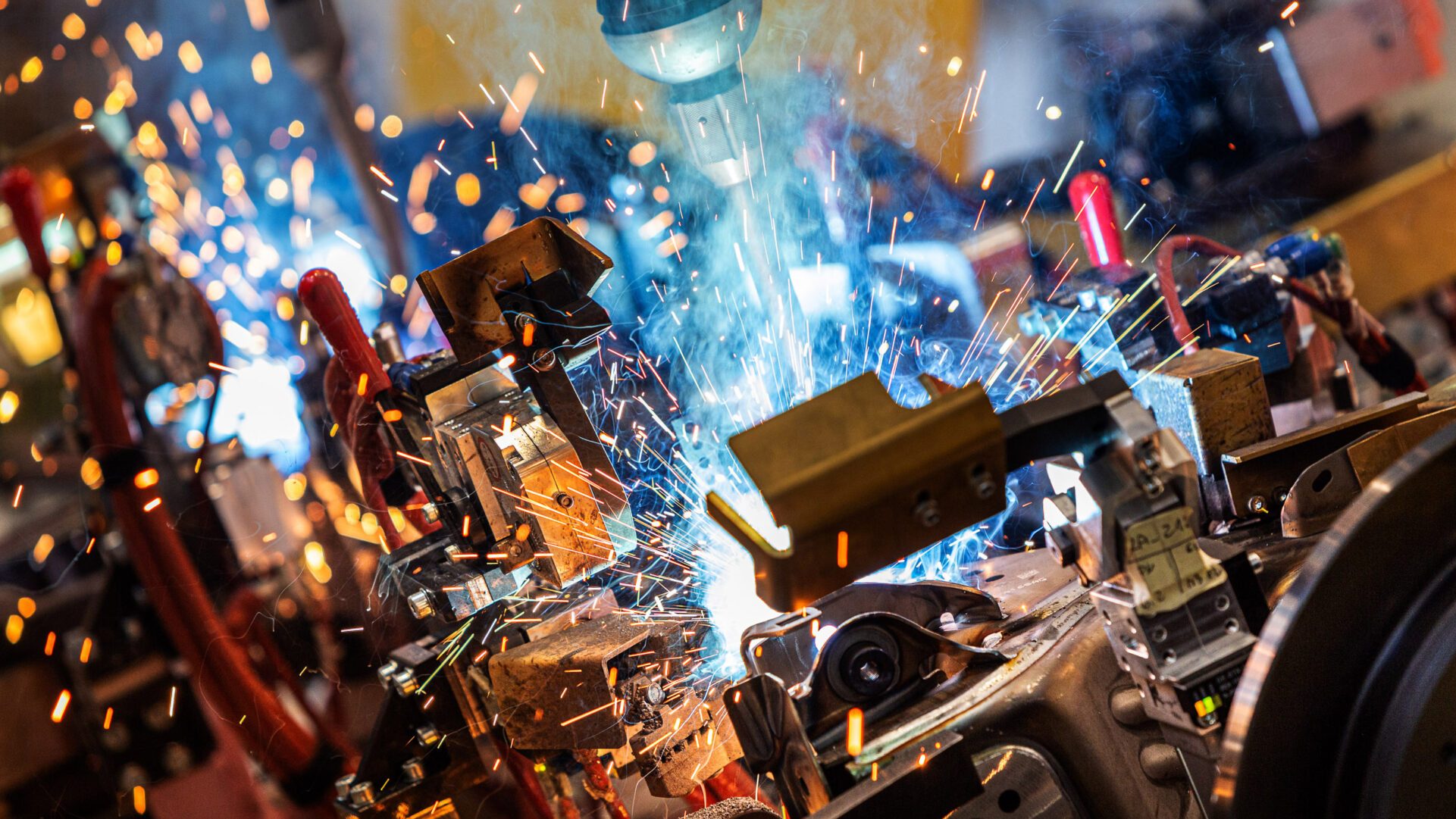
The next welding master? An industrial robotic cell
From this article, you will learn:
-
what does the market for robotic welding look like?
-
what is a robotic cell?
-
what do robotic work cells provide to a manufacturing facility?
-
what are robotic work cell benefits?
-
about the technologies used in robotic welding cells.
-
what robotic integration services with autonomous mobile robots are available?
