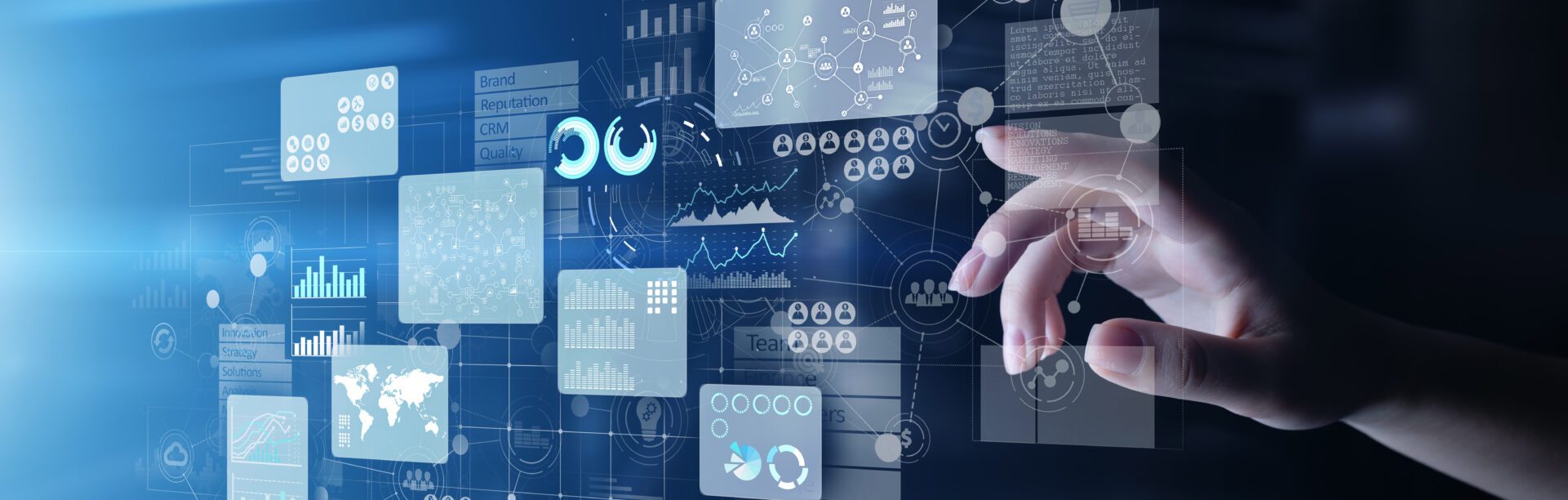
Digital Twin: How to optimize production with data?
From this article, you will learn:
-
what does the digital twin market look like?
-
what is a digital twin, and how is it created?
-
what does the process of datafication involve?
-
what are the differences between a digital twin and a digital model?
-
what are the benefits of implementing a digital twin in a manufacturing company?
-
why high-quality data is crucial for building a digital twin?
Every manufacturing company should strive to digitize its processes to implement its strategy and gain a competitive edge effectively. Achieving this requires collecting high-quality data about products, processes, and systems. These data enable the creation of digital models and the execution of simulations in a virtual environment. One technology that facilitates such activities is the digital twin.
Digital twin technology finds broad applications in areas such as production optimization, quality control, predictive analysis, supply chain management, intralogistics, healthcare, smart cities, building management, and the design and development of new products. By leveraging digital twins, companies can make better data-driven decisions while eliminating ineffective or erroneous scenarios.
In this article, we will discuss what digital twin technology is, the current state of the digital twin market, the benefits of implementing this solution, the importance of collecting high-quality data, and how to approach building a digital twin in a manufacturing company.
The global digital twin market
According to a report by MarketsandMarkets, the global digital twin market was valued at $10.1 billion in 2023. It is projected to grow at a compound annual growth rate (CAGR) of 61.3% from 2023 to 2028, reaching $110.1 billion by 2028. The report highlights that the dynamic growth of the digital twin market is driven by increasing demand for cost reduction and operational efficiency in supply chains. Another significant factor contributing to this progress is the growing adoption of digital twins in the healthcare sector, as well as the broad application of this technology in predictive maintenance of machinery and equipment.
What is a digital twin?
A digital twin is much more than a virtual replica of physical objects, processes, or systems. Unlike digital models, it considers the environment surrounding individual elements. In other words, a digital twin is an integrated and interactive environment that allows users to test and analyze various scenarios in a safe, virtual space. The concept of mirroring reality in the digital world plays a crucial role in simulating production processes. With the help of a digital twin, manufacturing companies can refine existing solutions or validate new ideas before implementing them in theirs facilities. This approach enables monitoring, analyzing, and optimizing processes in the virtual space without interfering with the actual operation of the plant. As a result, digital verification of assumptions reduces the cost and time associated with implementing inefficient solutions in the real world. Today, the digital twin is an indispensable component of delivering new products and services to customers and serves as the foundation for ongoing maintenance activities.
In summary, a digital twin applied to new solutions being implemented in a factory supports:
- planning,
- designing,
- analyzing,
- testing,
- maintenance activities.
