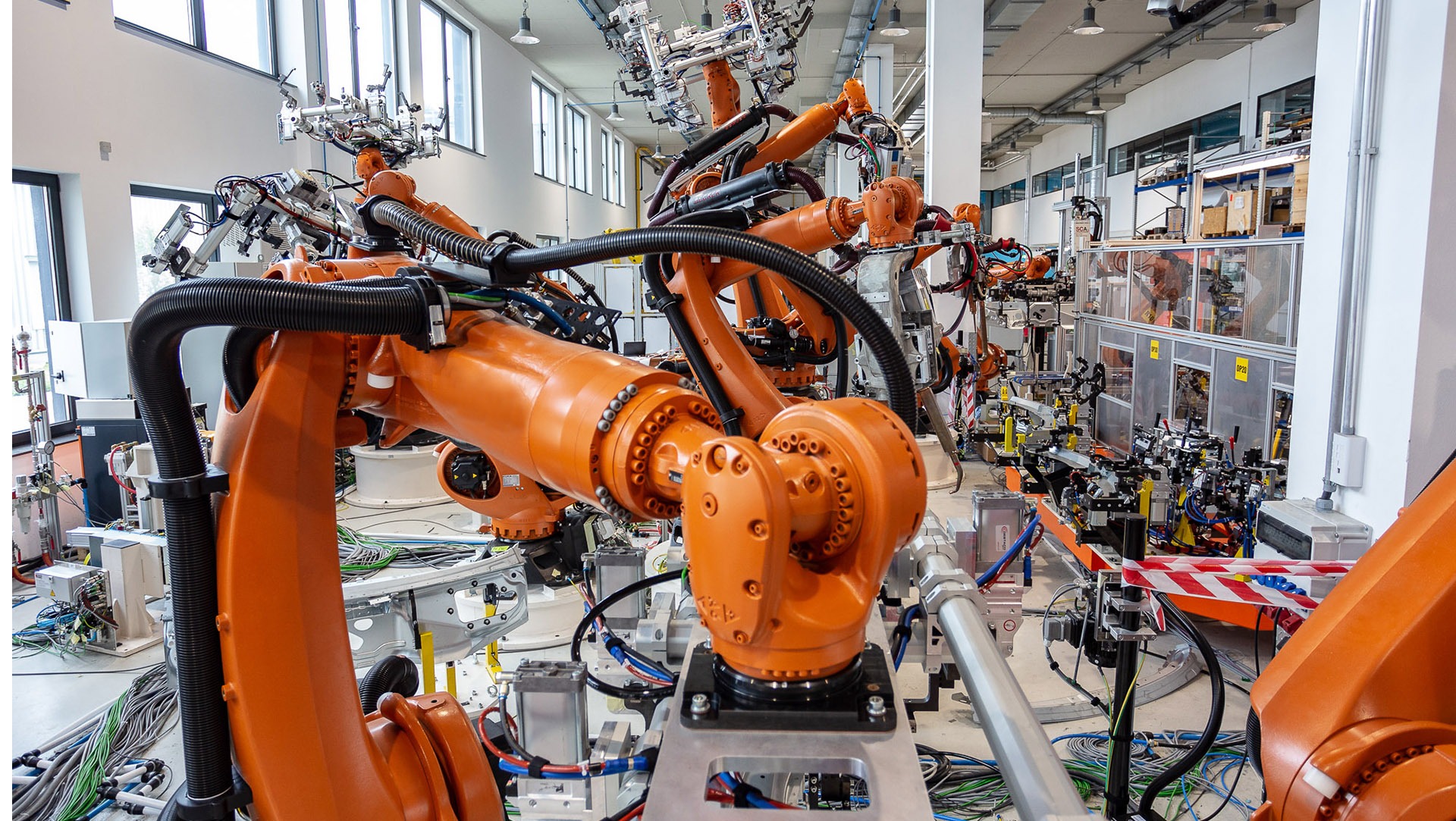
How to ensure the safety of a machine park?
