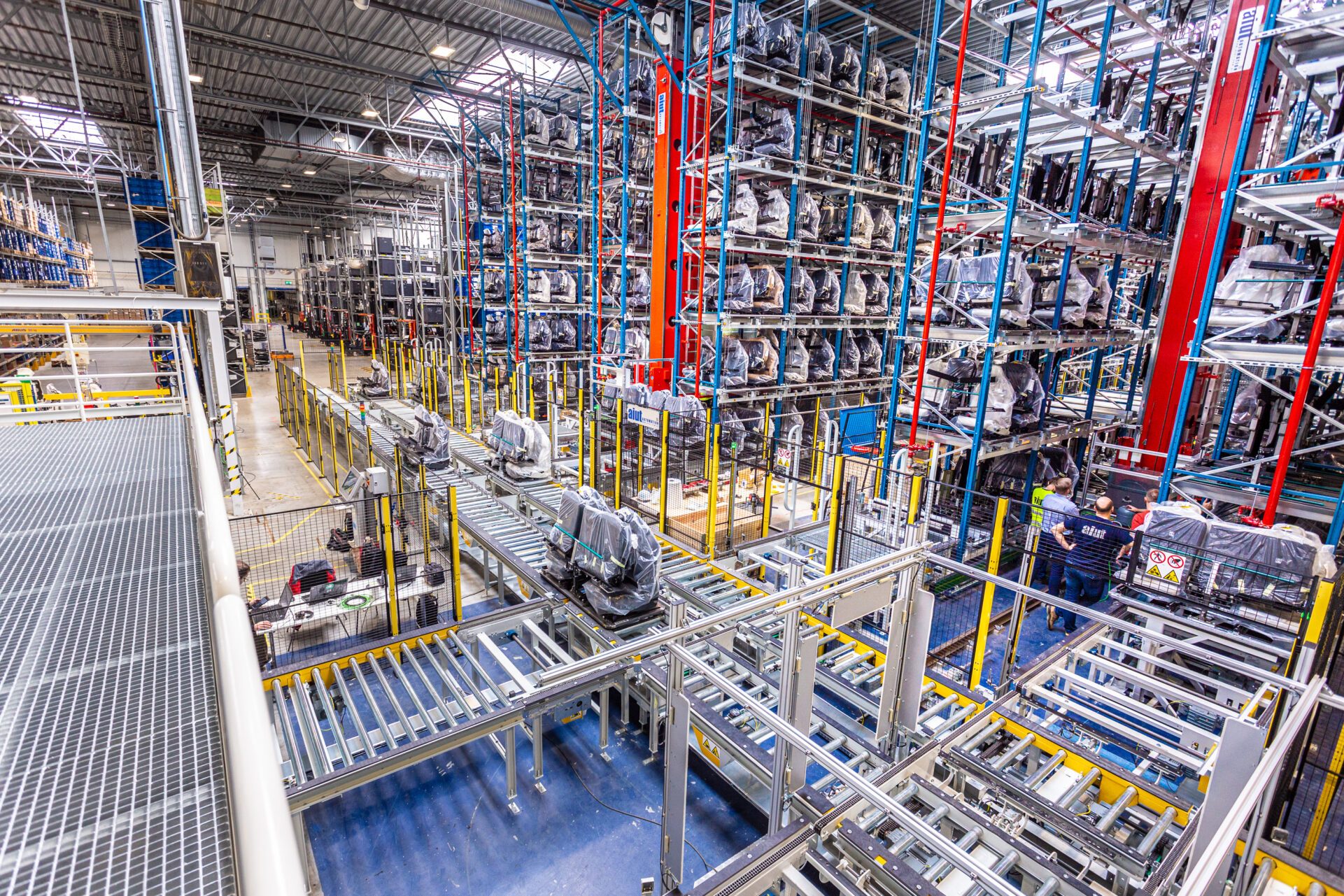
- Warehouse solutions – ASRS
- Automated storage and retrieval systems
- Automation and robotics
- Solutions
Warehouse solutions – ASRS
We design and implement automated storage and retrieval systems (ASRS).