For existing solutions, a digital twin enables:
- monitoring and continuous improvement of production processes.
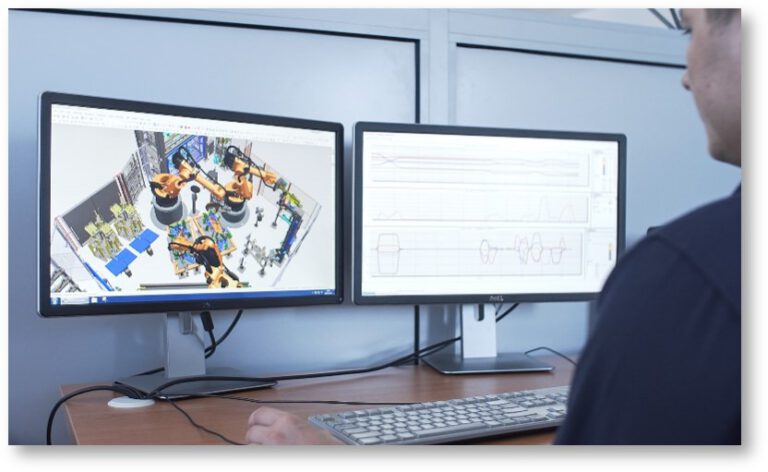
How is a digital twin created?
Design assumptions
Before building a digital twin, a key step is to define what problems it will solve and, on this basis, determine which part of production it will cover. It is also important to set the goals we want to achieve with its help. Then datafication begins, i.e., mapping reality in the digital world using data.
Digital model
In this step, technical specifications and detailed documentation are gathered, including information about equipment, production lines, or entire facilities. The digital model encompasses schedules, product structures (known as BOM — Bill of Materials), and historical data on downtimes or machine inspections. Enterprise Asset Management (EAM) or Computerized Maintenance Management Systems (CMMS), such as IBM Maximo, are frequently utilized for comprehensive resource management. Integrating them with the digital twin allows the company to gain full control over operations and speed up data acquisition processes.
Data collection
Once the 3D models are designed, actual data is introduced, becoming a key resource during process analysis and simulations. This data can include information from machines, devices, IoT sensors, control and monitoring systems (e.g., SCADA), production and warehouse management (WMS, MES), or RTLS systems.
Data analysis
Raw data collected from processes holds little value on its own. The key task is to select the most critical data and transform it into valuable information. Proper analysis enables not only the prediction of failures but also the optimization of production processes and the enhancement of operational efficiency. Machine learning algorithms play a pivotal role here, monitoring data in real time and supporting prediction and automation efforts.
Updating the digital twin
To unlock the full potential of digital twin technology and maximize the benefits of simulations, continuous, bidirectional data exchange between the digital entity and its physical counterpart in real-time is essential. This ongoing exchange of information helps manufacturing companies make better business decisions, manage processes more effectively, and monitor the condition of machinery, including early detection of failures.
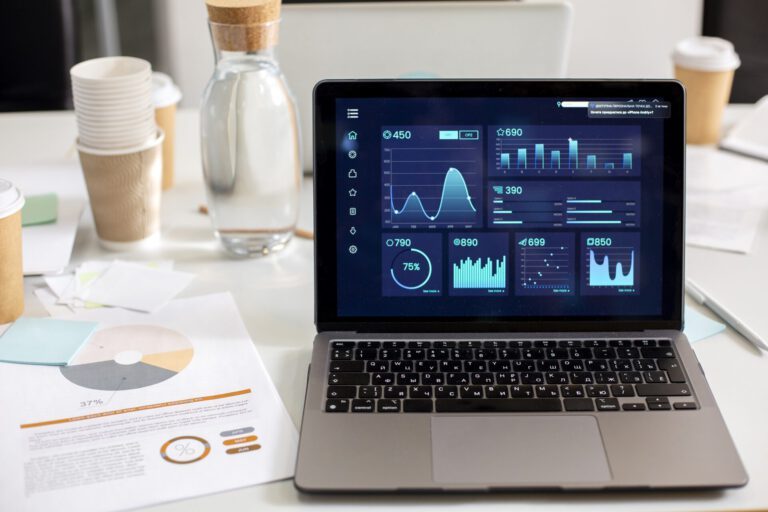
Benefits of implementing a digital twin
- Access to simulations: With a digital twin, companies can perform online simulations and test various scenarios without interfering with real processes. This allows for the verification of machine performance against design specifications, reducing the risk of downtime and shortening the time needed for the implementation of the solution in the facility.
- Increased efficiency: Real-time data analysis enables continuous process optimization and improvement. Digital twins enhance production processes by monitoring and adjusting parameters in real time.
- Improved product quality: Simulations and tests allow companies to make changes to production processes before their actual implementation, resulting in higher-quality end products.
- Reduced downtime and predictive maintenance: Digital twins facilitate failure prediction and maintenance planning, ensuring uninterrupted production.
- Cost optimization: More accurate process analysis enables better resource management, leading to the elimination of inefficiencies.
