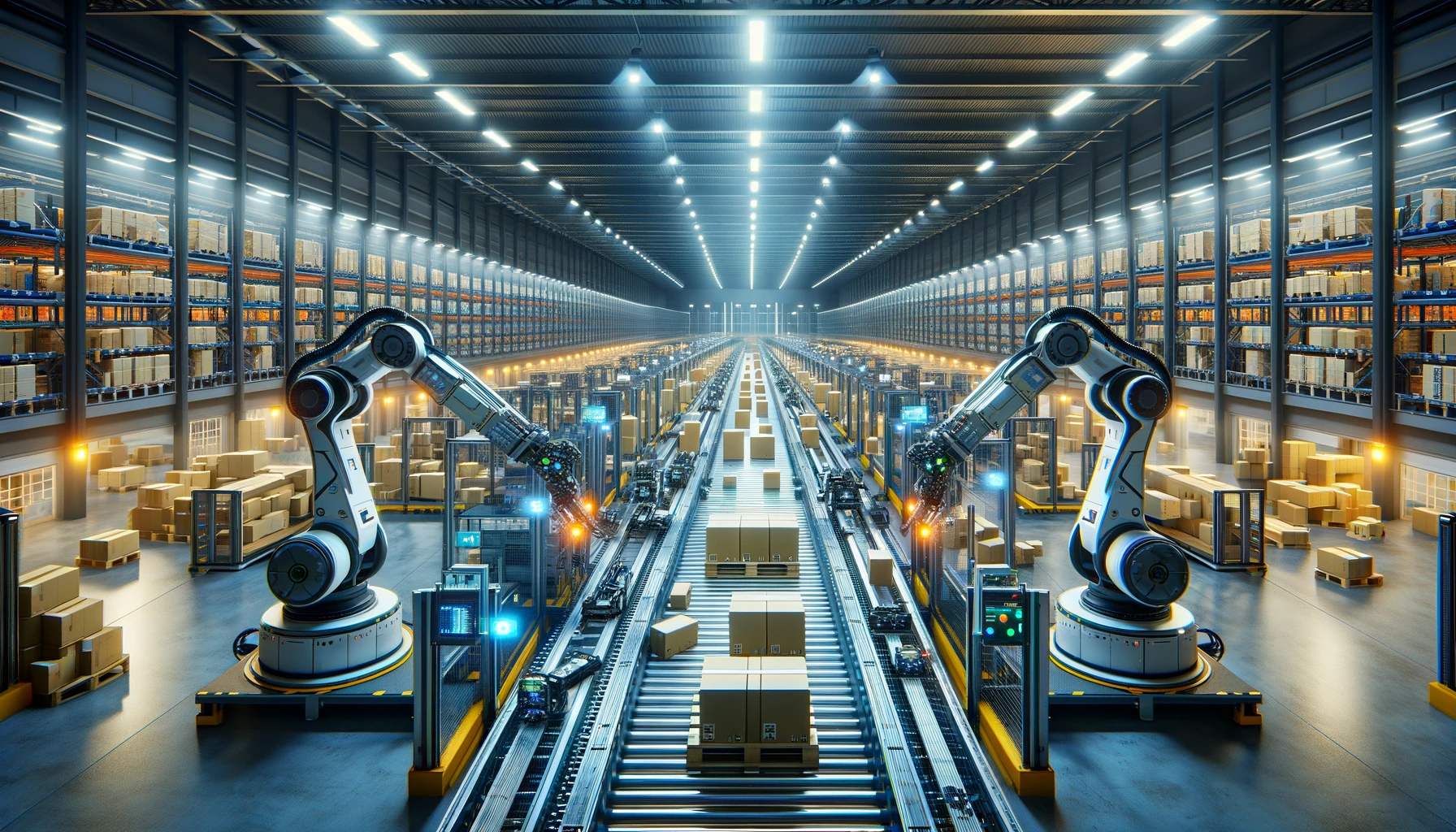
Automated Palletizing — Boost efficiency with robots
In this article, you will learn:
In the era of automation and robotization of processes, traditional methods are giving way to more advanced and flexible solutions. Palletizing automation using industrial robots is one example of such innovation, offering not only increased efficiency and precision but also improved safety in manufacturing plants. Although palletizing robots are not a new concept, there is currently a growing demand for increasingly intelligent systems that can analyze a product's weight, size, and susceptibility to crushing before palletizing items. Another challenge is integrating these palletizing systems with other warehouse information systems — MES (Manufacturing Execution Systems) or WMS (Warehouse Management Systems).