In today's industrial world, modern Manufacturing 4.0 technologies play a fundamental role, enabling automation and robotization of production processes with minimal or negligible human intervention. The range of benefits they provide, along with the growing need for improving production processes, compel enterprises to seek innovative solutions that will ensure their competitiveness in the market.
One such solution is a robotic cell utilized in industrial processes such as welding. Their primary task is to increase process efficiency, provide greater flexibility, and ensure the highest possible quality of manufactured products while simultaneously optimizing costs.
Originally, robotic welding stations were adopted in the automotive industry to overcome the shortage of skilled labor for manual welding applications. Currently, these and other robot workstations are gaining popularity in numerous manufacturing sectors, including electrical, electronic, metal, machinery, aerospace, defense, construction, and pharmaceutical industries.
In this article, we will examine the market for robotic welding, what robotic cells are, what benefits they bring to enterprises, why it's worth investing in them, and what the latest robotic welding technologies are used in robotic manufacturing.
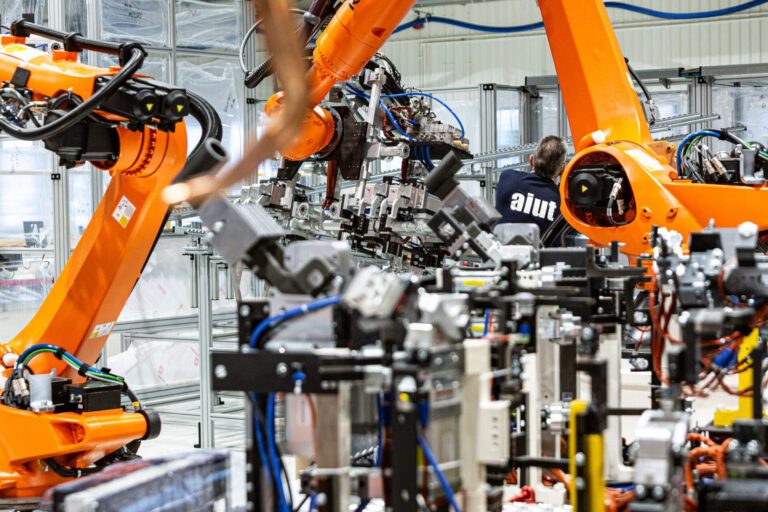
Welding market in the robotic industry
According to a report by MarketsandMarkets, the global robotic welding market in terms of revenue was estimated at $7.1 billion in 2021. It is projected to reach $11.7 billion by 2026, with a compound annual growth rate (CAGR) of 10.5% (see chart below).
The driving factors behind the growth of this market, as presented in the report, include Manufacturing 4.0, which signifies increasing awareness among companies regarding the implementation of innovative solutions in this area. Additionally, growing demand for efficient welding robots in the automotive and transportation industries, and government initiatives aimed at supporting the digital transformation of enterprises.
What are robotic work cells?
A robotic cell, also known as a robotic station, is an enclosed work area where an industrial robot, along with necessary auxiliary tools, performs assigned tasks. These advanced systems respond to the need for automation and robotization of manual workstations, where there is a lack of skilled workers, such as welders. Integrating industrial robots into production processes relieves workers of tedious, repetitive tasks requiring big precision, ensuring high, repeatable quality of the manufacturing process. Robotic cells are used in various production processes, for example as robotic welding cells, robotic packaging cells, robotic palletizing cells, robotic assembly cells, or robotic sorting cells, replacing the need for manual execution of these processes. They are designed in accordance with machinery directives and equipped with appropriate cell safety systems. They accurately and effectively perform operations programmed for them in production environments, where speed, repeatability, and precision are crucial.
At Aiut, we design comprehensive solutions for automated robotic welding, from simple, standard robotic solutions to more sophisticated robotic cells. The implementation of welding cells is carried out by adjusting them to the individual needs of the customer each time.
