
AGV or AMR robots? Key to the factory’s success
From this article, you will learn:
-
when and where the first industrial mobile robots were created.
-
what are the differences between automatically guided vehicles (AGV) and autonomous mobile robots (AMR)?
-
how do AGVs and AMRs work?
-
what does the market for AGV and AMR robots look like?
-
where are warehouse robots used?
-
what are the benefits of implementing AGV and AMR robots in factories?
In the era of Industry 4.0, warehouse automation solutions play a crucial role in increasing operational efficiency in manufacturing plants and warehouses. Among innovative automation solutions are AMR (Autonomous Mobile Robots) and AGV (Automated Guided Vehicles). These two technologies revolutionize the way goods are moved and managed in industrial facilities. The choice between them depends on specific needs and the conditions of a given work environment, as these solutions differ in control method, program execution, size, and payload capacity. In this article, we will take a closer look at the characteristics of AGV and AMR robots, where they find applications, and what benefits they bring.
Automated mobile robots — historical overview
AGV robots first appeared in the 1950s, specifically in 1953 in the United States. The visionary behind them was Arthur Mac Barrett, who led the Barrett Electronics company, based in Northbrook, Illinois. These pioneering mobile transport robots, referred to by the inventor as vehicles without a steering wheel, followed a signal transmitted through wires embedded in the floor.
In Europe, the beginnings of self-propelled machines date back to 1956 when the EMI company from England developed a vehicle moving along a colored tape attached to the floor. Path recognition was made possible in this case through an optical sensor. In the subsequent years of the 20th century, AGV robots evolved and found increasingly broader applications. An example of this trend is the Swedish company Volvo, which, during that time, began transporting car bodies between workstations in the Kalmar factory using as many as 186 machines.
A somewhat later invention are the AMR robots in healthcare, which began to appear on the market in the 1990s. The first of them was HelpMate, released by the company Transitions Research Corporation. Its purpose was to transport items in hospitals, such as meal trays, medical supplies, test results, or mail. Ongoing technological progress led to the development of natural navigation systems, enabling the continued dynamic growth of AMR robots.
AGV vs. AMR? — key differences between automatically guided vehicles and autonomous mobile robots
Structure and payload of automated transport vehicles
AMR robots have a compact structure, making them much more maneuverable than, for example, a manually operated forklift. Moreover, they can easily fit into spaces inaccessible to most vehicles — including AGV, such as under a pallet. The shape of the AMR robot and the vehicle's wide payload range are key features that meet the facility's needs. For instance, AIUT's AMR (called AMR Formica) can transport loads ranging from 800 kg to 2 tons (depending on the model). Such a wide range of lifting capacity is possible thanks to the full customization of the solution and the vehicles themselves.
Path planning and movement
AGV vehicles move along predefined paths marked by magnetic, optical, or other floor-based signs. Therefore, AGV navigation systems work best in fixed, repetitive processes, such as transporting pallets along a designated route. In contrast, AMR does not require predetermined paths as they navigate freely in their environment, utilizing technologies like laser navigation supported by Simultaneous Localization and Mapping (SLAM) or machine vision-based algorithms. AMR robots excel in dynamic environments where variables, like the movement of other resources in a factory, are present. Although the methods of movement differ between AGV and AMR, both require a smooth surface without significant inclines or gaps.
Programmability
As mentioned earlier, AGV moves along fixed paths, executing specific tasks programmed in advance. Changing the route for AGV can be challenging, involving the expansion of magnetic strips in new sections of the track or even the need to reconfigure layouts in the production or warehouse facility. Conversely, AMR robots are flexible in choosing their path, adapting to changing environmental conditions and easily adjusting to new tasks. If the goal is to have a robot perform a variety of tasks, especially different ones for each shift, an easily programmable AMR robot is a better solution.
Implementation, deploying mobile robots in factories
Implementing an AGV system requires larger initial financial investments due to the need to install the appropriate infrastructure, such as magnetic and optical tapes, and set up reflectors or locators on designated routes. In the case of AMR devices, there is a seamless installation with lower costs. This is because it is sufficient for an AMR robot to move around the designated area and create a map of the space.