It has long been known that ensuring the safety of employees in companies with a machine park is a priority and highly regulated from a legal standpoint. Each machine or device must meet the relevant standards as well as the safety requirements of the Machinery or Tool Directive. Although the trend toward continuous improvement of safety in facilities is strongly visible in the market (e.g., in the increasing number of conducted machine safety audits), the incident report from Statistic Poland (GUS) still indicates that the issue of accidents at work exists. According to GUS, the incident rate, describing the number of injured persons per 1,000 employed, decreased from 5.10 in 2021 to 4.66 in 2022. Below is shown what it looked like for individual sections in 2022.
Comparing preliminary data of incident reports from the first half of 2023, it turns out that there has already been a 1.8% increase in accidents at work compared to the first half of 2022. The manufacturing industry still has one of the higher rates, so this raises the question – what actions should be taken to increase and ensure the safety of a machine park in factories?
What is a machine park?
A manufacturing company, to carry out its technological processes, requires specialized equipment and machines tailored to its technological processes. The collection of them creates the so-called machine park, which the company manages, i.e., utilizes, to implement its adopted strategy. Manufacturing companies are required to regularly inspect the technical condition of their machines. Such actions ensure the highest quality of the produced goods, high production efficiency, prevention of costly breakdowns, and, more importantly, guarantee that the daily operation of machines becomes safer for the employees.
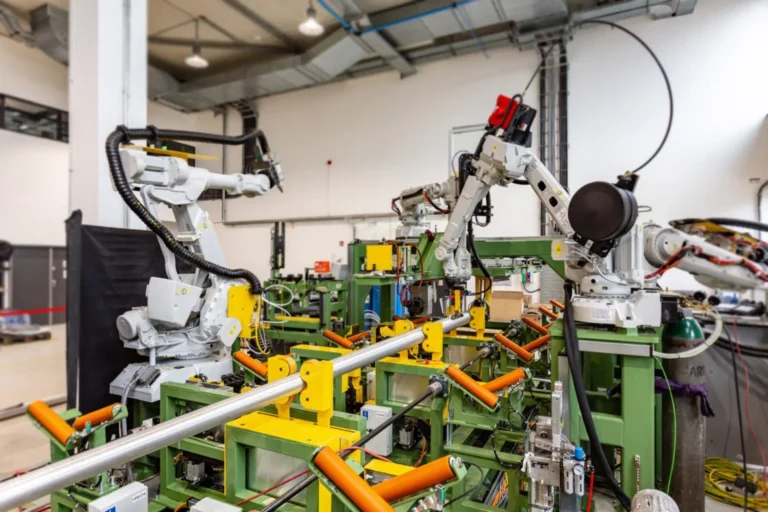
How to increase the safety of the machine park? Below some safety tips to follow in your factory.
1. Machine park safety audit
A machine park safety audit is a process of assessing and analyzing the work environment where various types of machines, equipment, and systems are located. The main objectives of conducting the audit are:
- identifying risks for machine park hazard prevention.
- checking whether machines and machine park safety features meet technical requirements.
- verifying machines and equipment conditions for compliance with standards.
- analyzing the machine park safety regulations (procedures, standards, operating instructions) and verifying employee training in their application.
- modernizing the machine park, restoring efficiency and performance of the equipment.
- developing recommendations and machine park safety tips
- creating an individual protection strategy with a plan ensuring the continuity of the production cycle.
The benefits of regular inspection and maintenance of a machine park:
- increased safety for employees.
- ensuring high quality of manufactured products.
- reduction of downtimes, repair costs, and minimization of losses.
- maintaining production continuity.
- ensuring high efficiency of the machine park.