This article will discuss current trends in the warehouse automation market, and highlight the benefits of industrial palletizing automation. Also, it will point out key aspects to consider when choosing an industrial palletizing robot and show how to properly prepare these systems for efficient operations.
Palletizing solutions in the warehouse automation market
According to the report “Warehouse Automation Market: Forecast To 2026” conducted by LogisticsIQ Research, the warehouse automation market is expected to nearly double with a CAGR of 13.7% between 2019-2026. Its size in 2019 was $15.5 million, and it is forecasted to reach $30.329 million in 2026, as shown in the chart below.
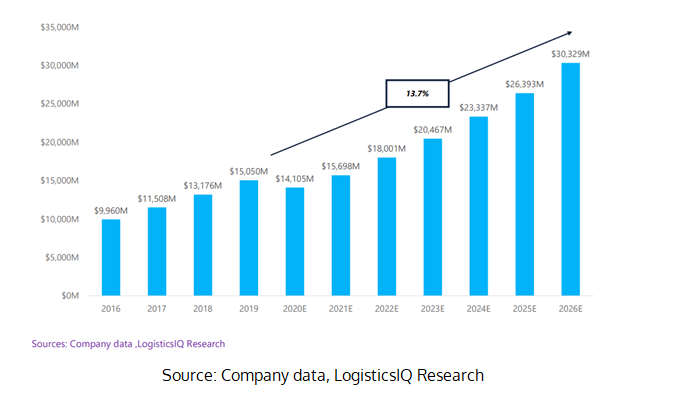
Analyzing the individual technologies that contribute to the value of the warehouse automation market, the chart below shows that in 2019, palletizing and depalletizing systems reached a value of $11.71 million. It is forecasted that in 2026, they will reach $17.56 million.
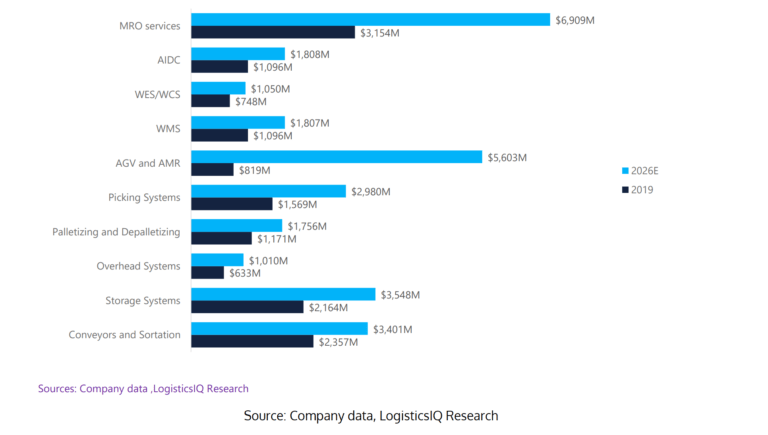
Definition of palletizing operations
The palletizing process is a key operation in logistics and supply chain management, involving the arrangement of goods in line with a selected pallet pattern for their transportation, storage, or shipment. Pallets prepared in this manner can be moved along with the entire load using near-transport devices such as forklifts or autonomous mobile robots. For effective transport and storage, the choice of the right pallet types is crucial. Those available on the market vary not only in the material they are made of – wood, plastic, or metal – but also in size. The most popular pallets include Euro-pallets and American pallets. Factors influencing the choice of pallet types include warehouse storage and retrieval systems, material handling automated systems, the type of products to be stored (to meet e.g., pallet loads and product dimensions), or requirements, and conditions imposed by suppliers.
