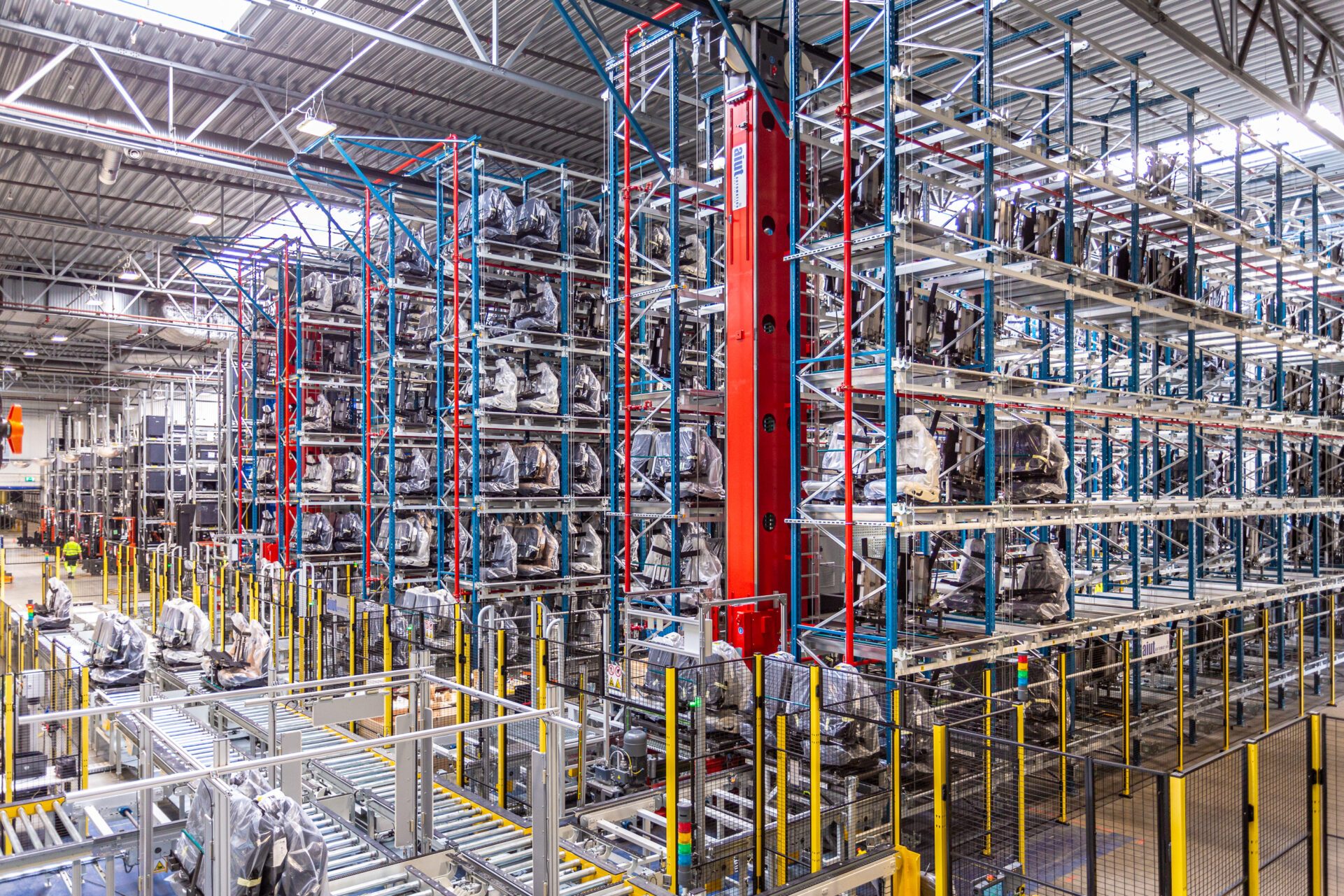
5 facts about warehouse automation solutions
In this article, you will learn:
-
what are warehouse automation solutions?
-
5 key facts about warehouse automation solutions.
-
what benefits do automated warehouse systems bring to businesses?
-
in which industries are warehouse automation solutions used?