Navigation of AGV/AMR, mobile robot technology for path planning
AGV uses specific markers or previously marked navigation lines and additional characteristic points for movement. In contrast, AMR navigates relying on advanced technologies such as camera systems, laser sensors, and scanners. Using these technologies, AMR robots understand their surroundings and create a map of the terrain, autonomously choosing the optimal route to reach the designated destination. Unlike AGV, AMR does not require advanced external infrastructure. However, ensuring the visibility of fixed elements in the factory, such as pillars or walls, is essential for AMR to use them as locational anchors and facilitate accurate spatial orientation.
Flexibility and responsiveness of mobile transport robots
AGV robots are ideal for tasks with fixed destination points. Their responsiveness is limited, meaning that if they encounter an obstacle, the robot stops and waits until it is removed. Meanwhile, AMR can automatically avoid obstacles (if possible) and designate an alternative path to reach the predefined destination. Additionally, if an AMR encounters an object on its path, it stops due to collision avoidance capabilities resulting in embedded safety systems.
Scalability
AGV mobile robots are less flexible in terms of easy system expansion, while AMR devices are more scalable, allowing for the easy addition of more units to the system. For example, Qursor, an advanced fleet management system from Aformic, enables simultaneous control of multiple robots. It also allows for cargo transport—handling up to 500 tasks using over 20 mobile robots fleet in just 8 hours. This operating method easily adapts to process efficiency needs. Furthermore, the seamless integration of warehouse execution software (e.g., WMS or MES) with AMR robots from Formica makes them an integral part of the production process.
Mobile robots market
Automatically Guided Vehicles — AGV
According to the “Global AGV market volume by region 2019” report by Statista Research Department, there were over 138,700 units of Automated Guided Vehicles (AGV) worldwide in 2019, and it is projected to exceed 272,700 by 2025.
As per the report from MarkertsandMarkets, the AGV market is estimated to have reached a value of $2.4 billion in 2023. Their forecasts indicate that by 2028, it will reach a value of $3.3 billion. The growth drivers mentioned in the report include the demand for automation in factories and warehouses, increasing safety levels, production flexibility, and adapting to market needs, such as moving away from mass production in favor of customized solutions.
Autonomous Mobile Robots — AMR in numbers
Despite the strong and established presence of Automated Guided Vehicles (AGV) in manufacturing plants, their role is gradually being taken over by AMR carts. It is estimated that autonomous mobile robots (AMR) will constitute 80% of industrial robots by 2027, and their number in factories is expected to reach 15 million by 2030. According to research by The Insight Partners, the market value of AMR robots in five key regions: North America (NAM), Europe, Asia-Pacific (APAC), the Middle East and Africa (MEA), and South America (SCAM) is as follows (see the chart below). It is also estimated that the AMR robot market could reach $8.7 billion by 2030.
AGV and AMR applications
AGV and AMR robots revolutionize the functioning of factories, setting new standards for efficiency and flexibility in internal transport and material management. They find applications in material handling and distribution operations within factories. These include product transportation on the production line, moving and delivering pallets, and packages, transferring raw materials, semi-finished products, and finished goods between different production stations, storing finished products in warehouses, and optimizing space. There are many types and applications of AMR and AGV robots, each equipped differently (e.g., with grippers, platforms, forks, robotic arms, etc.), making them better suited for specific tasks in order fulfillment operations.
Both AGV and AMR find applications in almost every industry. Research indicates that in 2022, the most common industries that used AMR robots were logistics (31%), automotive (16%), and FMCG (16%).