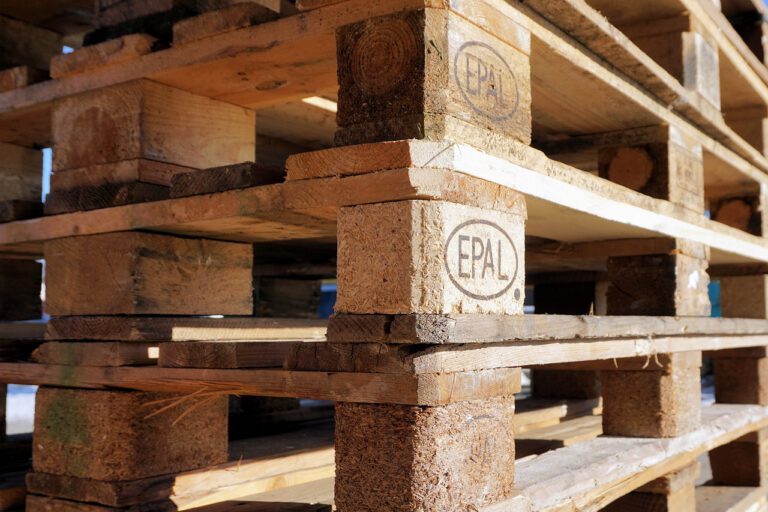
Automated palletizing vs. manual palletizing items
The palletizing process can be carried out manually by workers or automatically with the use of specialized palletizing robots. Manual palletizing items requires the physical stack and distribution of products on a pallet by an operator, making it time-consuming and less efficient, especially in the case of large production volumes. Robotic palletizing allows for fast, precise, and continuous arrangement of products, resulting in increased efficiency, reduced operational costs, and relieving physical workers from, for example, moving heavy loads.
Check out what we can do for you in terms of automation and robotization of production processes.
The benefits that industrial palletizing automation provides with industrial robots
- Increased palletizing process efficiency thanks to robots that work 24/7
- Greater precision in pallet arrangement and secure product handling
- Reduced risk of accidents and injuries among workers
- Shortened palletizing process time
- The universality of the palletizing process across different industries and applications thanks to the flexibility in adapting robots for various tasks and pallets
- Cost savings through reduced labor costs
- Elimination of human errors
- Quick return on investment
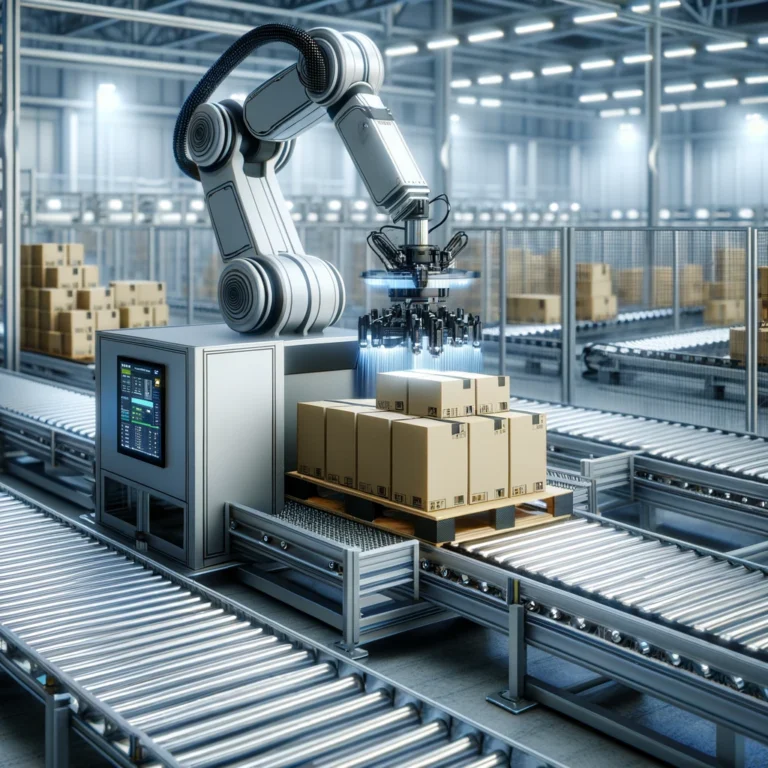
How to automate palletizing? — aspects and technical parameters to consider before investing in robotic palletizing systems
In the process of selecting a modern palletizing solution, remember that we are not evaluating a single industrial robot, but must take a comprehensive look at the robotic stations. Using palletizing robots will bring us a series of benefits, provided that we consider the appropriate aspects and technical parameters presented below.
