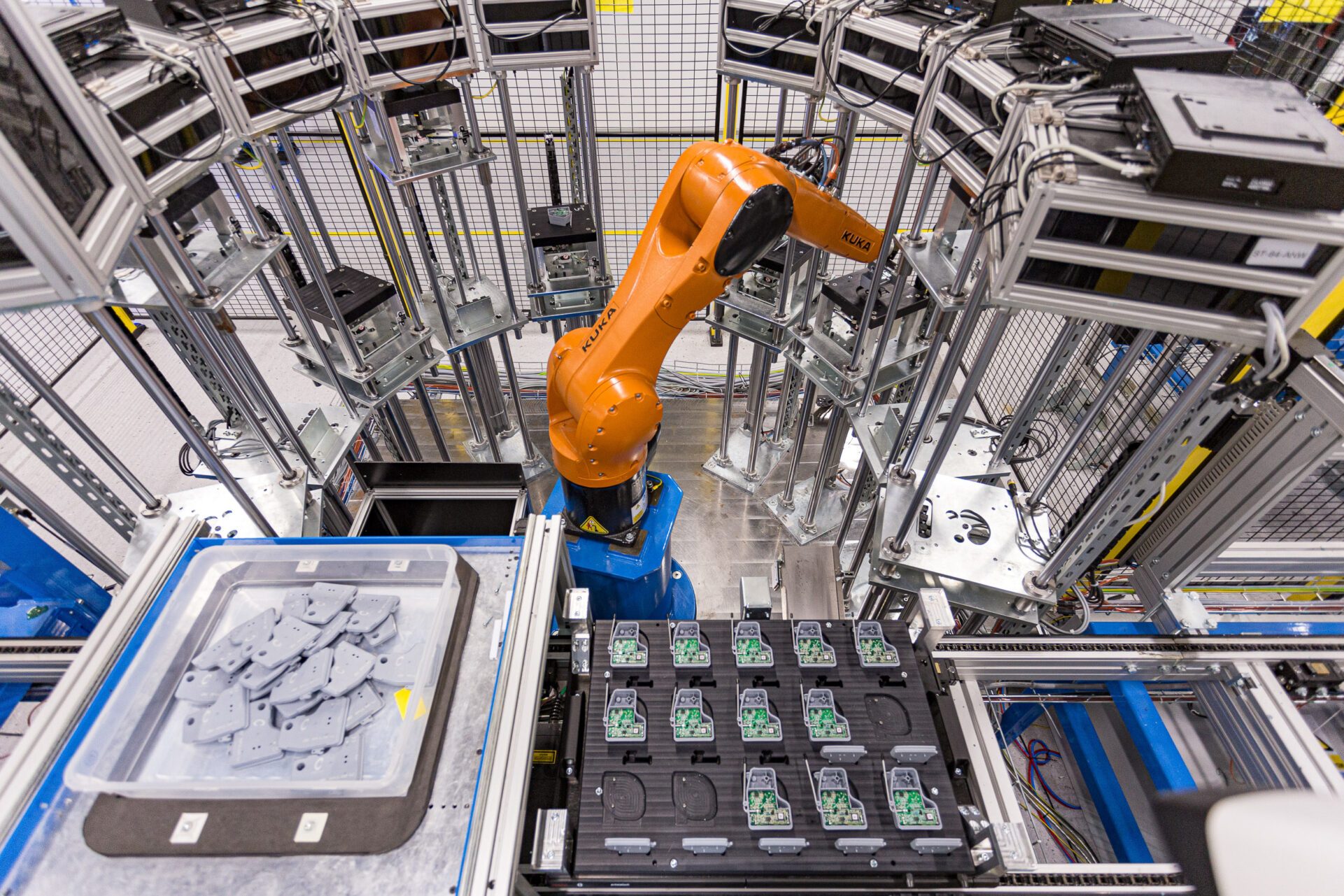
OEM in action: How does electronics manufacturing work?
In this article, you will learn:
-
what is the process of electronics manufacturing?
-
who is an OEM manufacturer in the electronics industry?
-
what are the benefits of working with an OEM electronics manufacturer?
-
what drives the OEM electronics assembly market?
-
what stages does the electronic manufacturing process include?
-
what are THT and SMT component assemblies?
-
how do you choose an electronics manufacturer?
Electronics play a crucial role in nearly every industry. The increasing complexity and number of components required for advanced consumer electronics manufacturing and industrial electronics production demand collaboration between various suppliers. To illustrate the scale – a single smartphone contains an average of 160 chips, while an electric vehicle may require up to 3,500 chips. And that's just a fraction of the electronic components necessary for its operation. To focus on developing their products and services, end-device manufacturers outsource electronics assembly to specialized companies. These companies are known as Original Equipment Manufacturers (OEMs). In this article, we explain the role of OEM manufacturers, the advantages of partnering with them, the key stages of the electronics production process, the differences between THT and SMT assembly, and how OEM services are evolving in the electronics market.