In the era of Manufacturing 4.0, warehouse automation solutions have become not just a passing trend but a necessity. They are essential to meeting growing customer demands, increasing the efficiency of warehouse and production processes, and maintaining market competitiveness. The primary role of warehouse automation solutions is to streamline the internal transport of goods within a facility. Whether in logistics centers or manufacturing plants, this process requires automation to handle increasing orders while simultaneously reducing operational costs. Among the most common warehouse automation solutions are AGVs (Automated Guided Vehicles), AMRs (Autonomous Mobile Robots), conveyor systems, and stackers cranes, key elements of advanced logistics solutions, such as automated high-bay warehouses.
How do you know if investing in warehouse automation solutions is worth it? In this article, you will discover five key facts that will help you better understand what warehouse automation solutions are, how they work, what benefits they bring to businesses, and in which industries they are applied.
1. Autonomous mobile robots (AMRs) – a game-changer in warehouse logistics
Initially, internal transport relied primarily on forklifts operated manually by workers. However, technological advancements — especially those brought by the Fourth Industrial Revolution (Manufacturing 4.0) — have led to the growing adoption of more efficient and automated warehouse solutions. One of these solutions is autonomous mobile robots (AMRs), which have revolutionized automated goods transport while minimizing the need for human intervention. AMRs transport loads of various sizes and weights in any industrial environment. They handle repetitive and hazardous tasks, improving worker safety and allowing employees to focus on more complex, knowledge-intensive tasks. Equipped with advanced sensors and mapping technologies, AMRs scan and update their surroundings in real-time, dynamically adapting to changes in warehouse layout. These robots can stop at precise locations to avoid collisions with other vehicles. Unlike AGVs (Automated Guided Vehicles), AMRs do not require predefined infrastructure to move along designated routes. If you want to learn more about the differences between AMRs and AGVs, check out our article: “AGV or AMR robots? Key to the factory’s success“.
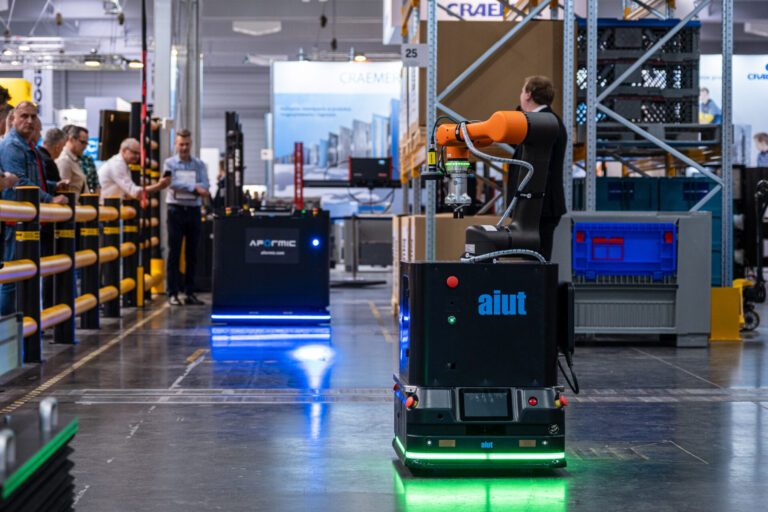
Autonomous mobile robots – benefits of implementing automation
- reduced operational costs – lower demand for manual labor and minimized human errors
- high scalability – ability to dynamically adjust the number of robots to the company's current needs without costly infrastructure changes
- improved warehouse process safety – advanced collision avoidance systems and sensors significantly reduce the risk of accidents
- high flexibility – AMRs adapt their routes to warehouse layout changes, navigate around obstacles, and dynamically respond to new conditions
- integration with WMS and ERP systems – automated material flow management and optimization of logistics processes
- handling diverse loads – capability to transport goods of various sizes and weights in any industrial environment
- enhanced service quality – smoother warehouse logistics enable better inventory management and on-time order fulfillment
Revolutionize intralogistics with AFORMIC
Aformic is a sister company of AIUT – a global system integrator specializing in factory automation, robotics, intralogistics, process control, and digitalization. The company provides comprehensive intralogistics solutions, offering both a fleet management platform and the intelligent AMRs F-series. Our solution ensures full adaptation of AMRs to customer-specific processes, enabling the transport of loads of various sizes and weights in any industrial environment.