Production cycle time
One of the most important parameters that will tell us, in reality, how many palletizing robots are needed in our process. If it turns out to be short, it may be a sign that one of them is not able to perform all the tasks in the required time. Additionally, the robot's reach should be taken into account, which is crucial when designing an inline palletizing intended to handle a specific segment of the production process. Other aspects to consider when choosing a palletizing robot include the speed of performing load arrangement operations and its accuracy.
Compatibility of palletization stations with products
Another significant aspect is planning which products the palletizing robot will pick up from the production line. The product dimensions and their weight are critical here. The market designs both robots that are dedicated to handling diverse products and those that can handle palletizing only one specific product. Therefore, it is worth paying attention to production variability and the robot's universality, i.e., the ability to work with various types of loads and packaging. Also, the way products are arranged should be evaluated. Whether products will be placed on pallets, in containers, or perhaps on an autonomous mobile robot AMR/AGV, which will streamline the further flow of goods within the production plant or warehouse.
Load capacity and lifting capacity
Load capacity is the maximum weight the robot can handle. This is a key technical parameter, as the size and weight of products determine the choice of robot and tools, such as the appropriate type of gripper in a robotic arm.
System Integration: palletizing software with existing information systems
Choosing the right palletizing robot and its integration with existing production and logistic systems is a key factor in ensuring smooth and efficient operation at the end of the production line. The palletizing robot must not only be matched to the technical specifications and operational requirements of a given plant but also compatible with production management systems (MES), warehouse management systems (WMS), and other automation tools. Integrating the robot with production and warehouse management systems allows for automatic planning of palletization tasks, monitoring work progress in real-time, and efficient material flow management. This can significantly reduce downtime, increase production throughput, and improve the overall accuracy and quality of logistic processes.
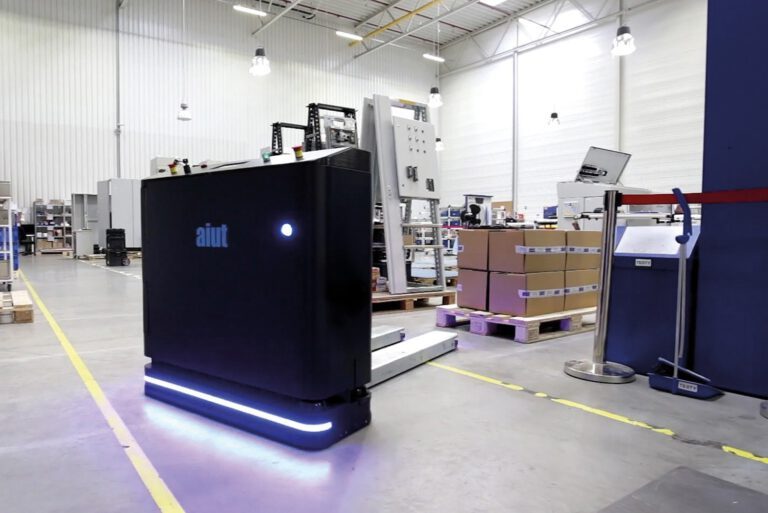
Summary
The use of palletizing robots is an investment towards the automation and optimization of processes, offering companies increased efficiency, precision, and operational safety. It is also a strategic business decision that brings long-term benefits and a quick return on investment. However, it is important to remember that the appropriate selection and preparation of the palletizing robot is key to success, hence the need for cooperation with a trusted technological partner, and as we know — comprehensively only with an integrator.