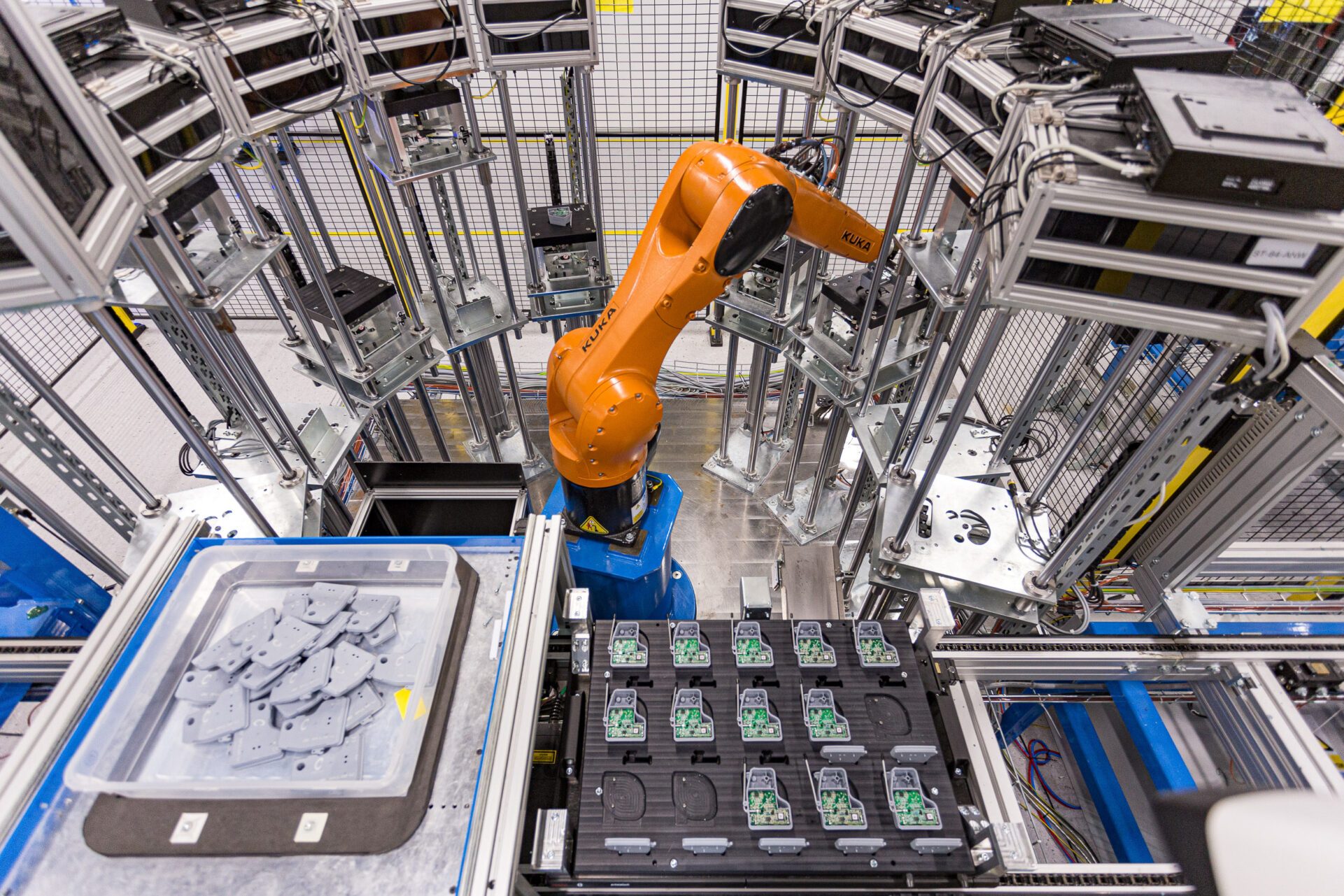
Electronics manufacturing process – what does it involve?
Electronics manufacturing is a complex process that requires both specialized knowledge and compliance with specific standards. It begins with defining PCB design and the circuit board manufacturing process, followed by prototyping, electronic circuit board assembly, programming of integrated circuits (IC), functional testing, and certification. Each of these stages is critical to ensuring high-quality electronic product manufacturing before the final product reaches the market. The individual stages of this process will be discussed in detail in the following sections of this article.
Who is an OEM manufacturer?
Original Equipment Manufacturers (OEMs) produce electronic devices such as computer processors, printed circuit boards (PCBs), displays, and other components that later become integral parts of finished products. OEMs play a critical role in electronics contract manufacturing (ECM), providing components to consumer electronics companies and industrial electronics manufacturers alike. They possess the necessary expertise, experience, and know-how to manufacture electronics for other companies — namely, end-device manufacturers. A well-known example of an OEM is Intel, which manufactures processors and other electronic components used by brands like Lenovo in their computers. By partnering with an OEM manufacturer, Lenovo can focus on developing its products and services without the need for specialized knowledge in component manufacturing.