Why is high-quality data critical for building a digital twin?
High-quality data plays a pivotal role in the process of creating a digital twin, as it serves as the foundation for building an accurate model of the real-world object or process. Such data enables the development of digital models that faithfully replicate the behavior of machines, production lines, and systems. Outdated or inaccurate data can lead to flawed simulations, which negatively impact business operations, increasing the risk of costly downtimes and inefficient corrective actions. Therefore, high-quality data forms the cornerstone of an effective and reliable digital twin, making it the key factor for the success of implemented strategies in the real world.
Summary
The introduction of digital twins into the industrial sector opens up new opportunities for optimizing production processes. Digital twins, advanced IoT technologies, and data analytics are becoming the foundation of modern factories. These technologies enable failure prediction, quality improvement, and faster decision-making. Industry 4.0 and the development of digital twins are integral to the future of manufacturing, ensuring competitiveness and operational efficiency for companies.
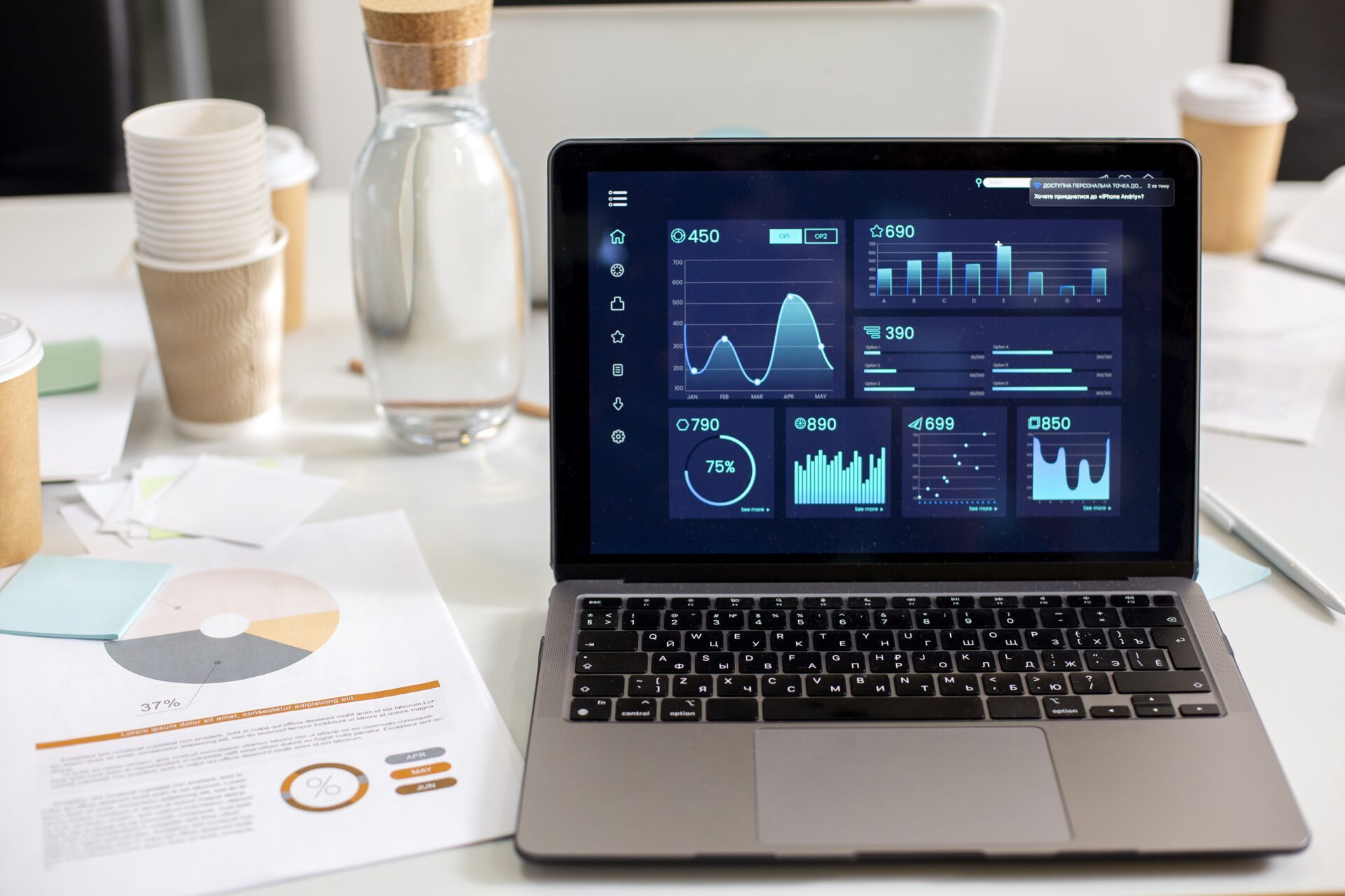
Has your company implemented a digital twin yet?
If not, contact us to learn how AIUT can support your business in the production digitization process and the implementation of digital twin technology.