At AIUT, we co-create the latest trends in intralogistics. We are a leader among providers of advanced robotics and automation systems for global industrial markets. Our comprehensive solutions are tailored to client’s needs, in order to achieve their goals and successes in the market together.
Mobile robots such as AMR series F, conveyor transport systems, automatic sorters, and high storage systems that can reach over 40 meters in height are just examples of intralogistics solutions that have become an integral part of warehouses and distribution centers today. Integration, customization, and utilization of these solutions to individual needs are key. Development, following new trends, and technological progress will ensure companies’ high competitiveness and the ability to face new challenges.
Transforming manual warehouses into automated ones is the direction of the market. The basis for effective investment is the choice of the right technological partner.
Discover our warehouse automation solutions:
For efficient storage and retrieval of materials, pallets, and containers in warehouses – well as in distribution centers, we use advanced storage systems based on: pallet stacker cranes, miniload, automatic pallet shuttles, or our innovative solution of mini stacker cranes, which are dedicated to container handling for high-capacity systems. Our set of possible solutions also includes less typical systems, such as stacker cranes for transporting car bodies, large-volume storage, or other less typical materials or structures.
Automated manufacturing buffers and smooths out production in case of line stops and provide the possibility of product sequencing, particularly when there is a large variety of assortments. Also, they minimize the risk of downtime in just-in-time production and provide its greater flexibility.
We use conveyor transportation systems to move pallets. We begin the construction of such systems with a full analysis of the capacity, dimensions, and weight of the transport media. Depending on the needs of a particular plant, different types of conveyors are used: roller, chain, belt, and modular. Systems built with roller conveyors are used on sections of horizontal transport lines for picking or buffering pallets. Chain systems, on the other hand, are used where pallets must be transported laterally due to limited space. Belt conveyors are used where there is a difference in level and small items are transported. Conveyor modules can be mechanically driven or work through the force of gravity. Roller and chain conveyors are most commonly used to transport pallets, while roller and belt conveyors are used for containers and cartons.
In a warehouse designing, many cooperating devices are used to help streamline warehouse operations. These can include labelers, through-feed scales, automatic wrappers, strapping or stacking machines and a lot more.
Automated sorters guarantee highly efficient and almost error-free segregation of items and parcels in a time incomparably shorter than during manual operations. Sorters can support companies at many points in production and logistics processes, including order picking or final sorting at parcel release. They are also used in the process of returning goods. When selecting sorters; we take into account the type of items to be sorted and the available space in the warehouse to optimally plan the physical flow of goods. Non-standard size, length or lack of packaging of goods that a company wants to segregate automatically is not a problem from our perspective, as we create a project for individual customer needs.
The solutions designed at AIUT, thanks to the traceability systems used, also allow tracking and full control of the sorting process. Errors in the sorting process are reduced by vision systems. Data from each stage of sorting goods are archived for future analysis and control, and photos taken of individual packages leaving the sorter allow full traceability of shipments and their condition at the time of release.
Pallets are platforms supported by means of transport, i.e. forklifts, which allow us to transport goods in a simple way. We call palletization the whole process of grouping goods on a pallet in the most efficient and safe way possible. Robotization of pallet loading and unloading stations brings measurable results in reducing operating costs. The robots we implement ensure the repeatability of the processes, improving the quality and efficiency of packing pallet loads. They influence a more efficient flow of warehouse goods and better control of inventory as well as warehouse space.
AIUT series F autonomous mobile robots provide efficient and unmanned cargo transportation. The heart of the intralogistics system using series F robots is the Qursor platform. Our system enables the optimization of logistics processes in warehouses, distribution centers, or manufacturing plants. It reduces inventory and labor costs, improves production efficiency, eliminates anomalies and collision risks, as well as enhances employee safety, and enables real-time process monitoring.