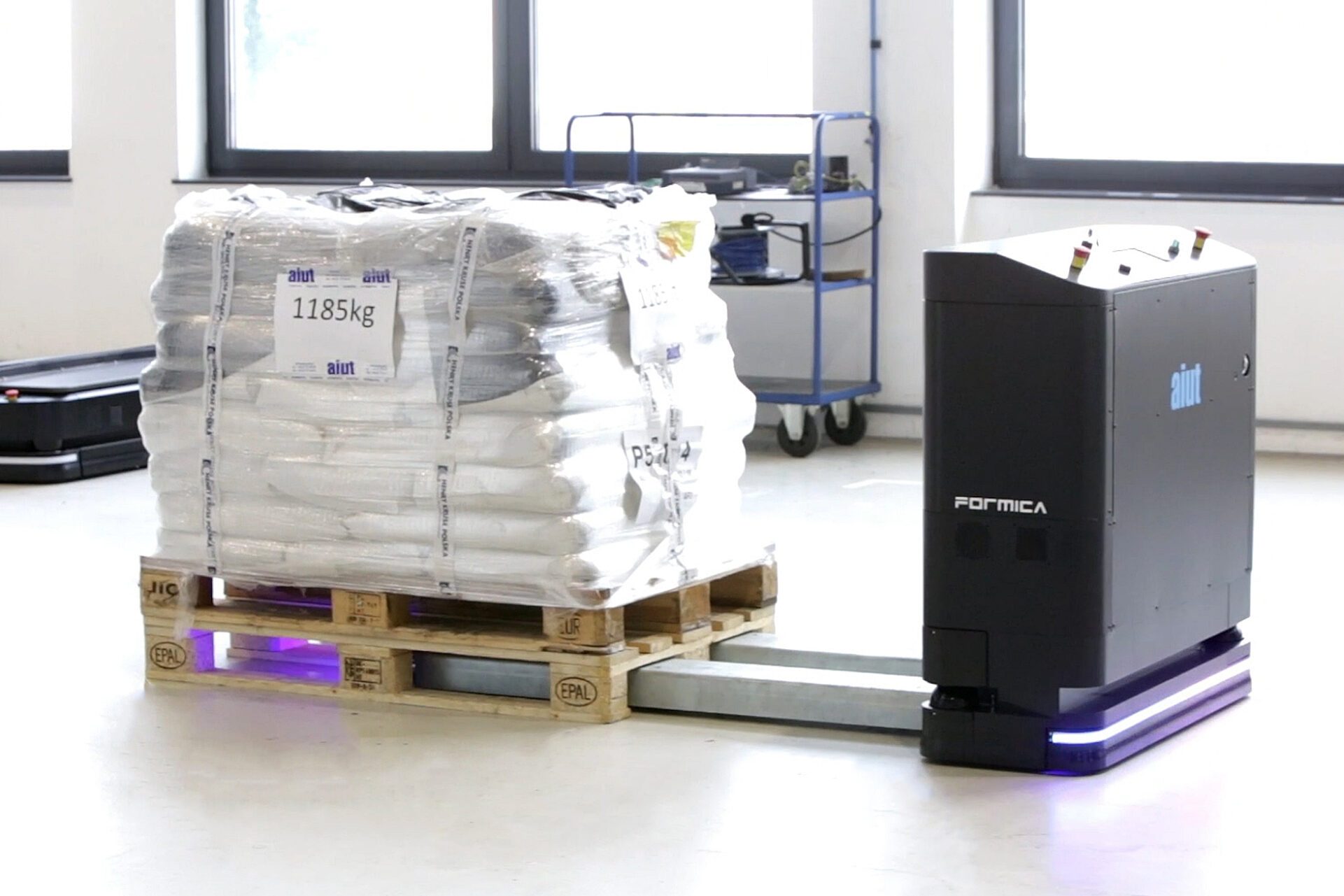
- AIUT new robot for heavy load transportation
AIUT new robot for heavy load transportation
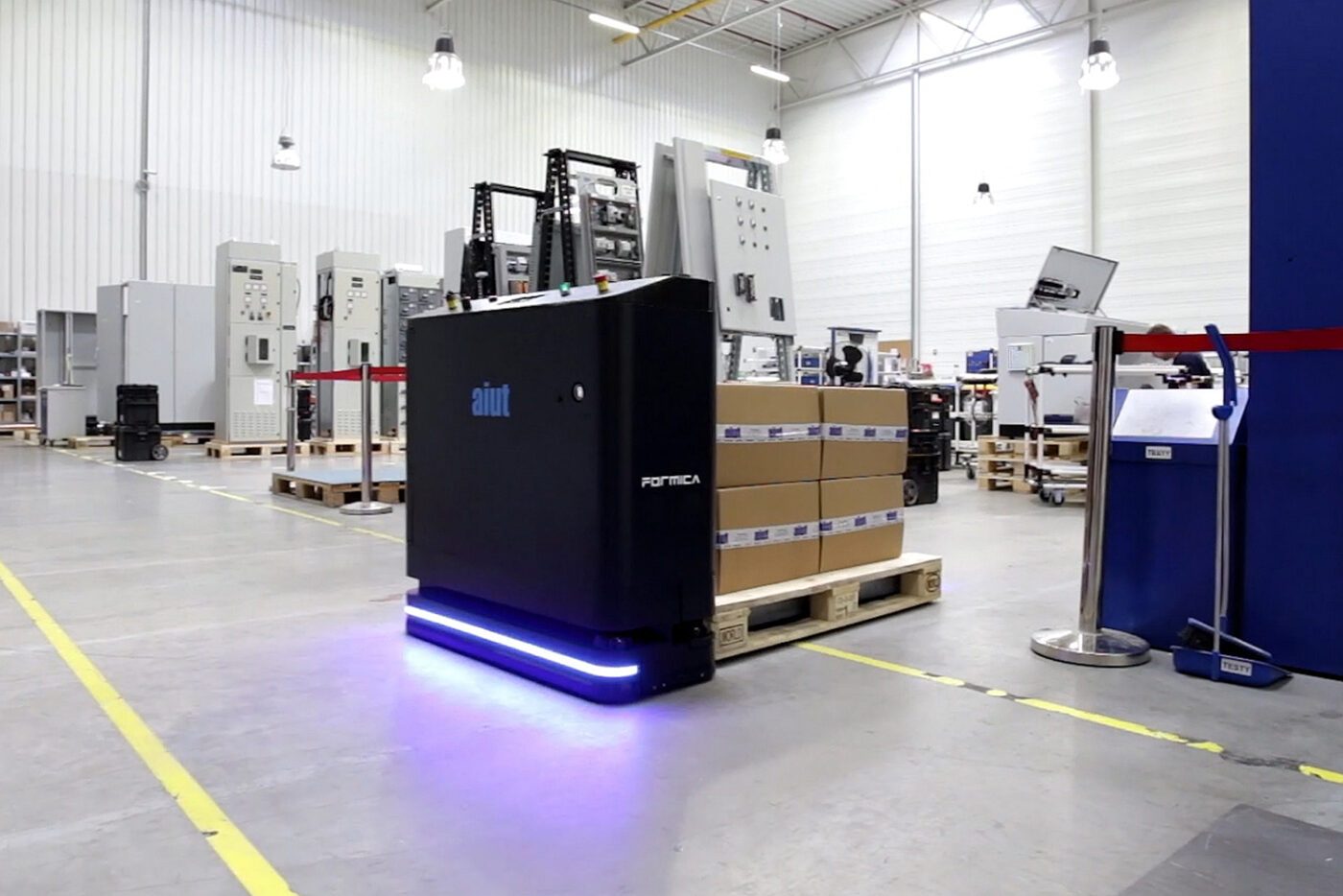
AIUT Formica family of autonomous mobile robots grows bigger with the new Formica 2 - an intelligent vehicle for heavy load transportation (of up to 1,500 kg), equipped with pallet jacks.
Formica 2 automatically and independently picks, transports and delivers heavy pallet loads up to 1.5 tonnes in a dynamic environment, providing a safe alternative to traditional forklifts.
Automatic transport of large loads
AIUT new robot enables full automation of palletized cargo transport. It allows for managing intralogistics more effectively throughout the supply chain. Formica 2 ensures safe transport of heavy and non-standard (including high) loads, improving the execution of orders in warehouse and production spaces.
Safe deliveries without operator intervention
Thanks to the use of advanced technologies and artificial intelligence (AI) algorithms, AIUT provides its robots with even better navigation. No changes to the plant space are needed. Safety and vision systems allow Formica 2 to traverse throughout a dynamic environment without collisions. The robot detects people and avoids other non-standard obstacles. Built-in weight distribution sensors give vehicles full control of heavy and high loads.
- We equip our autonomous mobile robots (AMR) with advanced, certified safety systems to guarantee full control of the area where Formica 2 operates. This allows the staff to work without any disturbance in the vehicle activity space. Formica 2 also predicts and avoids high-traffic zones and excluded areas. Moreover, advanced analytics allows robots to predict various events – explains Jerzy Greblicki, director of Radical Automation Division at AIUT.
Full control and collision-free deliveries
Formica 2 robots independently adapt the delivery route to the actual traffic volume on the factory premises. They also avoid sudden obstacles and adapt their speed to the weight and dimensions of the load - all to deliver cargo without mistakes or collisions. Additionally, each AGV / AMR AIUT can be supplemented with a unique BlackBox module equipped with a camera system to record vehicle operating parameters, and an IMU module that verifies vibrations, overloads and external impacts, providing full insight into the robot's work log, with the possibility of reviewing the events.
Quick implementation. No changes to the plant space needed
The extensive free navigation system, based on LIDAR technology, allows the robot to create a virtual map of the working environment and track traffic in its vicinity to select the optimal route - without interfering with the plant infrastructure. The vehicle makes decisions based on the actual traffic volume and information from the fleet management system, adjusting its response to the situation (it may, for example, slow down, stop, change the route).
- We are talking about machines that can be quickly and fully integrated (even while working remotely) with a robotic production line or another robot. Machines that can communicate with each other and flexibly react to events in real-time. Devices that are safe while cooperating with the human staff. Robots that ensure stable logistics processes and reduce costs. Importantly, the support these robots introduce where the number of employees is insufficient becomes crucial for ensuring continuity of production and execution of orders - Jerzy Greblicki adds.