OEM manufacturers also provide turnkey electronics production — tailored to a customer’s individual needs. The end manufacturer purchases electronic devices or technologies developed by the OEM and sells them under its brand. Depending on the agreement between the parties, design rights may be fully or partially transferred. An example of such an OEM is AIUT’s EDM division, which offers comprehensive project support — from hardware and firmware design, prototyping, and testing of electronic devices to certification and market deployment.
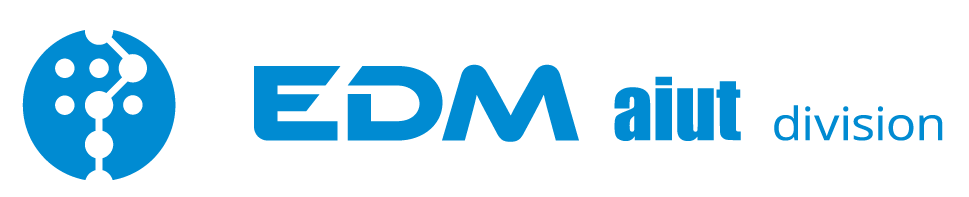
Benefits of working with an OEM manufacturer
- High-quality electronic manufacturing
- Reduced time-to-market for new products
- Focus on core business without needing in-house electronics production expertise
- Full customization of electronic devices to meet specific client requirements
- Lower production costs for end products
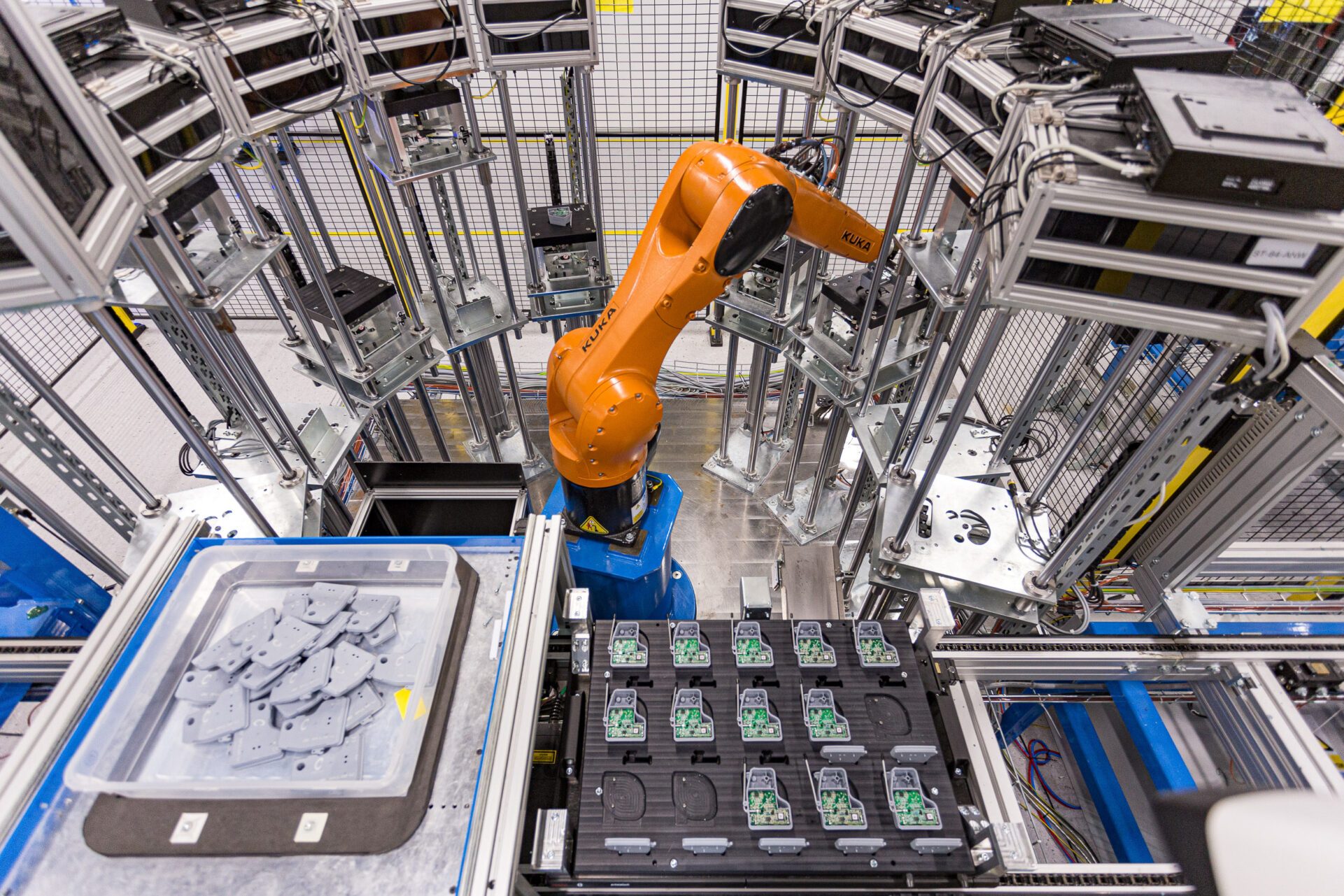
What does the OEM electronics assembly market look like?