The main advantages of implementing AMR robots and AGV
- Improve the efficiency of material handling
- Increased performance in warehouse operations
- Minimization of human errors, increasing safety standard
- Relief of workers from monotonous and physically demanding tasks
- Reduction of transportation and internal logistics costs
- Assurance of reliability and repeatability in manufacturing and order fulfillment operations
- Improvement of safety and reduction of damages caused by collisions and accidents
- Ensuring flexibility and scalability
- Ongoing support, maintenance of plant operations 24/7
Comment from our expert
— In industrial solutions, AGV and AMR robots are implemented to increase operational efficiency and relieve technical staff from performing repetitive tasks in internal logistics. Their use can enhance the reliability and repeatability of manufacturing and warehouse processes, and improve workplace safety and logistics operations, as well as ergonomics. Finally, AGV and AMR robots can become an integral part of the production process, serving as carriers for the manufactured product or interacting directly with plant automation systems and information systems. Such utilization of mobile robots allows for the creation of flexible scenarios in production execution, thus streamlining both manufacturing and its handling. — Marek Drewniak, Head of the Research and Development Section in the Automation Department at AIUT.
See the entire discussion on AGV and AMR mobile robots and all expert statements here.
For more information about AIUT's AMR, you can visit www.aformic.com.
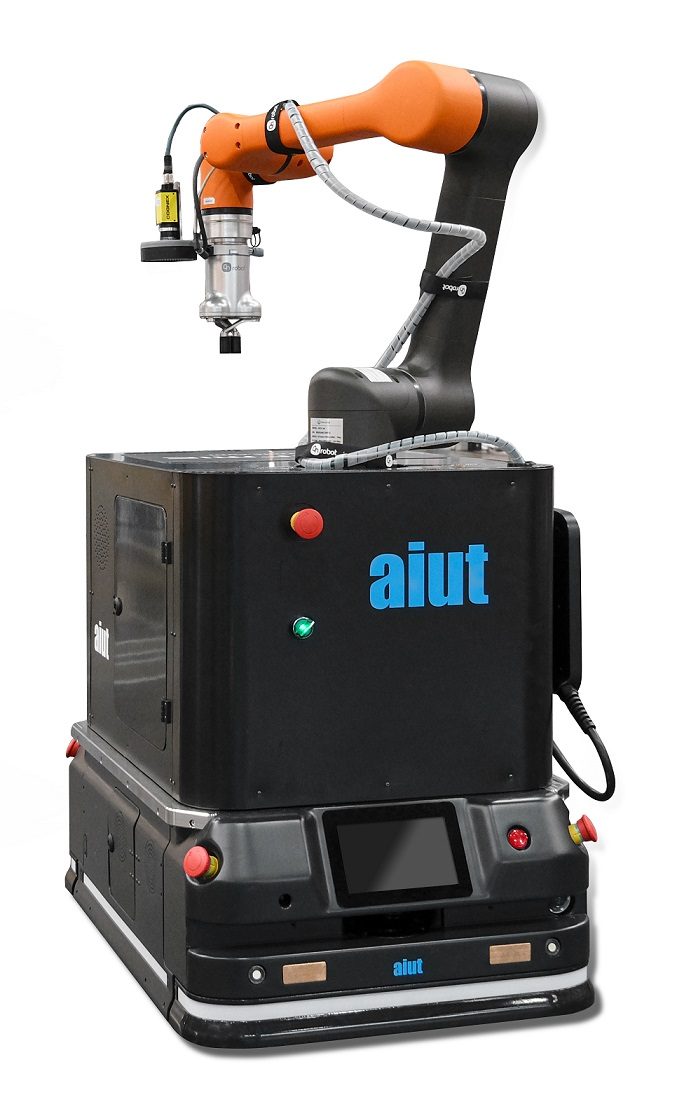
Summary
Warehouse automation solutions such as AGV and AMR enhance intralogistics efficiency. When making a choice, factors such as local conditions in the production hall, the allocated budget covering installation and operational costs, and the types of tasks we want these robots to handle should be taken into consideration. To maximize throughput efficiency, it is beneficial to combine the advantages of both AGV and AMR.

We can tailor AGV and AMR robots to the needs of your facility.
As an integrator of industrial automation and warehouse robotics solutions, we have over 30 years of experience in customizing automation solutions to meet the specific needs of our clients. Become the best player in the mobile robot industry with us!