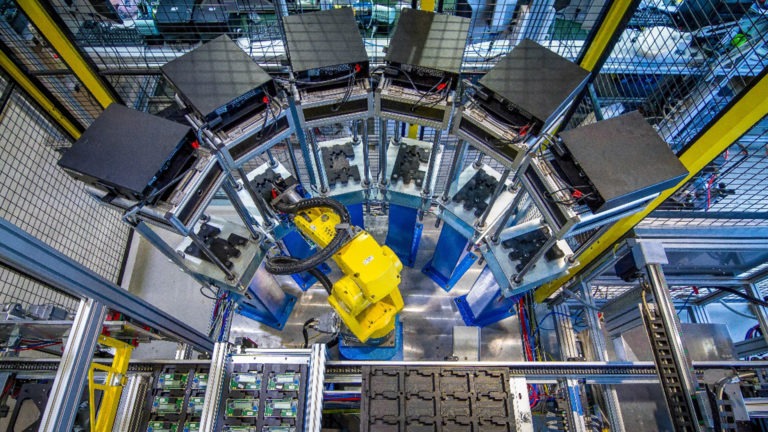
How is the robot work cell designed?
A robot cell design requires a thorough and precise analysis of the client's production process. Based on this analysis, suitable robots and necessary equipment are designed. For example, these could be vision systems that enable the recognition of elements, transmitting their coordinates to the robot, which can then recognize and sort them accordingly. Integration with equipment is ensured by software embedded in the robot. Deploying robotic cells are then tested to ensure safety standards and an effective robotic cell.
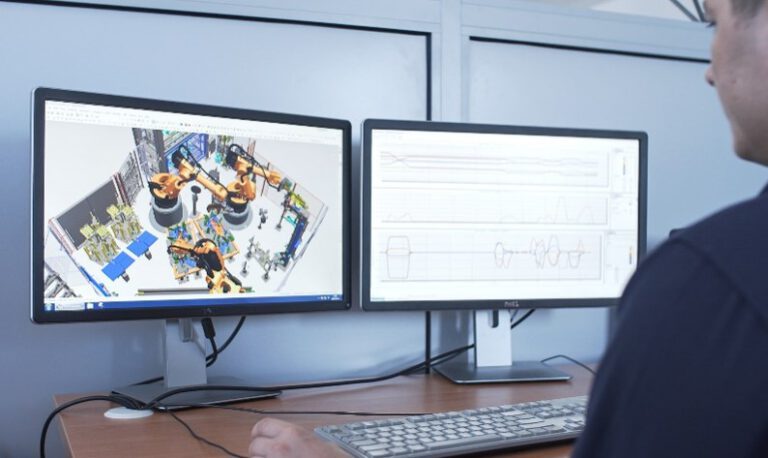
What are robotic work cells used for?
The use of robotic cells brings many benefits to manufacturing companies. Firstly, they enable increased productivity through process automation, resulting in faster production and shorter cycle times. Secondly, they ensure uniform and repeatable quality of manufactured products. Additionally, robotic cells allow for the optimization of raw materials and energy consumption, leading to reduced production costs. Furthermore, they provide comfort and safety by relieving people from tedious, monotonous, and dangerous tasks, such as welders exposed to prolonged work in hazardous conditions.
Benefits of industrial robotic cells:
- High, repeatable quality of execution
- Increased efficiency and productivity of the production facility
- Accuracy and speed of process execution
- Ensuring production continuity and minimizing downtime
- Robots provide production 24/7
- Minimization of human errors
- Meeting the growing demand for welded products
- Versatility of robots through the selection of appropriate software
- Raising standards and safety in the workplace

What robotic welding technologies are used in the industry?
Resistance spot welding
Resistance spot welding, also known as spot welding or electric resistance welding, is a process that involves using electric current to generate heat. As a result, the metal melts, leading to the joining of two elements. Industrial robot cells for resistance spot welding are equipped with special electrodes that press materials together and generate current, creating a durable connection. Parameters of the cell in this process that can be adjusted include welding current intensity, current flow time, and electrode pressure.
Projection welding
Projection welding is a type of resistance spot welding in which materials are heated using friction. Robotic cells for projection welding utilize properly programmed robots that precisely control pressure and movements to ensure effective material bonding.
MIG/MAG welding
MIG (Metal Inert Gas) or MAG (Metal Active Gas) welding involves joining materials using an electric arc maintained between a conductive wire and the workpiece. A shielding gas is supplied through the welding torch - inert gas for MIG and active gas for MAG. The arc melts the welded material, forming a weld seam. Industrial robot cells for MIG/MAG welding utilize advanced welding robots that precisely control the process, ensuring uniform and durable connections.