The OEM electronics assembly market reached a value of $57.07 billion in 2023 and is set for dynamic growth in the coming years. Forecasts indicate that its value will rise to $76.45 billion by 2032. This market comprises various segments, including consumer electronics manufacturing, automotive electronics manufacturing, industrial electronics production, as well as electronics for telecommunications and healthcare applications. Below, we outline the size of the OEM electronics assembly market across different industries and the key factors driving their growth.
Key drivers of the OEM electronics assembly market
- Growing demand for consumer electronics, such as smartphones, tablets, and smart home devices
- Increasing consumer expectations for higher device performance
- Rising popularity and demand for electric vehicles (EVs)
- Advancing industrial automation, driving demand for sophisticated electronic components
- Companies striving to optimize production processes and improve efficiency
- Cost reduction in manufacturing through device integration and machine learning-powered analytics
- Ongoing digital transformation, including the adoption of cutting-edge technologies
- Industry 4.0 solutions, boosting communication advancements (IoT)
- The rapid development of telecommunications, including global connectivity and 5G technology
- Growing integration of various processes within factories
- Increasing need for production outsourcing, helping companies cut costs and reduce project turnaround times
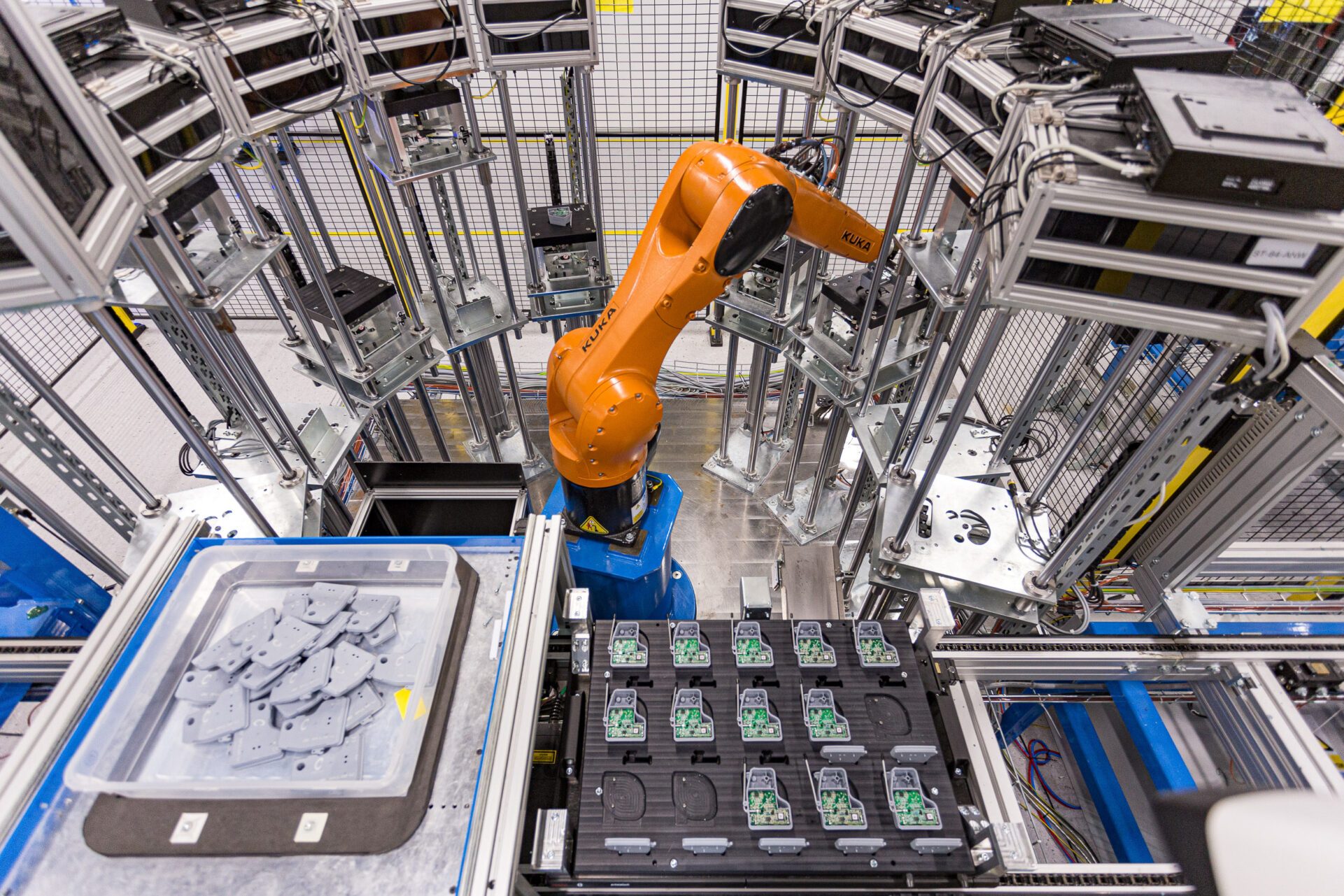
Stages of electronic device manufacturing – PCBA technology
1. Electronic circuit design, component procurement, and prototype production
The OEM manufacturer, in collaboration with the client, defines the project specifications and prepares a cost estimate. Once the terms of cooperation are approved, detailed technical documentation is created. A crucial part of this documentation is the BOM (Bill of Materials), which contains a complete list of electronic device components. A well-structured strategy ensures a smooth production process while maintaining budget compliance.