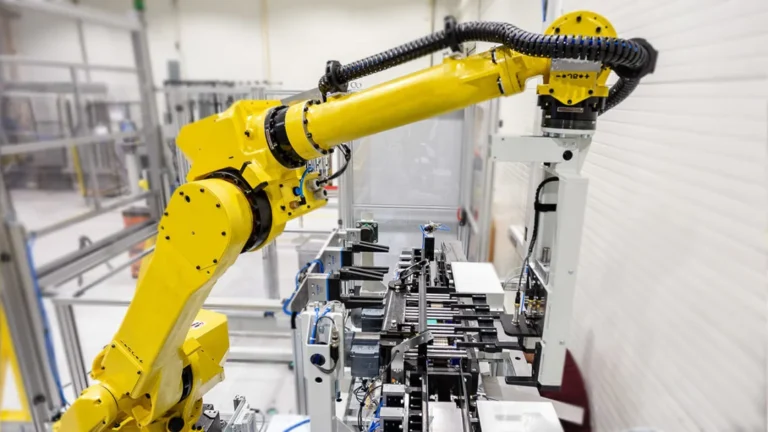
2. Machine park safety rules. Education and implementation of occupational health and safety principles.
In addition to regular audits of the machine park, education is a crucial aspect of improving safety. Employees should be thoroughly trained in the daily operation of machines, applicable procedures, and the identification of potential hazards. Safety and health at work (OSHA) training should be regularly refreshed and adapted to changing conditions and technologies. Organizations must establish clear and consistent procedures, work rules, and minimum safety requirements. This ensures that employees know, among other things, what emergency procedures are, how to use them, how to report machine safeguard problems, and what steps need to be taken in the event of a workplace accident. Additionally, employees should be required to wear proper protective clothing and equipment, for example, safety shoes, helmets, or gloves, to enhance workplace safety.
3. Key stages in machine design impacting the safety regulations of work areas
Fundamental when it comes to ensuring the safety of a machine park is the design stage, with full identification of hazards and a detailed analysis of the labor risk assessment. It is carried out individually for each machine, taking into account the specific environment in which it will operate and the processes occurring in production. In the later stages of project implementation, suitable methods and solutions are selected to ensure a safe working environment that mitigates the initially identified risks. The final confirmation that nothing poses a threat to operating the designed and built machine is the validation of safety systems.
A very important aspect is the already-mentioned analysis of the target working environment. Machine tests for proper operation of safety devices (such as scanners or optical barriers) conducted in workshop conditions may not always reflect the actual working conditions in production halls. This may mean that certain safety standards will change. For example, a high level of air pollution that can occur in a factory directly affects the operation of scanners, thus influencing the selection of safety measures or the determination of parameters.
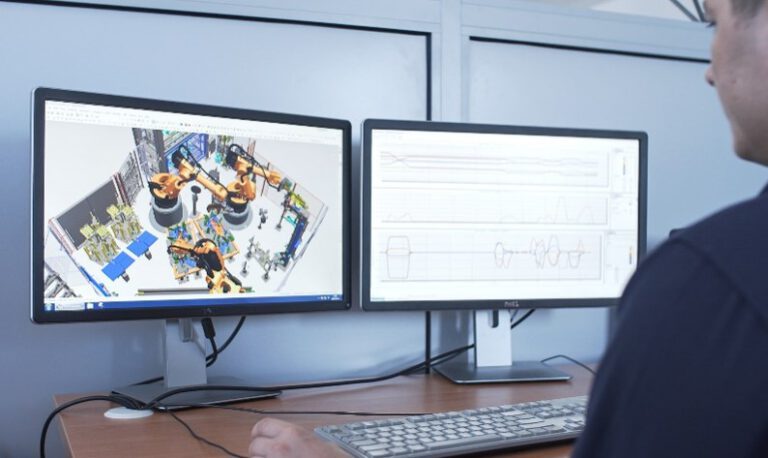
4. Systems for improving the safety of the machine park
- Visual monitoring systems that provide monitoring of the entire machine park and detect hazardous situations.