Laser and hybrid welding
Laser welding utilizes a high-energy beam of laser light to melt materials and create connections. Thanks to the highly concentrated heat source, laser welding of thin elements achieves high speeds, and in thicker materials, it can produce deep and narrow seams. Robotic cells for laser welding are equipped with precise optical systems and advanced control systems that enable precise guiding of the laser beam. Laser welding technology is used in remote locations that are difficult to reach. It can also be used in high-volume applications requiring increased precision in industries such as automotive and transportation, electrical and electronic, aerospace, and defense.
Hybrid welding combines the advantages of laser welding and MIG/MAG, allowing for high-quality connections while increasing process efficiency.
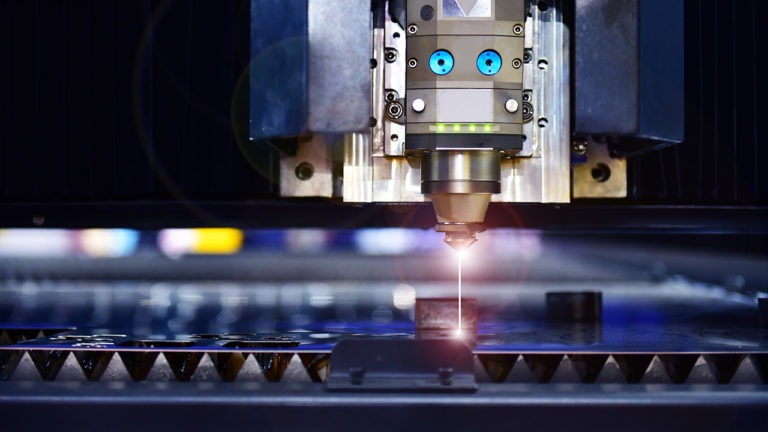
Fronius Poland Partner Program
AIUT has been granted Authorized Integrator PARTNER status within the Fronius Poland Partner Program, a market leader in robotic welding systems. Closer collaboration will accelerate the scope of welding solutions offered by AIUT, through the implementation of the latest robotic welding technologies and applications. Learn more here.
Robotic integration services — designing workstations integrated with AMR Robots
As an integrator, we collaborate with the leading companies in the robotic welding market, such as FANUC, Kuka, ABB, etc. In addition to implementing robotic cells for welding, we also create autonomous mobile robots from the F series to further increase the efficiency of production and logistics processes. This is possible because our AMRs can deliver products to robotic cells, providing the necessary materials for industrial robots to perform tasks. Additionally, we design collaborative robots (cobots) that are integrated with different robot arms. Below, you can see our autonomous mobile robot F23 with applied robotic arms from the aforementioned companies, which we presented at last year's Warsaw Industry Week.
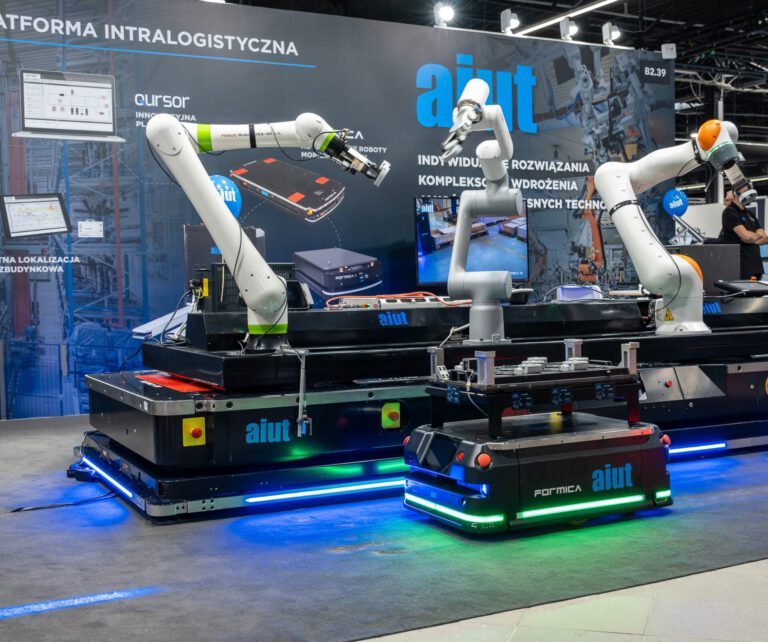
Summary
Robotic cells constitute essential tools in today's industry, enabling manufacturing companies to achieve greater productivity and efficiency. By leveraging advanced welding and joining technologies, these innovative devices contribute to improving quality, increasing productivity, and reducing production costs. Additionally, integrating production processes with autonomous mobile robots allows companies to achieve an even higher level of automation solutions and maintain a competitive position in the market.