Next, the printed circuit board (PCB) layout is designed using specialized engineering software, ensuring optimal PCB design for efficiency and manufacturability. This stage is crucial in the circuit board manufacturing process, ensuring high-quality electronic products that meet industry standards. It requires expert knowledge to ensure key design parameters, such as effective heat dissipation, appropriate trace width, proper spacing between elements, and other critical structural aspects. Based on the designed electronic device model, the appropriate component mounting technology for the PCB is selected. The OEM manufacturer procures all necessary electronic components following the BOM document, ensuring smooth assembly and production.
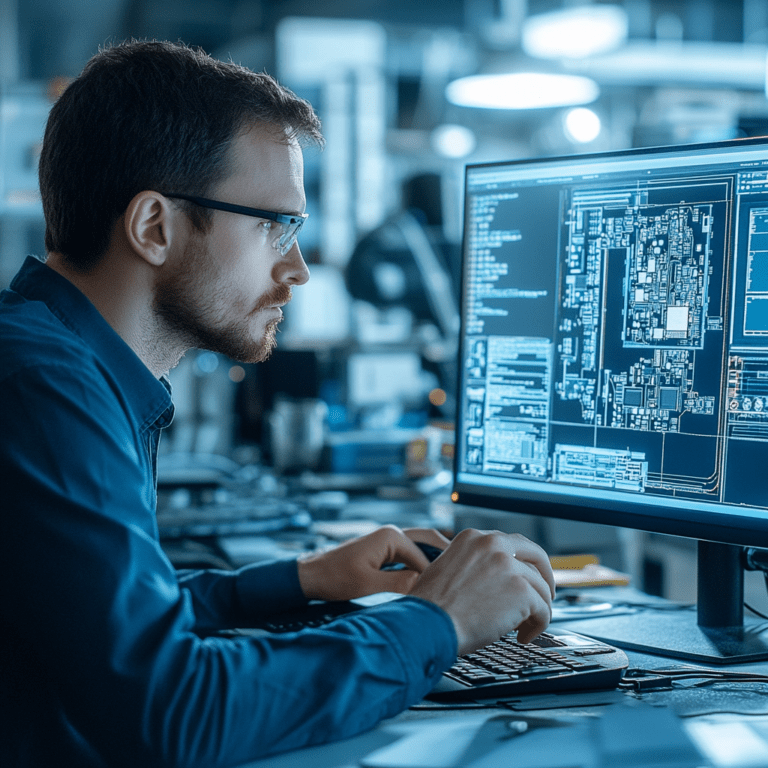
2. Mounting electronic components on the PCB
The assembly of components on a PCB (Printed Circuit Board) is a crucial stage in electronics manufacturing. Proper placement of elements and precise connections between them ensure the device functions correctly by minimizing electrical signal interference. There are two main methods of PCB component assembly:
- Surface Mount Technology (SMT)
- Through Hole Technology (THT)
Both techniques use chemical processes, such as etching conductive paths and copper deposition, to create conductive patterns on the PCB.
Surface Mount Technology (SMT)
SMT assembly is used for attaching small components such as integrated circuits, transistors, and receivers. These components are precisely placed on the PCB, typically using an automated pick-and-place assembly line. The process begins with the application of solder paste onto the PCB using a screen-printing machine. This machine scans the board’s surface and accurately applies solder paste to designated component locations. Next, the PCB is transferred to the pick-and-place machine, which picks components from reels, adjusts their angle using a vision system, and places them onto the previously applied solder paste. This process is repeated for all components on the PCB. Once component placement is complete, the Automated Optical Inspection (AOI) system checks the board for defects. The machine scans the assembled PCB and compares it with pre-set quality standards, detecting potential issues such as missing components, incorrect rotation, or insufficient solder paste application. The prepared PCB, with components attached to the solder paste, then enters a reflow soldering oven, where it undergoes controlled heating with precisely adjusted temperature and heating speed. As the temperature increases, the solder paste melts, permanently bonding the components to the PCB and creating secure electrical connections. After the soldering process is completed, the board is cooled and moves on to the next inspection stage to ensure the quality of component assembly.