- Access control systems that prevent accidental and unauthorized entry into restricted zones or machine operation areas.
- Safe machine interlocks that prevent the start-up of devices, for example, during maintenance work.
- Automatic machine shutdown systems that activate in cases of threats, overloads, or detection of anomalies in machine operation.
- Intelligent data analysis systems utilize artificial intelligence protocols to monitor behaviors, establish patterns, and proactively respond to potential dangers, such as deciding to shut down a specific machine or robot.
- Real-Time Location Systems (RTLS) that monitor the movement of resources in the factory in real-time, allowing for responses to undesirable events (e.g., forklift exceeding speed limits, unauthorized entry into a zone, improperly occupied workstation). Learn more about AIUT's intralogistics platform Aformic and the indoor location solution offered by AIUT.
5. Innovative solutions equipped with appropriate safety measures
Continuous technological progress enables highly efficient and increasingly dynamic automation of production processes. More and more companies are introducing innovative solutions for the automation of production processes, such as industrial robots, mobile AGV/AMR robots, or collaborative robots (also called cobots), about which you can learn more in the blog post linked here. While striving for the automation of production processes, it is crucial not to forget that ensuring the park workers' safety remains a top priority.
For example, although cobots are designed as safe devices to collaborate with humans, the tools they are equipped with and the significant elements they handle can impact the safety level of the entire workstation. Such information must be taken into account in the risk assessment to ensure that a specific application using a collaborative robot is safe and functional.
Thanks to technological development, industrial machines or robots are increasingly equipped with appropriate sensors, further enhancing the safety of a machine park and the comfort of working with such devices. Robots are equipped with safety systems with features such as motion restrictions or stops on collision paths with humans. An example of their application can be seen in Formica AMR robots. They are equipped with safety bumpers to stop the mobile robot in case of collision and safety laser scanners that, with the help of LIDAR (Light Detection and Ranging) technology, detect the distance from specific objects.
Learn more about how the Formica AMR robot is built here.
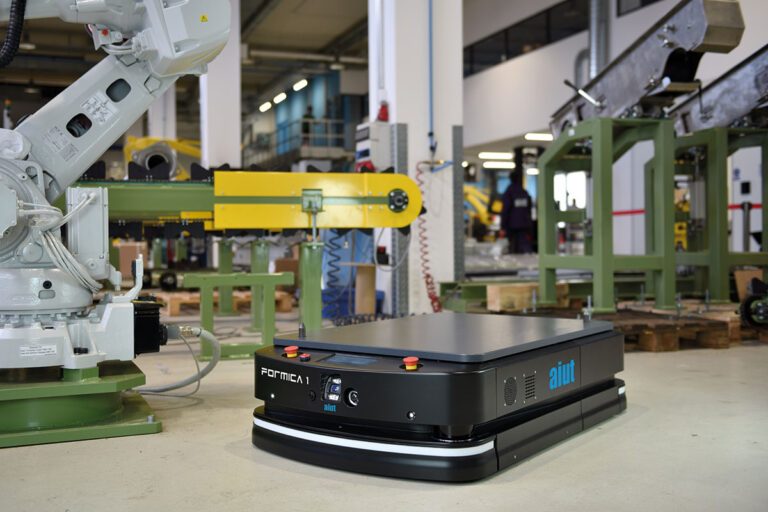
Summary
Regular inspection and maintenance of machine parks and implementation of health and safety procedures should be a priority for the functioning of every factory. Organizations must invest in employee education and ensure that machine park safety regulations are well-known to employees. Furthermore, they need to review equipment safety to see if they meet appropriate standards. All these actions will help create a safe working environment, maintain the machines' high efficiency, and eliminate production hazards. With technological progress, various safety systems are available, and machines are equipped with increasingly sophisticated safeguards. A crucial tool in preventing accidents and maintaining the high technical condition of machines is the regular analysis of machine park safety conducted during audits.