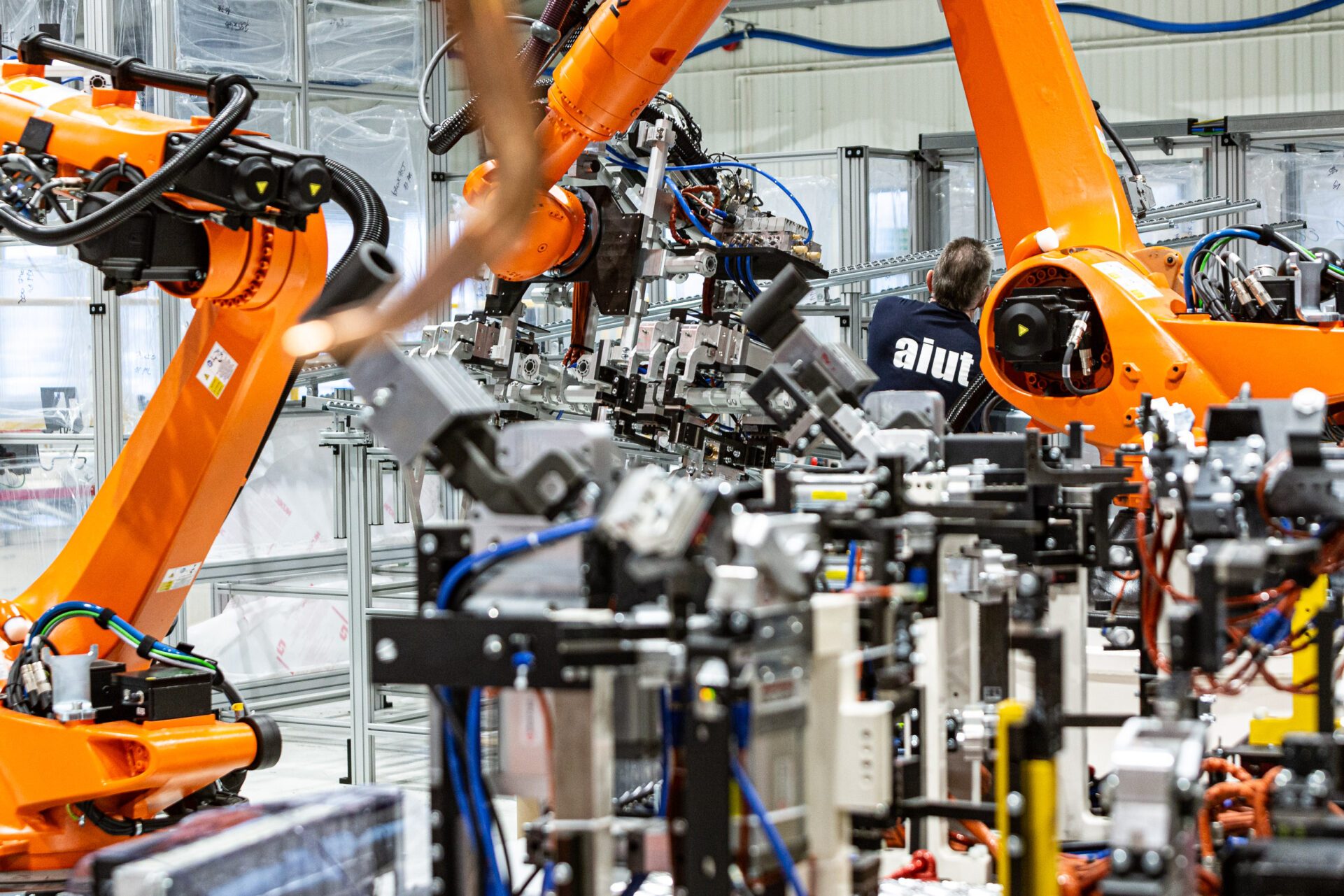
Are you looking for a custom robotic work cell for welding at your facility?
We are a system integrator in the field of industrial automation and robotics. With 30 years of experience, a team of 700 engineers, and over 4500 projects completed worldwide, we utilize the latest robotic welding technologies to provide reliable and precise automation and robotic solutions. We support our clients in increasing the efficiency and quality of their welding tasks.