Through Hole Technology (THT)
THT assembly, also known as Through Hole Technology, is used for mounting larger components on the PCB, such as capacitors, relays, and connectors. The process begins with preparing the PCB by drilling holes in designated locations. Once the holes are ready, electronic components are inserted and soldered from the underside of the board. During wave soldering, the PCB is heated, causing molten solder to flow into the drilled holes and creating strong and reliable electrical connections. This method is particularly useful in applications requiring high mechanical stability, ensuring components remain resistant to vibrations and shocks. Additionally, to protect electronic components from environmental factors such as moisture and contaminants, protective coatings are applied. Common protective materials include insulating varnishes and silicones, which enhance durability and reliability in various operating conditions.
3. Inspection of component assembly
After the PCB is removed from the reflow soldering oven, it is cooled and subjected to a quality control check to verify the accuracy of the soldering process. This inspection is carried out using Automated Optical Inspection (AOI), which identifies missing, misaligned, or damaged components and detects defective solder joints. The inspection process may include X-ray verification for more advanced electronic devices. This technology enables a detailed assessment of solder joint quality, including those hidden beneath component casings, ensuring the highest standards of reliability and performance.
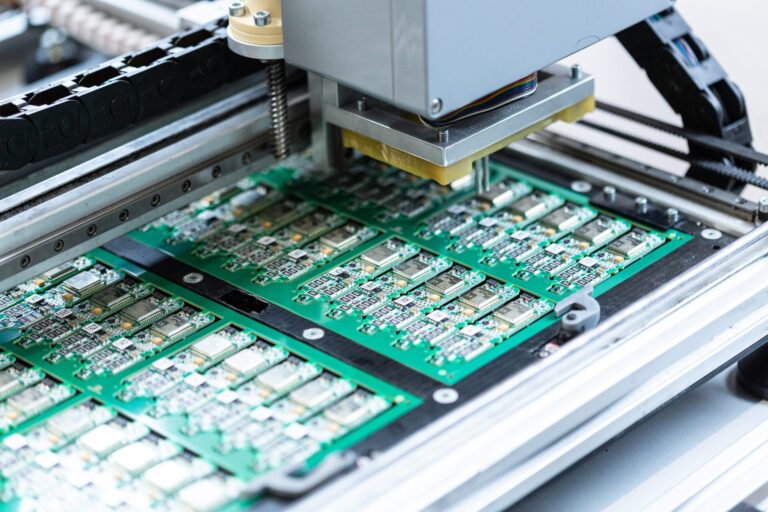
4. Programming of integrated circuits (ICs)
During this stage, firmware is uploaded to programmable devices such as microcontrollers and microprocessors mounted on the PCB. This allows the device to function according to the project specifications, enabling it to receive signals, read values, and transmit data to a server. The programming process also serves as an additional quality check, ensuring that components are correctly positioned and installed, that signals are free from interference, and that the device operates as expected.
5. Functional testing
The assembled PCB undergoes functional testing, which can be performed either automatically using Automated Test Equipment (ATE) or manually with probes and other measurement tools. Additionally, environmental testing is conducted to simulate real operating conditions, such as specific temperature and humidity levels. These tests help verify whether the product will function reliably under actual usage conditions.
6. Custom wiring, prototyping, and enclosure production
Depending on customer requirements, the OEM manufacturer may design a prototype of the device's enclosure and outsource its production. During the prototyping phase, 3D printing is often used as a cost-effective and rapid method for testing different design concepts. Once the final design is approved, a plastic injection mold is commissioned based on the prepared model. The finished enclosure is then assembled with the PCB and additional components, such as buttons, displays, and wiring, creating a fully integrated device ready for further testing or shipment.
7. Outgoing Quality Control (OQC)
At the final stage of production, the finished device undergoes an Outgoing Quality Control (OQC) process, where it is verified against the technical documentation and checked for compliance with industry certifications, environmental regulations, safety standards, and quality requirements. The compliance process also considers the specific regulatory requirements of the target market where the device will be used. Once all necessary certifications are obtained, the OEM manufacturer delivers the final product, ready for deployment in various applications based on customer needs.