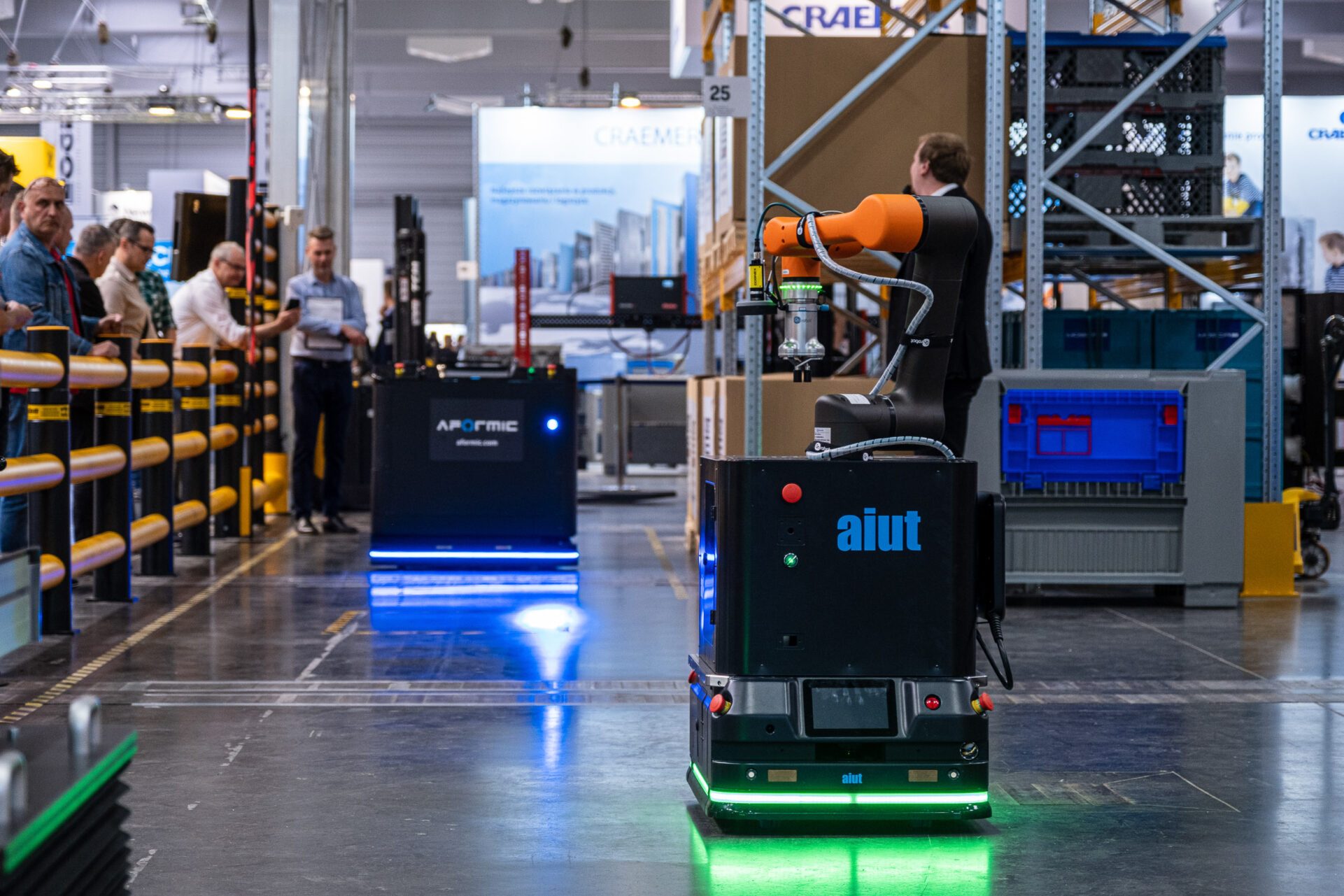
2. Warehouse automated solutions go beyond AMRs and AGVs – implementing automation with conveyor systems
While AGVs and AMRs dominate internal transport automation, conveyor systems also play a crucial role. Like other warehouse automation solutions, conveyors streamline the movement of goods, ranging from heavy to lightweight products. They automate warehouse receiving and dispatch areas and are particularly useful in facilities with limited space or those requiring automated product sorting. Implementing a comprehensive conveyor system optimizes the entire order fulfillment process, significantly boosting warehouse operational efficiency. Warehouse automation solutions such as conveyors eliminate manual handling and reduce the risk of product damage during transit.
