination of bottlenecks. Tracking resources in real-time, enables precise process monitoring and proper analysis, aiding in the identification of inefficiencies and the implementation of corrective actions. Utilizing such solutions allows for long-term process optimization and better resource utilization, while simultaneously enhancing efficiency and safety within the company.
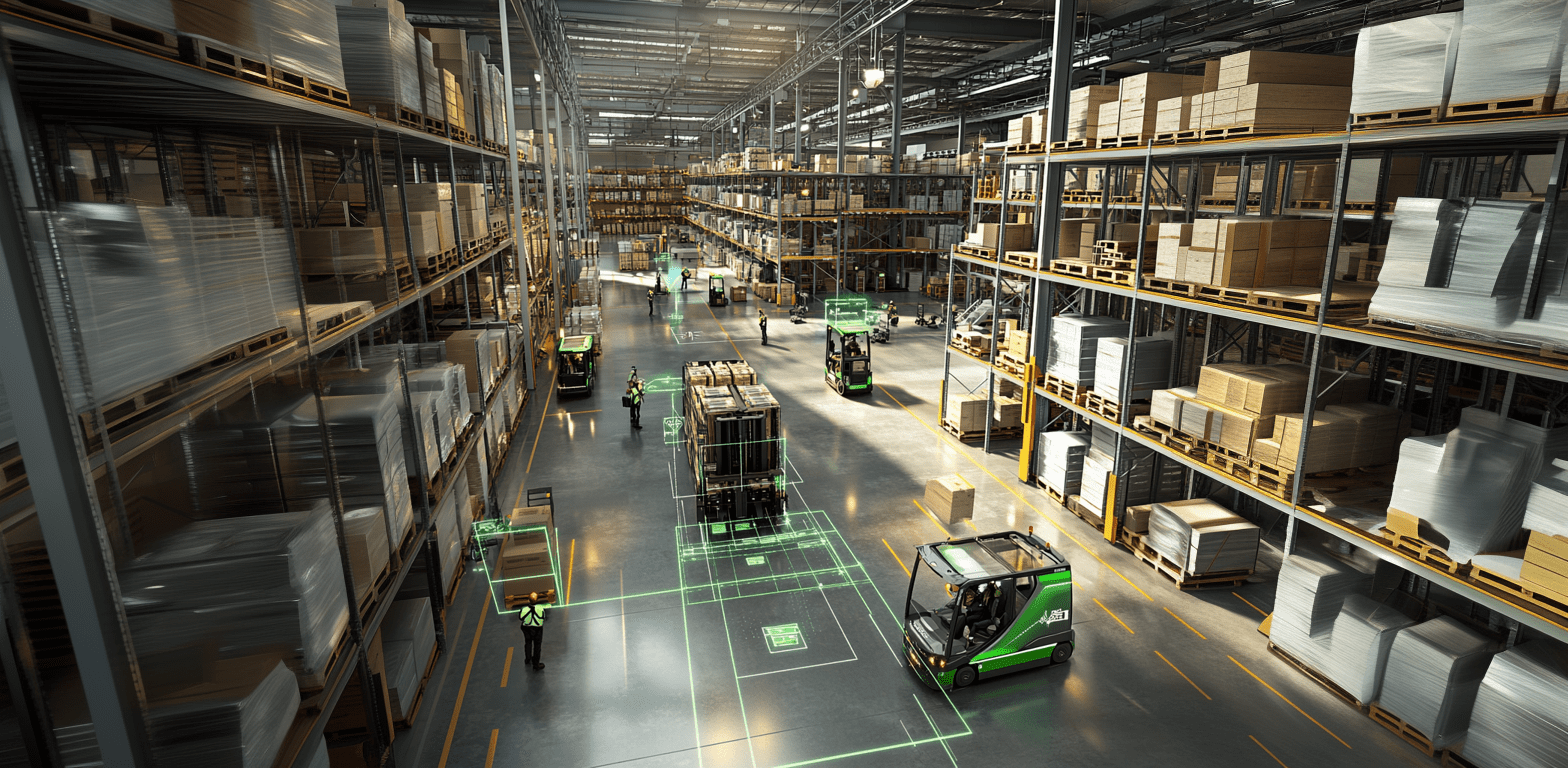
Eliminate bottlenecks with RTLS Romotus
Discover how our real-time location system can revolutionize your processes. Optimize, monitor, and boost efficiency today.