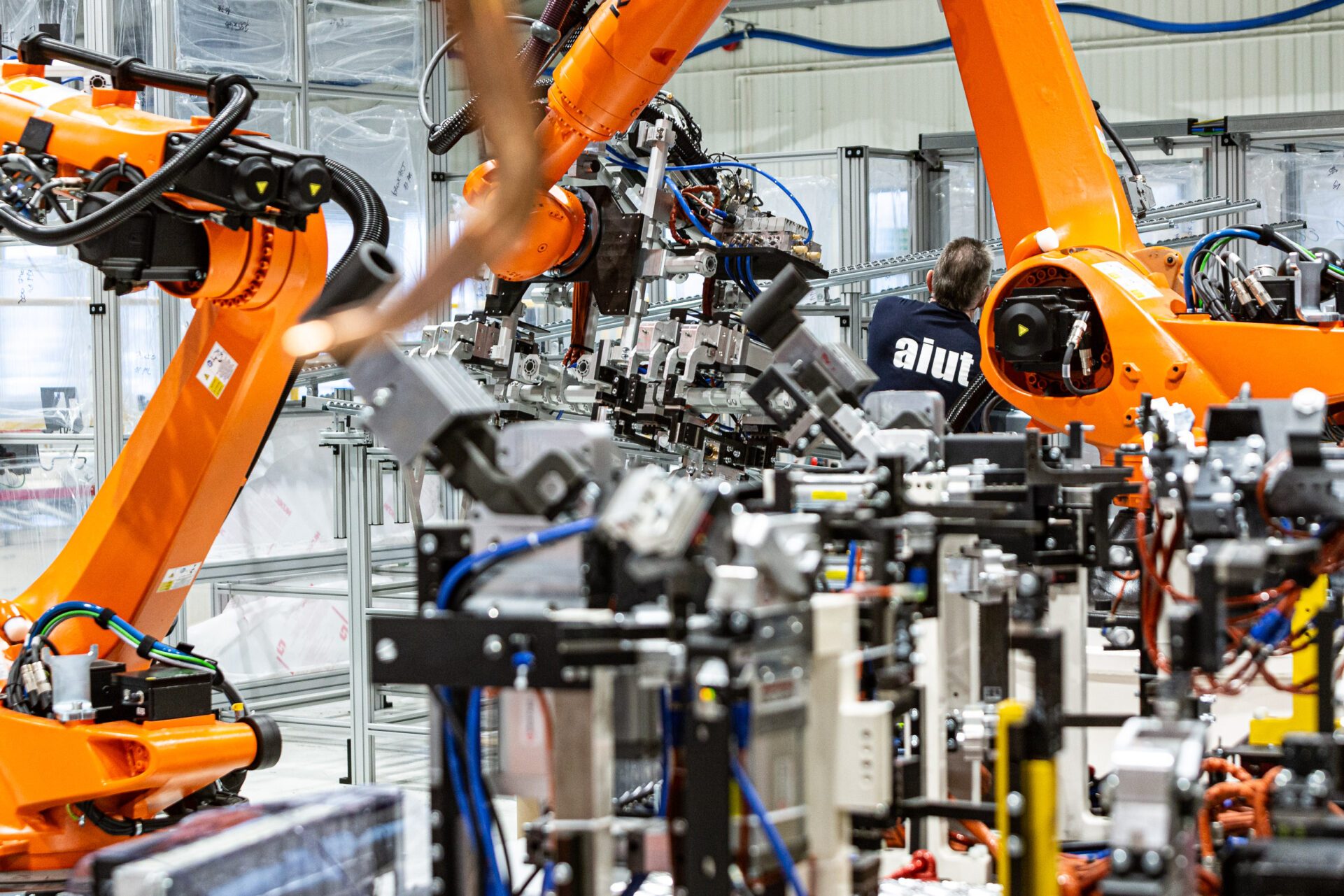