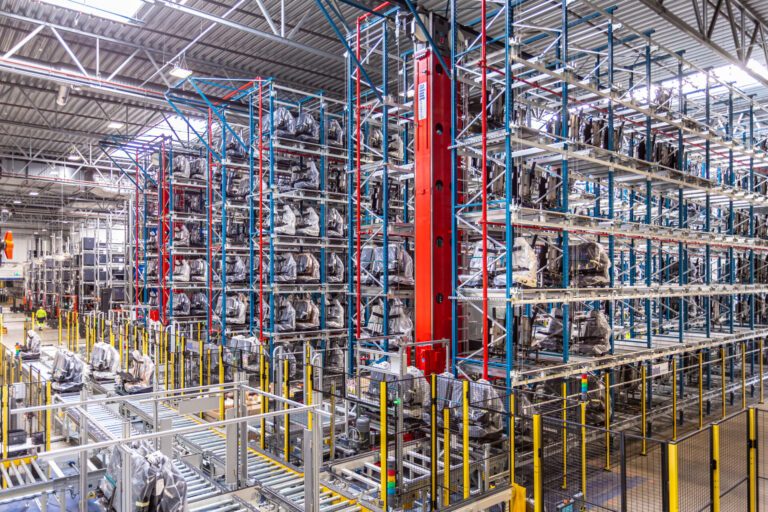
There are different types of conveyors available on the market, including:
- Roller conveyors
- Chain conveyors
- Belt conveyors
- Modular conveyors
Read the article “Conveyor systems: The key to efficient internal transportation“ to find out which conveyor solutions best fit your logistics needs!
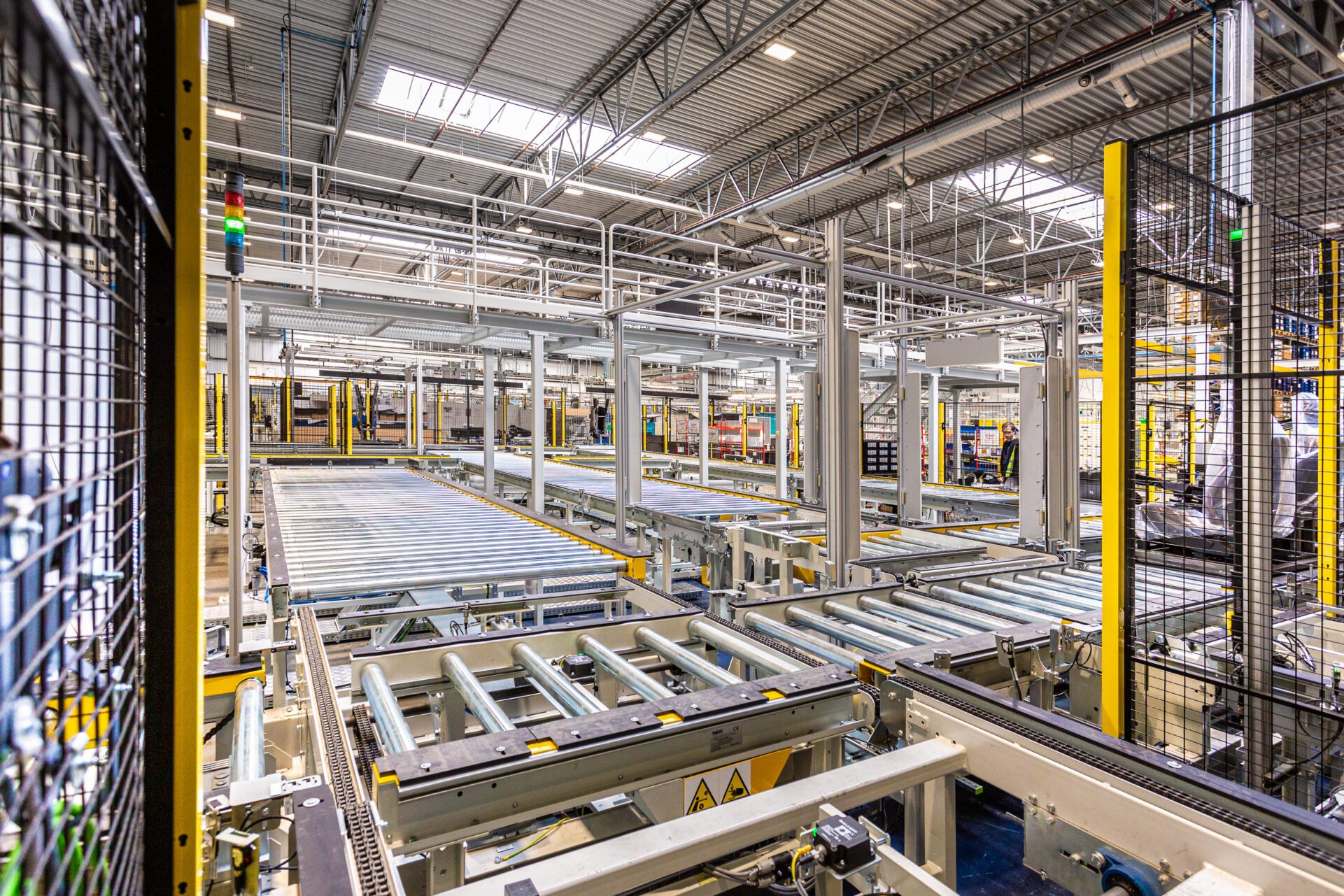
3. Automated solutions improve warehouse operational efficiency
Automating material transport ensures smooth and precise delivery of raw materials, components, and finished products, eliminating delays and minimizing human errors. As a result, companies can operate more efficiently, quickly, and reliably. The efficiency of warehouse automation solutions is measured by their throughput, meaning the number of completed orders or shipped parcels per hour. Warehouse automation solutions optimize goods flow and help businesses meet market demand standards, ensuring stable and uninterrupted operations. Another advantage is the growing integration capability of warehouse automation solutions with other logistics systems, allowing for seamless management and synchronization of warehouse operations. This enables businesses to optimize processes, increase competitiveness, and enhance operational efficiency.
4. Greater transparency through integration with other warehouse systems