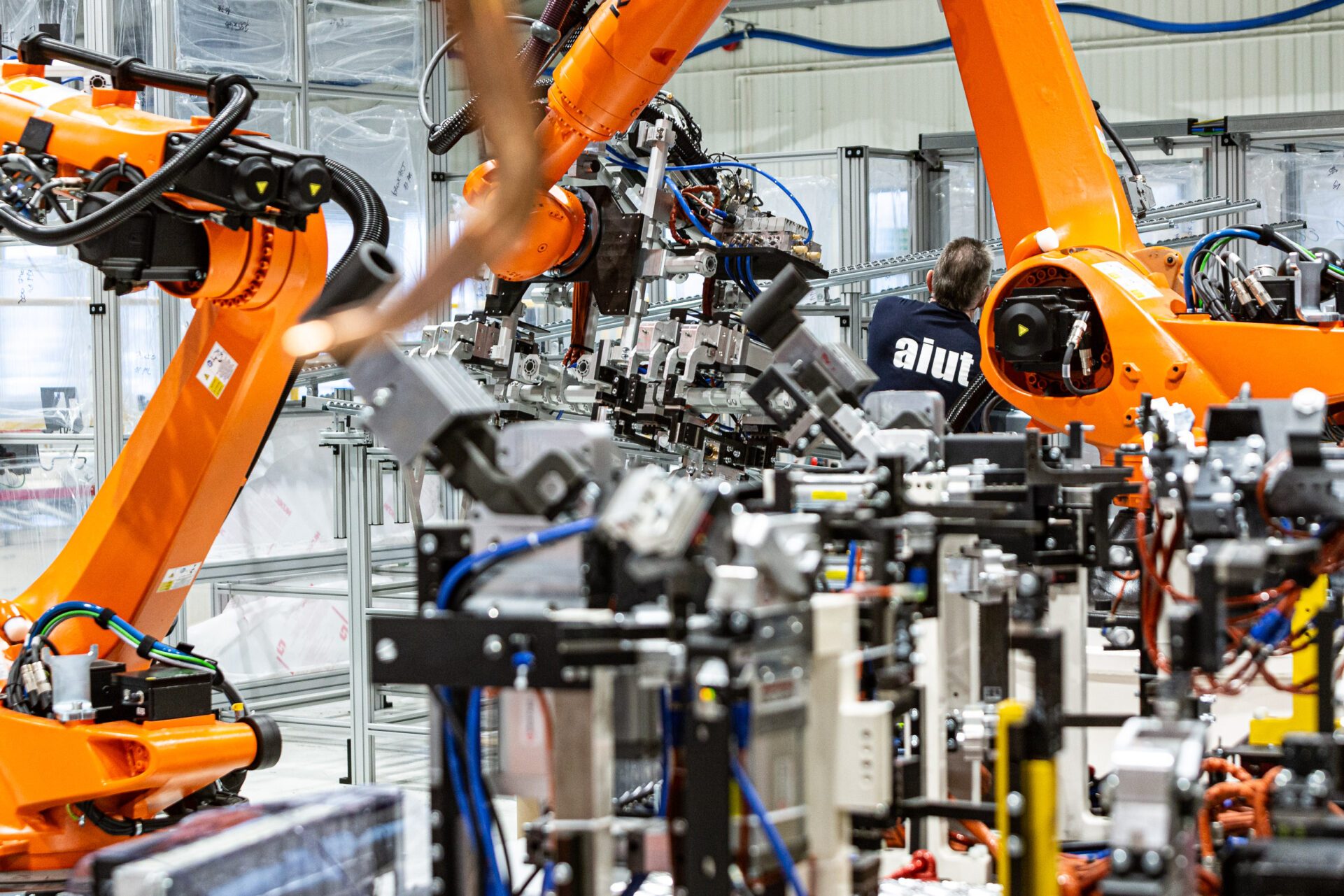
Are you looking for an experienced partner to implement robotic palletizing systems? Contact us!
As an integrator in the field of automation and industrial robotics, we specialize in designing palletizing automation, and other robotic workstations and production lines. We implement palletizing solutions as well as storage and retrieval systems for material handling.