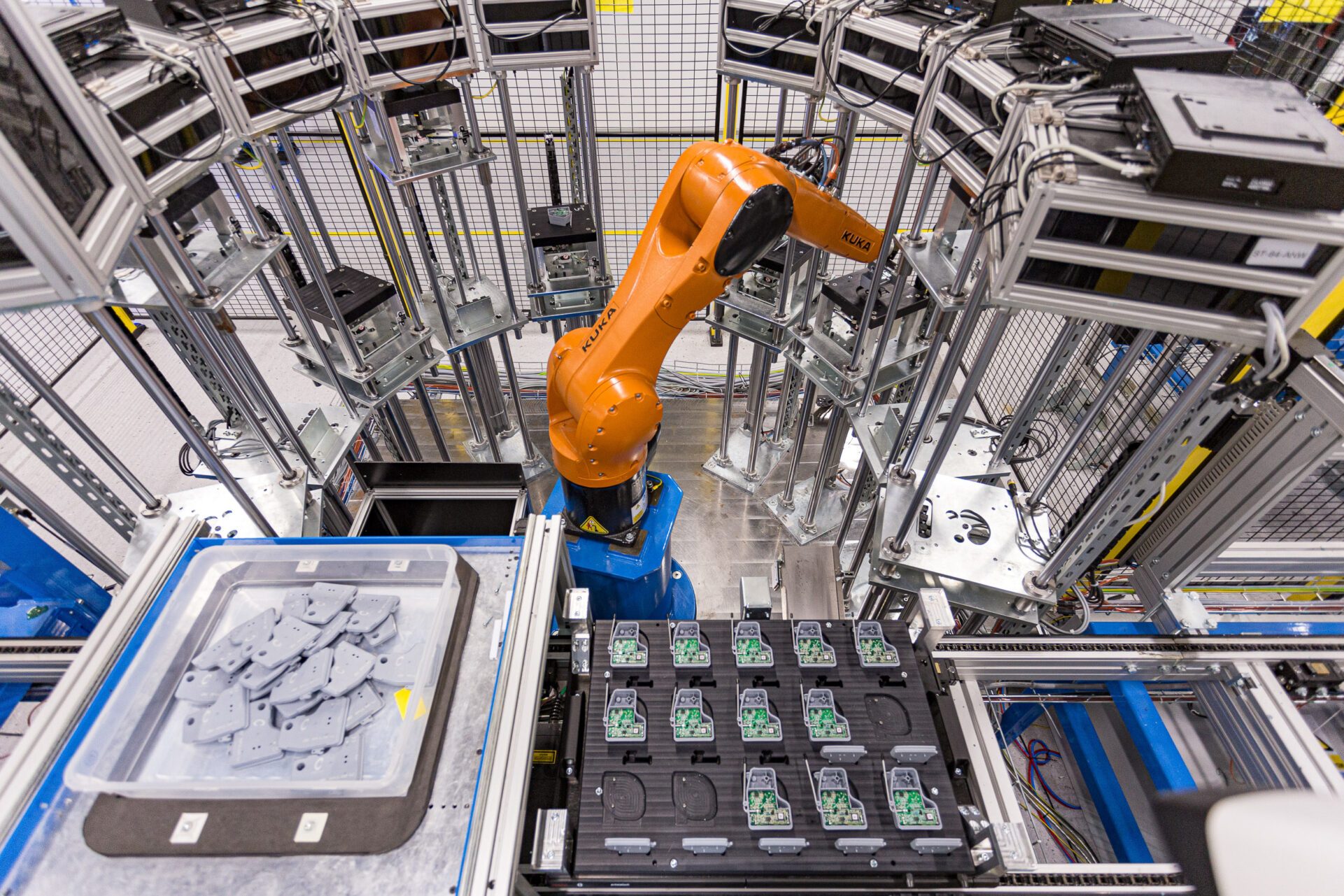
Choosing an electronics partner in the OEM market
Electronics manufacturing services for industrial applications are offered by many suppliers. However, selecting the right partner requires careful consideration of their experience in electronics production management and track record of completed projects. A comprehensive electronics manufacturing process, including design, component assembly, and technological consulting, should be handled by an OEM manufacturer committed to maintaining high-quality standards in electronic device production.
AIUT EDM – comprehensive industrial electronics manufacturing
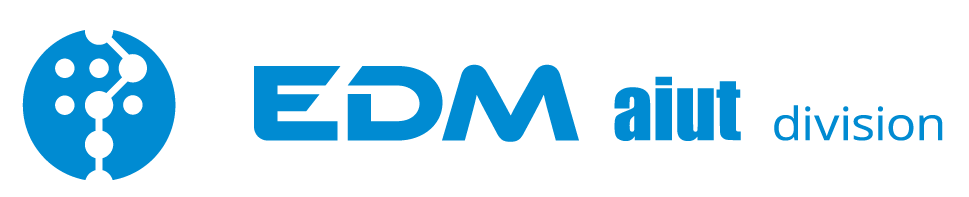
AIUT EDM – Experienced OEM manufacturer for industrial electronics
AIUT EDM is an experienced OEM manufacturer offering comprehensive support in the design and production of electronic devices. The company specializes in developing cutting-edge technologies, delivering turnkey solutions from the design phase and component selection to assembly and testing. With state-of-the-art technological infrastructure, AIUT EDM ensures the high-quality production of electronics, guaranteeing compliance with industry standards. Collaboration with AIUT EDM also provides access to comprehensive support, including both warranty and post-warranty service. Additionally, through partnerships with renowned electronic component suppliers, AIUT EDM guarantees top-quality devices and exceptional product reliability. The company not only manages the production process but also offers consulting on optimal solutions, supporting clients at every stage of their project’s execution.