Integrating warehouse automation solutions with production lines allows for precise material deliveries from warehouses according to order schedules, minimizing the risk of downtime and optimizing the flow of raw materials. For businesses, this is a cost-effective and comprehensive solution that improves logistics while eliminating risks related to labor shortages or supply delays. Additionally, integrating warehouse automation solutions with ERP, WMS, or MES systems increases warehouse process transparency through real-time data collection and analysis. This facilitates effective inventory monitoring, performance analysis, and faster operational decision-making. In the Manufacturing 4.0 era, internal transport automation and its seamless integration with warehouse management systems are crucial steps toward smart intralogistics. Fully integrated warehouse automation solutions shorten order fulfillment cycles, ensure continuous supply flow, and enhance customer satisfaction.
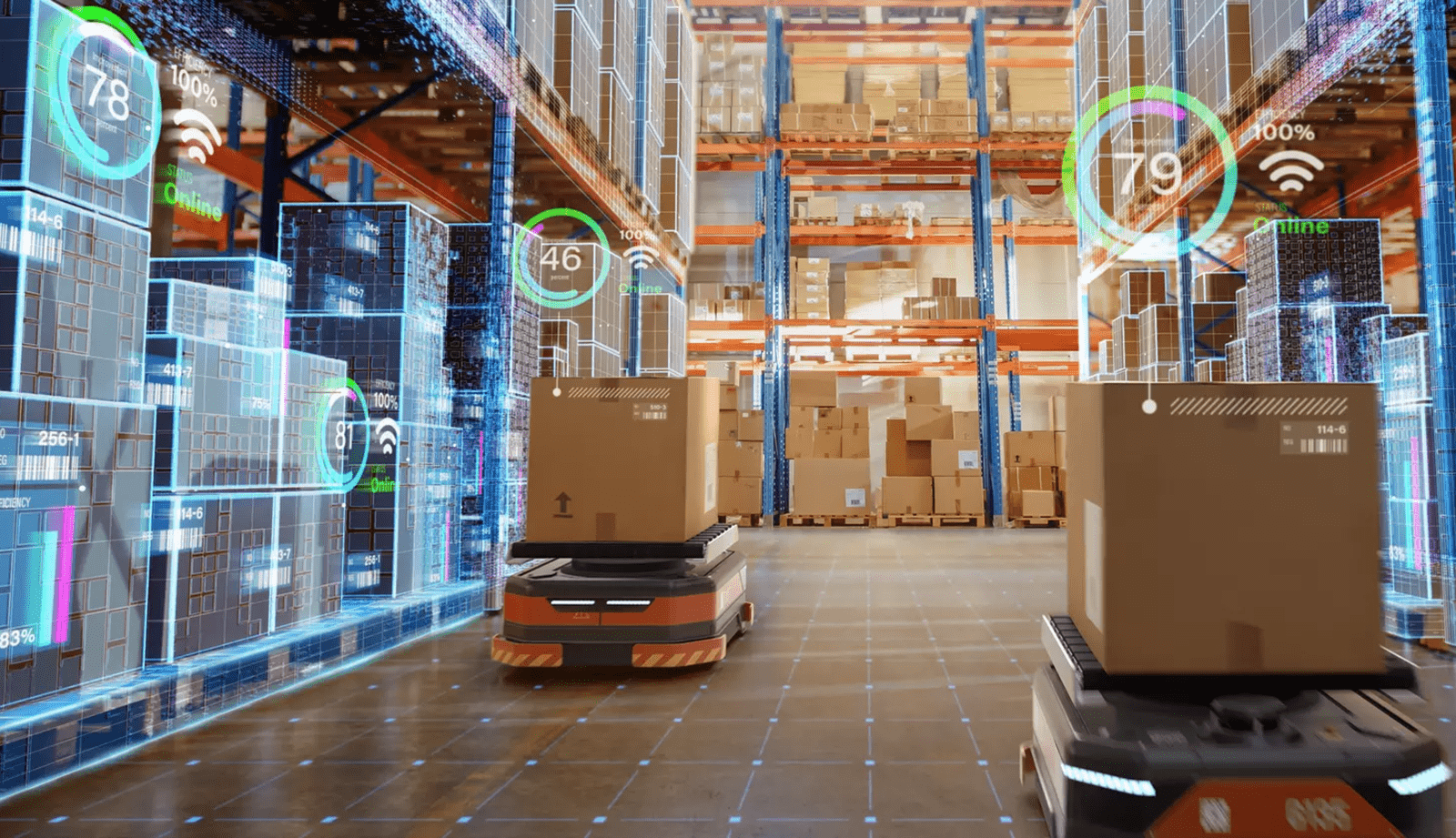
5. Warehouse automation technology for every industry
Warehouse automation solutions are used in a wide range of sectors — from automotive, food, and pharmaceuticals to e-commerce. Thanks to high configurability, they can be adapted to the specific needs of each industry, making them extremely versatile solutions. Logistics centers, warehouses with high product turnover, and facilities requiring fast transport increasingly invest in automated storage systems to optimize processes and enhance operational efficiency. For example, the food and FMCG industries rely on fast and precise goods movement to maintain supply chain continuity. Similarly, the automotive industry — one of the most technologically advanced sectors — leads in adopting modern technologies. It continuously invests in robotics and intelligent transport systems, enabling better material flow control and supply chain optimization.
So, are warehouse automated solutions a trend or a necessity?
The benefits outlined in these five key facts speak for themselves — higher production efficiency, faster order processing, lower operational costs, and optimized warehouse operations are hard to ignore. While many companies strive to automate warehouse processes, some hesitate due to high initial investment costs. However, in the long run, warehouse automated solutions provide a solid return on investment, reducing human errors, improving goods flow, and boosting competitiveness. For forward-thinking companies, warehouse automated solutions are not just a trend but a strategic necessity.
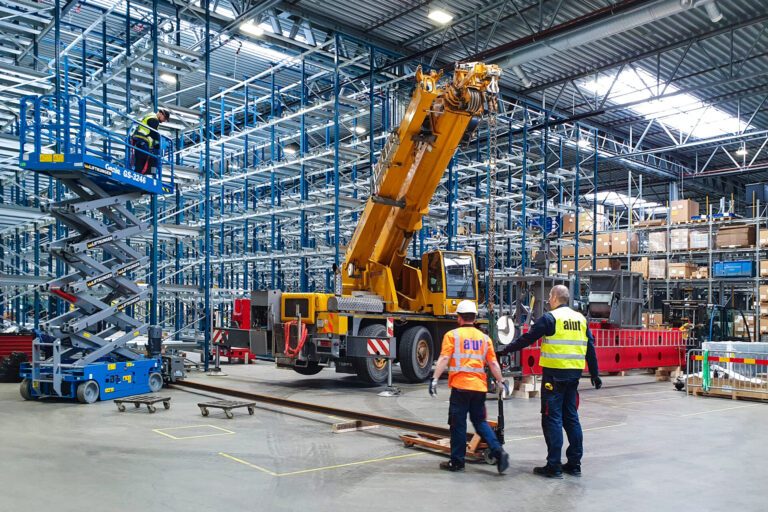
Intralogistics with AIUT
AIUT implements automation solutions in industrial plants, warehouses, and distribution centers. We equip our clients with solutions such as: automated storage systems, conveyor lines, automated pallet and container transporters, and robotic transport solutions, including the AFORMIC intralogistics system. We cater to various industry needs regarding warehouse automation solutions. For our client in Poland, we implemented a transport line that, using an overhead conveyor system, connected the production hall with the warehouse. The designed line includes low conveyors with a centering system, pallet lifts for vertical pallet transport, and standard roller conveyors. It is used for transporting two types of high pallets and features a bidirectional operation mode.