Summary
The production of electronic devices is a complex process that requires precision, specialized knowledge, and access to advanced manufacturing technologies. OEM manufacturers play a key role in global electronics manufacturing, ensuring the highest quality standards while reducing costs and time-to-market. Partnering with OEM manufacturers allows companies to focus on their core competencies while benefiting from comprehensive support in design, component assembly, and device testing. In today's market, driven by innovation and reliability, OEM manufacturers play a key role in meeting these demands. Their expertise and advanced technologies not only accelerate time-to-market but also reduce costs and ensure the highest quality standards. Choosing the right OEM manufacturer is a strategic decision that can enable companies to execute ambitious technological projects and strengthen their position in the global market.
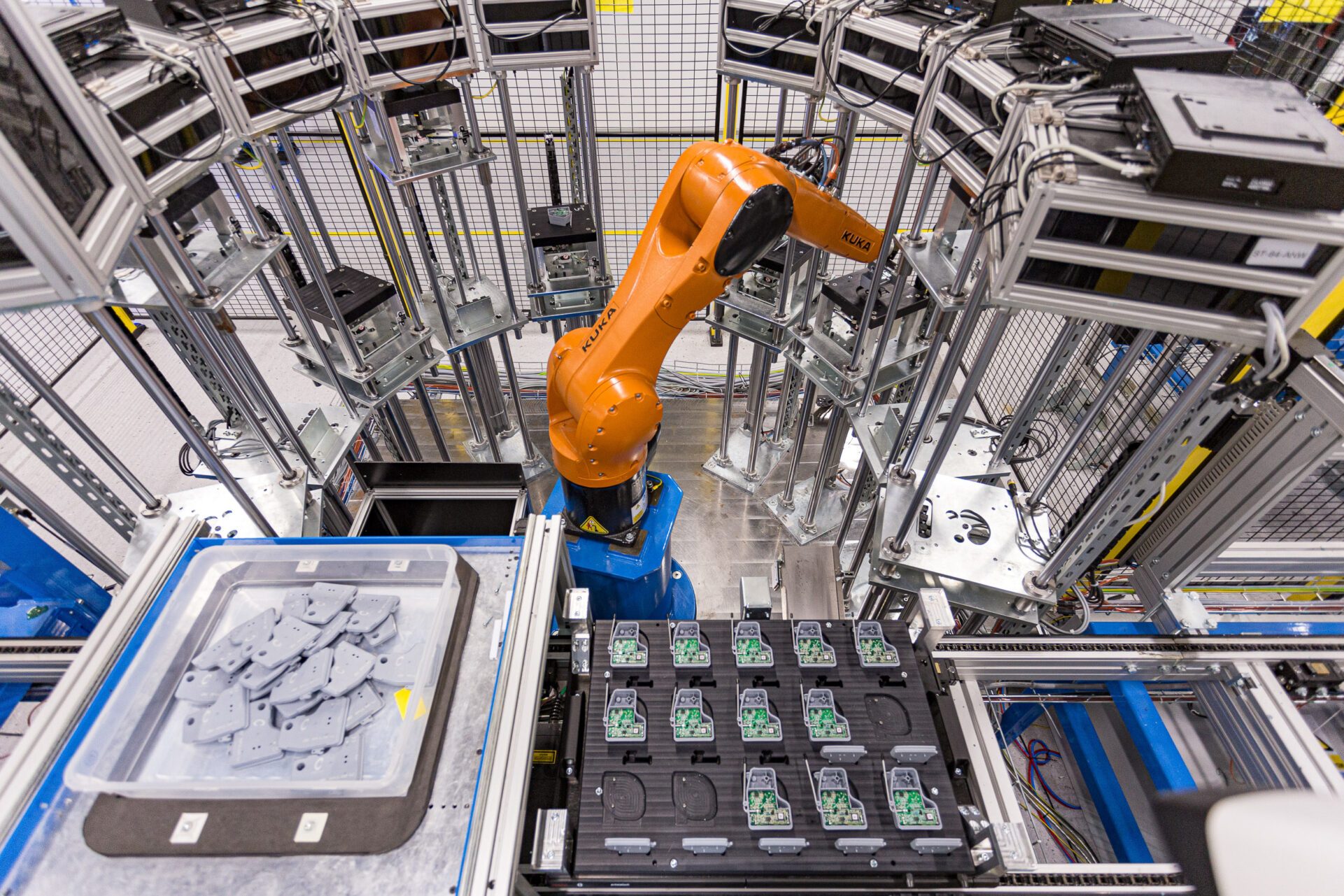