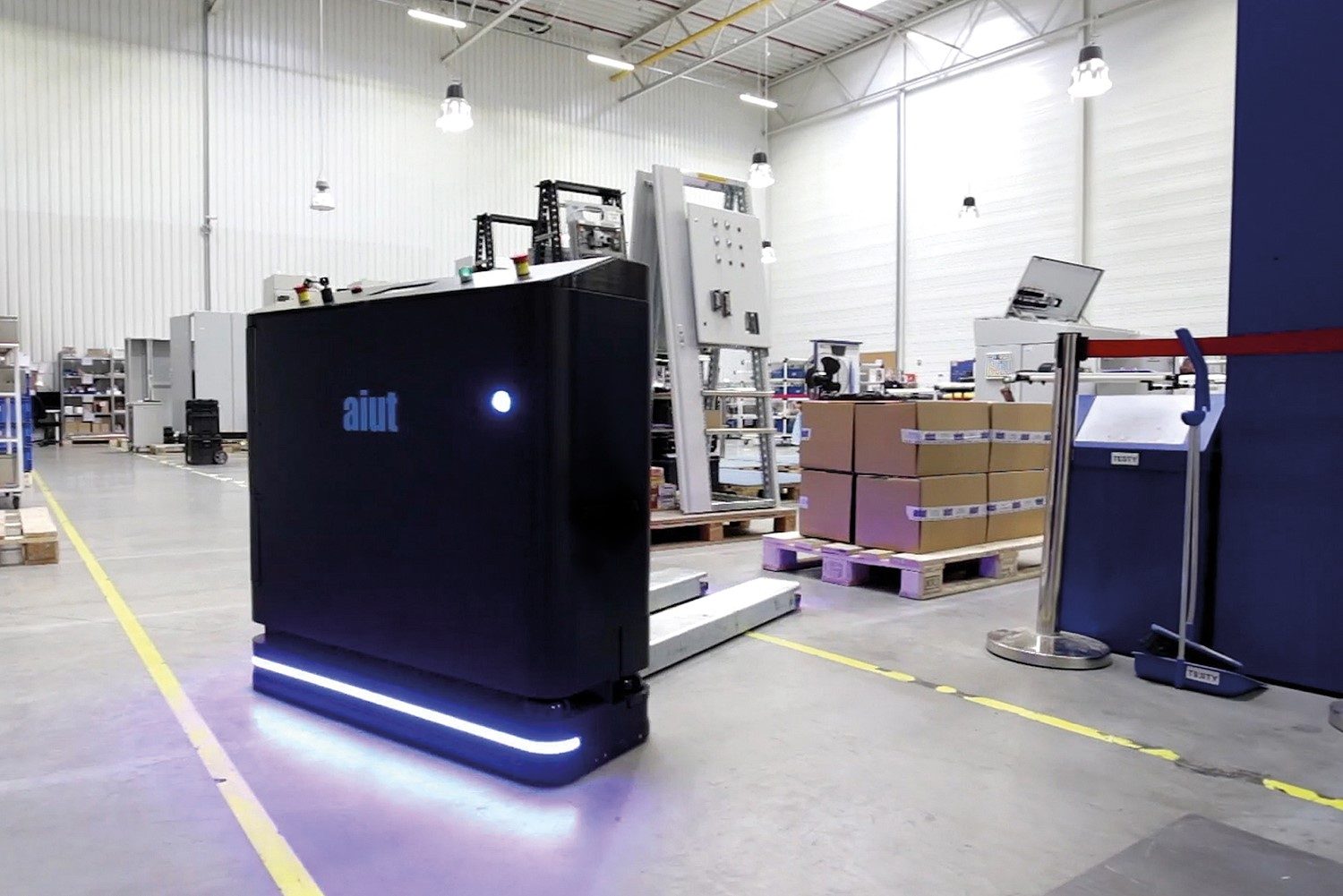